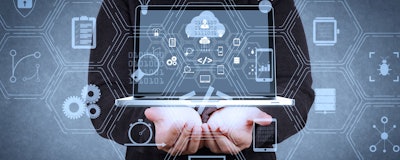
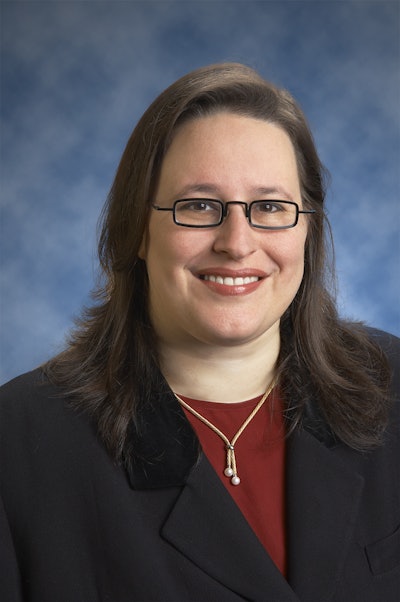
As any product manufacturer will likely testify, there is a big difference between a pre-production pilot program and moving to actual full production of a product or part. Indeed, for manufacturing companies that are embarking on or expanding serial or limited quantity production using 3D printing (additive manufacturing), several important aspects must be considered. More specifically, it’s worth thinking very carefully about the software aspect of the deployment. One might argue that this aspect is so important that it should be included in the pilot program itself.
Let’s think about this transition from pilot to production. When you move into manufacturing you move to a corporate grade process. Such a process needs to meet certain criteria: it needs to be automated, seamless, secure, and completely repeatable. None of this is possible, when your process includes manual steps or does not include secure, corporate-grade, end-to-end software solutions.
Basically, it’s no different than other aspects of an organisation: the IT department checks, deploys, and operates integrated systems that ensure smooth and secure end-to-end systems that form the backbone of the corporation (such as ERP). Other platforms integrate with this backbone and this way there is uniformity across the organization making sure purchasing and finance, for example, are in sync. The same should apply to manufacturing processes—they should be integrated and play well with the other functions in the organizational infrastructure.
Silent yet Crucial
At LEO Lane, we like to say that software works best when you don’t feel it. It’s there in the background, seamlessly making sure everything happens correctly and securely without bothering the user or anyone unrelated to it in the process. A simple example of this is the virus scan on your email – if it’s a good one you never need to do anything with it and yet it performs a vital function without which your email would be a danger zone and literally unusable.
As well as allowing for a repeatable, automated, process, software also offers other benefits. In a fast-paced changing industry, it’s important for processes to have the flexibility to adapt continuously. Good software solutions, and especially cloud (public or private) solutions provide exactly the adaptability needed for this scenario. It’s important to check that the solutions you choose are real SaaS cloud solutions (rather than an on-premise solution that is installed on a cloud server but still has all the drawbacks of on-premise software). Many software platforms also allow for add-ons that can provide added functionality on their own or from other vendors later on. In the additive manufacturing ecosystem, we already see such platforms that started from the direction of ERP, MES, workflow, and even PLM. All these platforms need to talk with each other to be effective.
In addition, although sometimes the unsung hero (or villain, as the case may be), the software that drives the 3D printer is especially important. A good printer driver integrates with (or allows integration to it from) other software solutions, thus enabling a full end-to end process. This makes a big difference in the user experience of the 3D printer, its perceived functionality (as opposed to its physical functionality), and in the printer set up.
Check List
Having established that software should be chosen carefully and early, what else should we check to help achieve our seamless and automated criteria? The additive manufacturing ecosystem is quite fragmented and that also goes for software. There isn’t one platform that gives you everything, so it’s wise to make a list of all your corporate grade needs. See which of them can be covered by existing IT infrastructure and for which you need something special for additive manufacturing.
For example, when moving to virtual inventory the files (digital assets) need to be managed and backed up. There are plenty of excellent file management and backup systems available and there should be no difference in handling additive manufacturing files from other important files. That said, there are tasks and platforms that are specific to additive manufacturing. Here specialized solutions are needed and their ability to integrate easily and abide by cooperate policies and procedures should be added to the checklist.
In the virtual inventory example above, this would include making sure the existing infrastructure can be managed as is by the users of the additive manufacturing workflow software, allowing the file redundancy and back up to happen automatically. Forward thinking companies will include security, IP Protection, and consistency enforcement as part of these AM-specific solutions. Another aspect to consider is quantity control. IP Protection and quantity control are problems arising directly from virtual inventory and need to be addressed specifically.
Once you have your list and candidate software solutions to complement the parts missing in the organization, it’s time to choose specific software solutions and put the platform together. Remember, what might be sufficient for a pilot, won’t work in production, simply because it’s not sustainable, repeatable, or scalable. It’s therefore wise to consider these aspects already at the pilot phase.
To Production and Beyond!
I believe that when these software considerations are included as part of the planning for the initial pilot program, the resulting pilot is more valuable and the move to production much smoother. If the solutions chosen are friendly to other software and integrate easily with them, the pilot can simply be turned on to production at the point of deployment. In addition, there’s an obvious advantage to having a better idea in advance of the final costs to be incurred in full production. Ultimately, with smart planning and the appropriate software, corporations can position themselves to not only harness the benefits offered by additive manufacturing, but to do so quickly and efficiently.
Lee-Bath Nelson is co-founder and vice president of business at LEO Lane and can be reached at [email protected]