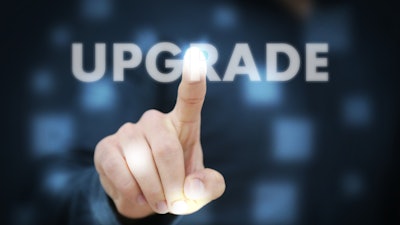
Enterprises face several challenges related to digital transformation. Connectivity is a significant problem due to legacy technology silos, differing data formats and a lack of interoperability. Digging into connectivity issues, in many instances, machines on the plant floor have air gaps, making it extremely difficult to extract data to move processes to the cloud to perform analytics, derive intelligence and add business value.
There are multiple reasons why air gaps exist. One might be intentional security measures to isolate devices, preventing them from establishing an external connection with other computers or network devices. Air gaps could also exist because there is no network switch connecting IT and OT devices, keeping them from talking to each other. In many cases, air gaps exist due to the lack of standards and APIs that enable systems to interface with each other.
Cost is another legacy barrier to digital transformation, as these initiatives often require significant investments in technology, enterprise level licensing, specialized talent and improving infrastructure.
Technical debt often impacts older facilities using legacy systems and processes not easily integrated with new digital solutions. Migrating away from these systems can be complex and time-consuming. The cost of the infrastructure improvements and the actual products on top of that alone is substantial, so balancing these costs with the expected returns can be a challenge, especially for smaller organizations.
Confronting the Skills Gap
As the older workforce retires, knowledge gaps can emerge. This presents a challenge for organizations to focus on onboarding and attempt to advance digital transformation. Modern HMI visualization technologies shortens the onboarding process, accelerates digital transformation, and provides opportunities for new staff with different skill sets that better align with modern HMI visualization technologies. Furthermore, there are opportunities to uplevel existing experts through training for them to be fully conversant with new products and technologies.
IT-OT convergence is a common issue to be considered when organizations are looking to advance digital transformation using HMI and visualization software because it involves aligning different objectives, technologies, cultures and security considerations. Overcoming these limitations requires careful planning, collaboration and a strategic approach to bridge the gap between IT and OT domains.
The smoother the IT-OT convergence is, the tighter those teams collaborate, the more likely that the end customer is going to be successful.
Scalability presets yet another challenge as it involves careful planning, resource allocation, cost management and technical considerations. Organizations must address these factors to ensure scalability of their digital systems to meet growing demands and perform optimally under heavy loads for long-term success.
Accelerating Digital Transformation
There are several specific qualities and features particularly important in visualization and HMI platforms that accelerate digital transformation in manufacturing, not only in terms of production, but also with design and maintenance.
Manufacturers are constantly looking to minimize downtime, maximize the production of good products and eliminate bad products and wastage. On the production side, HMI is the key interface that provides operators with a live snapshot of what is going on in a machine, production line or system. HMI essentially connects the plant floor, the machine, the system, the production line and any higher-level channels that might be used for data analytics.
Driving this connection is visualization software, the beating heart of operations. The data collected needs to be presented to operators in a format that’s understandable and actionable, with outputs customized to deliver data appropriately for a particular operation. Extensibility is a major factor in this. Traditionally, HMI was seen as having a specific function or role on the plant floor when it came to digital transformation. However, this evolved with the advent of Industry 4.0 and the connected enterprise, when fully integrated systems became of paramount importance, and the evolution into Industry 5.0.
It is here the flexibility, scalability and extensibility of visualization software, the ability to communicate to multiple controllers and multiple systems, becomes a primary enabler for digital transformation using IoT protocols. OPC Unified Architecture (OPC UA) or Message Queuing Telemetry Transport (MQTT) would be prime examples.
Access to historic data is a crucial factor on the runtime side, essentially digitizing what used to be tracked manually on the plant floor. A core consideration when selecting visualization software is an integrated data logger or historian that allows data to be digitally historized, with access provided to operators as needed to operators, as well as to higher-level systems at the enterprise.
Real World Collaboration
Moving to the design side of manufacturing, HMI and visualization software accelerates digital transformation by delivering a collaborative development environment and the ability to leverage SaaS cloud-based tools to enable new business models. End users can be connected with their design development team, often consisting of multiple designers working on the project simultaneously, enabling collaboration, flexibility, security and transparency, regardless of location.
HMI tools also allow developers collaborating on code to use a centralized repository like GitHub for code management and version control. It integrates design tools and code within an HMI interface, enabling collaboration. Users can merge changes seamlessly, avoiding duplication of efforts.
The centralized environment provides a comprehensive view of project status, change history and version control, which aid transparency. HMI tools enable OEMs to collaborate externally as well as with customers or partners to share ideas, troubleshoot and evaluate applications. Designers benefit from creating reusable code libraries in this repository, promoting trust and efficiency. They can easily incorporate trusted code modules into their applications, enhancing differentiation
Finally, HMI and visualization also support digital transformation with machinery maintenance, empowering operators with remote access. Issues can be flagged, and notifications sent to maintenance engineers, and integrated chat tools and screensharing capabilities connect on-site operators with remote technicians to relay issues and maintenance solutions. Together, they identify and make changes, saving these changes in the cloud repository for updated application versions.
Looking ahead, as OEMs and system integrators look to adjust their business models or create new ones and build the infrastructure to support cloud-based connectivity and monetize that, there are opportunities for them to partner with automation solution providers. While HMI tools and visualization software are central to the digital transformation of manufacturing, other tools are essential to form a complete system. Embracing these technologies is necessary for manufacturers to optimize operations, enhance quality, reduce costs and stay competitive in today's data-driven world.