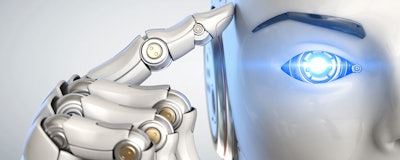
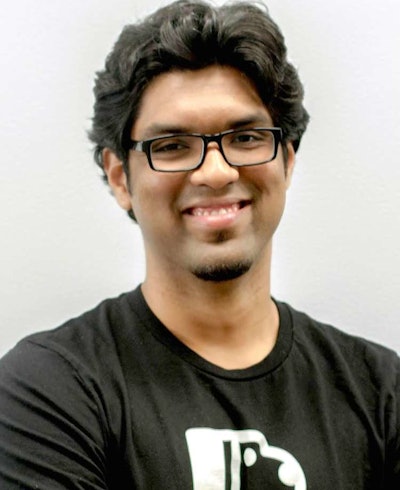
No one needs to tell manufacturers that they need to become more nimble and efficient. This is especially true for process manufacturing companies that operate expensive assets. In addition to the regular onslaught of business pressures, manufacturers are also facing the prospect of a global trade war. In response, manufacturers are now looking to artificial intelligence (AI) and machine learning (ML) for help, having seen the benefits other industries have gained using these technologies.
To clarify the terminology, AI is the goal that needs to be achieved and ML is a vehicle to get there. AI has a lot to offer, especially to manufacturers. The insight it provides can help address critical process and asset performance questions for manufacturers that have previously been difficult and time-consuming to fully answer. For example, if a manufacturer needs to add or change specific operations, what impact will these changes have on the life of the underlying assets? What aspects of operations offer opportunities for increasing throughput efficiency? Can changes be made that will increase the life of a critical asset?
The timing for AI adoption in manufacturing could hardly be better, because many manufacturers are also evaluating and implementing Industrial Internet of Things (IIoT) systems as part of their larger digital transformation effort. IIoT combines sensor data with information from databases, computers and other systems to make operational processes much more efficient. When combined with AI, IIoT can have a much larger impact on an organization than it could alone, providing deeper insights in far less time than do traditional processes.
AI and IIoT — A Natural Fit
To date, most of the attention given to IoT has focused on consumer products, such as connected homes and appliances. But while IIoT may not have yet captured the public’s imagination, it’s a fast-growing market. According to consulting and IT services firm Accenture, IIoT could add $14.2 trillion to the global economy by 2030.
That said, the IIoT market is not yet mature, and many manufacturers still depend on inefficient legacy technologies and processes. For example, in the beverage industry, it’s common for a single process analyst to be responsible for assets at up to a dozen plants or more. Getting data on asset performance using legacy tools is a tedious and complicated task, because each plant has multiple different software systems housing data on aging on-premise systems. So, because industrial plant operators can’t get the specific answers they need from data in a timely fashion, they are forced to make decisions about asset management based on their on-the-job experience and whatever information their clunky tools can gather.
It doesn’t have to be this way. With modern technology, process analysts can effortlessly extract data from their own systems and then analyze that data to gain a higher level of data intelligence that will make a significant difference in a plant’s performance.
With IoT in place, assets are continuously sending data about key performance indicators. This is valuable information that can alert management in real time about potential issues. But while most IoT platforms can track and perform some analyses on this information, to unearth the most valuable insights, manufacturers will need to apply a more sophisticated approach using AI.
Together, IIoT and AI can address the weaknesses of the legacy systems that are still so prevalent in industrial or production settings. When IIoT data is combined with the large volumes of readily available historical and real-time information within plant systems, AI can pinpoint blind spots that were previously unknown to analysts because they have not been able to link all of this data together. As a result, plant management can highlight processes that are having an outsized impact on shortening asset life, discover process inefficiencies that are reducing throughput, and identify new opportunities to reduce downtime. Most importantly, IIoT and AI help ensure that plants meet and exceed their business goals.
Finally, adopting IIoT and AI technologies doesn’t just improve efficiency and profitability, it can also help with recruiting key talent. Millennials and Gen Zers are digital natives who have grown up knowing that any information they desire is accessible in seconds. They’re going to be extremely frustrated working in a legacy environment where the data they need is either inaccessible or non-existent. Those manufacturers that take their digital transformation seriously and deploy technologies like AI and IIoT will find it much easier to attract the employees they want, because recruits will know they’ll have access to the information that they expect.
By deploying IIoT and AI together, manufacturers can move away unreliable tests and static rules of thumb to empower decision makers with data-driven approaches. Once all of their data is accessible and AI begins uncovering important insights, manufacturers can overcome current challenges, identify emerging problems to nip them in the bud, and, ultimately, improve the bottom line.
Prateek Joshi is the founder and CEO of Plutoshift.