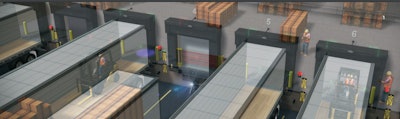
HAZARD RECOGNITION AND CONTROL
A Systematic Approach to Identifying and Reducing Loading Dock Hazards
September 2017
WHITE
PAPER
of $48,000 per single work-related injury and
$1,390,000 per death. That’s more than $1.8 billion
spent on forklift related injuries and deaths on an
annual basis.
Unfortunately, tragic stories and statistics like
these are far too common. However, they are often
preventable with the right training, processes and
systems in place. The first step to protecting workers
is identifying potential hazards that exist in and
around your loading dock. That starts by addressing
pedestrian safety.
PEDESTRIAN & FORKLIFT SAFETY
Do you have people on the drive approach as semi-
trailers enter and exit the loading dock area? The
lack of visibility by drivers, combined with ambient
noise masking the sound of trucks backing up, can
If you’re a facilities manager or work on a loading
dock, you understand that danger lurks around
every corner – inside and outside the building.
Whether it’s trucks entering the drive approach, or
material handlers loading and unloading trailers,
a busy loading dock poses a number of threats to
workers.
The danger of serious injury or death to loading
dock personnel is a sobering reality for companies
today. Recent news reports like these below serve
as a tragic reminder of what’s at stake.
THE ASSOCIATED PRESS – JANUARY 24, 2017
Authorities in Las Vegas say the death of a 44-year-
old man who was fatally injured when he was
struck by a tractor-trailer in a grocery store loading
dock was an accident. The Clark County coroner
reported Tuesday that the man died of multiple
injuries before his body was found.
THE ASSOCIATED PRESS – JANUARY 25, 2017
A 51-year-old man was killed when he fell between
a loading dock and a tractor trailer as the vehicle
pulled away from the dock and a forklift then
fell on him, law enforcement officials told the
Associated Press.
Statistics from organizations like the Occupational
Safety and Health Administration (OSHA) and the
Industrial Truck Association also paint a picture
of the dangers lurking at the dock. According to
a recent study, forklift accidents result in 34,900
serious injuries every year and close to 100 fatalities.
Furthermore, The National Safety Council reports
that forklift accidents cost employers an average
1
result in pedestrians being pinned or crushed on
the approach. Pedestrian hazards also exist inside
your building. Many of these accidents occur
when dockworkers are in the path of a forklift
that is entering or exiting a trailer. According to
the National Institute for Occupational Safety and
Health (NIOSH), close to 20 percent of all forklift
accidents involve a pedestrian being struck by the
forklift. That translates to almost 19,000 people per
year.
There are a wide variety of factors contributing
to pedestrian hazards, including: noise, limited
visibility, heavy equipment, operator error, lack of
communication and a push for productivity. The
best way to mitigate these factors is to implement
a multi-layered protection system. Using advanced
technology to continuously monitor the inside and
outside of the loading dock while providing visual
and audible alarms to warn of potential danger is
key. Rite-Hite has been partnering with companies
for years to identify potential hazards and develop
solutions that protect workers, equipment and the
bottom-line.
RITE-VU™ HAZARD RECOGNITION
AND CONTROL
The Rite-Vu Hazard Recognition and Control system
is the direct result of Rite-Hite’s collaboration with
customers and industry professionals. The system
is designed to help protect workers on and off
forklifts, inside and outside the loading dock area.
It takes a systematic approach to loading dock
safety, protecting workers in several important ways.
Approach-Vu™ – Safety begins on the drive approach
when a truck driver is backing up into a loading dock
bay. Approach-Vu uses motion sensors mounted
above the loading dock shelter to continuously
monitor for trucks. When a truck is detected, an
audible warning sounds and a bright light illuminates
in a pedestrian’s line of site. The combination of
audible and visual warning helps reduce the risk
of pedestrians being struck on the drive approach.
Pedestrian-Vu™ – When a material handler is working
inside a trailer, it is critical for pedestrians and
other material handling equipment to stay clear
of the door opening. Pedestrian-Vu uses motion
sensor technology to alert dockworkers of activity
inside a trailer, helping to keep them out of harm’s
way. Sensors are placed on each side of the dock
door and detect when a pedestrian or material
handling equipment enters the trailer. When this
happens, a bright blue light is projected on to the
leveler signaling that there is activity inside the
trailer and warning people to stay clear. If the trailer
is secured using a Dok-Lok® vehicle restraint, it
cannot be disengaged while someone is detected
inside the trailer. Furthermore, if someone enters
an unsecure trailer, an audible alarm is prompted.
2
3
Corner-Vu™ – With the Corner-Vu system, loading dock
personnel will no longer have to guess whether or not
a trailer is secured at the loading dock. Bright lights
mounted on the inside top corners of the loading
dock door indicate whether or not a trailer is properly
secured. Green lights mean a trailer is safely secured
and ready to enter, while red lights caution workers to
stay clear. Visual status is also displayed on the Dok-
Commander control system (lights and video display).
Leveler-Vu™ – This system provides material
handling operators with a visual reference as they
back out of a trailer. Green lights indicate that the
trailer is properly secured to the loading dock, while
red lights caution to stay clear. The high-intensity
lights are mounted to the dock leveler making
them easy to see when entering or exiting a trailer.
The Rite-Vu™ Hazard Recognition and Control system
is controlled by Rite-Hite’s Dok-Commander™ control
system. The Dok-Commander offers a number of
advantages over traditional controls, including:
Control Integration – Dok-Commander has the ability
to integrate a wide variety of controls into a single
unit. This helps to simplify operation while freeing up
wall space.
Interlocking Equipment – Dok-Commander has the
ability to interlock systems, creating a customized
sequence of operation that increases overall
safety and productivity. For example, a sequence
could be implemented that restricts a trailer
from being released from an automatic vehicle
restraint until a loading dock barrier is put in place.
Visual Communication – A visual display of
the loading dock approach is integrated into
the Dok-Commander control box, giving
users a live look at trailers entering the area
and vehicle restraint status. There is no need
for a worker to go outside to confirm status.
NEMA 4X Rated – Protection for the
components that help protect your people
in the harsh loading dock environment.
Security System Interface – A Dok-Lok® and Dok-
Commander pairing can physically enhance
security at a facility when linked with an active
building security system. If an engaged restraint
is tampered with, the building security system
is notified and facility protocol is followed.
Full-time safety at the loading dock often includes
a removable barrier to guard the loading dock
opening when a truck is not present. The Dok-
Guardian™ Safety Barrier from Rite-Hite® is
designed to stop up to 10,000-pounds traveling
at up to 4 miles-per-hour. It provides a four-
foot high visual barrier that stretches across the
door opening and can be easily seen by workers.
The Dok-Guardian can be interlocked with a Rite-
Hite vehicle restraint, creating a sequence of
operation that prohibits the barrier from being
removed until a vehicle restraint is fully engaged.
TOTAL LOADING DOCK SAFETY
Trailer separation accidents are another serious
threat to loading dock personnel. Separation
accidents are often the result of a communication
breakdown, or the use of antiquated
technology to secure trailers (i.e. wheel chocks).
4
An automatic vehicle restraint is the first layer of
defense against trailer separation accidents and has
long been synonymous with loading dock safety.
While vehicle restraints can’t be overlooked when
discussing total dock safety, modern technology
has given birth to integrated systems that take
safety to a whole new level.
To draw a simple comparison, look at the automobile
industry. For decades, the seat belt was the gold
standard for safety. Now modern automobiles are
packed with safety enhancements, including air
bags, automatic emergency braking, pedestrian
detection, blind-spot assist, lane-departure warning
and more. All of these systems working together
have made automobiles safer.
Companies like Rite-Hite® are adopting similar
technologies and are introducing them to industrial
settings. These technological advancements,
combined with the use of automatic vehicle
restraints, are helping to elevate safety and
productivity at the loading dock and beyond.
TAKE CONTROL WITH A SYSTEMATIC
APPROACH
Today’s loading dock environments are busier,
faster and more complicated than ever before.
As a result, companies need to mitigate potential
threats by using the most advanced systems and
technologies. A systematic, multi-layered approach
integrating motion sensors, visual/audible alarms,
automated vehicle restraints and barriers is the
most effective way to reduce risk at the loading
dock.
To learn more about Rite-Hite’s systematic approach
to loading dock safety, visit ritehite.com or call
(800) 456-0600 to schedule a free loading dock
assessment. The experts at Rite-Hite will help you
identify potential hazards at the loading dock and
will develop a customized solution to help protect
your workers.