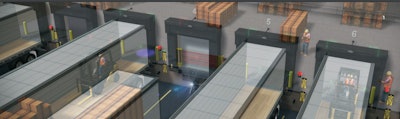
FOOD SAFETY:
From Farm to Fork, why the Loading Dock Plays an Important Role in
Securing America’s Food Supply.
June 2014
WHITE
PAPERFOOD & BEVERAGE • CONCEPT TO DELIVERY • PRESENT TO FUTURE • SPECIAL REPORTNOV. 1, 2013AS SEEN IN:
RiteHite.com
roughly one in six Americans (or 48 million people) get sick,
128,000 are hospitalized and 3,000 die of food borne
disease.1 By the time food becomes contaminated, it has
often been mishandled in several ways along the food
production chain. According to the CDC, loading docks are
an area of concern, particularly when refrigerated food is
left on a loading dock for long periods of time during warm
weather.
When it comes to the loading dock, a common breakdown
in the cold chain occurs when the security seal is broken
on trailer doors outside the building and the doors are
opened in the drive approach, exposing product to outside
elements. If the security seal is broken by the driver, or
some other party, companies have no way of knowing
if the contents have been tampered with potentially
creating a number of security issues. In addition, product
may be exposed to warm weather outside the building,
which allows bacteria to grow. Temperature and humidity
control also become important once product is unloaded
in a facility. Any gaps found at the loading dock make it
diffi cult to control environmental conditions. A company’s
inability to control temperature and humidity can lead to
spoiled or damaged goods.
The law gives the Food and Drug Administration (FDA) new
authority to regulate the way foods are grown, harvested
and processed, allowing the agency to focus more on
preventing food safety problems rather than reacting to
problems after they occur.
Portions of the act went into effect once it was signed into
law by President Obama, such as the FDA’s authority to
order food recalls. Other portions of the law require the FDA
to prepare and issue regulations and guidance documents
over time covering a variety of areas, including: harvesting,
storage, processing, packaging, distribution, sales and
consumption.
Many safety-minded companies involved in the food supply
chain are taking proactive measures to comply with FSMA
and any future regulations. These proactive measures are
helping secure America’s food supply, which ensures safe,
reliable food is served at restaurants and kitchen tables
across America. In addition, companies are protecting
themselves from the damaging and lasting impact of a
major product recall.
THE LOADING DOCK
There are a wide variety of businesses involved in bringing
food to the marketplace. When you break down the food
supply chain process, it’s easy to see that a large portion
of America’s food is delivered and shipped through
loading docks at every level of manufacturing, processing
and distribution. Loading docks play a signifi cant role in
bringing fresh, safe food to American consumers. However,
there are a host of potential threats at the loading
dock that businesses need to address. Some include:
Cold Chain Integrity – When fresh or frozen foods are
being transported, the procedures and equipment needed
to maintain the integrity of the cold chain are critical. Any
breakdown in the cold chain can adversely affect the
quality and freshness of food and, in some cases, lead
to serious food contamination. The Centers for Disease
Control and Prevention (CDC) estimates that each year
1
1 in 6 Americans (or 48 million people) get sick,
128,000 are hospitalized and 3,000 die
of food borne disease.
IN JANUARY 2011, PRESIDENT BARAK OBAMA SIGNED INTO LAW THE
FOOD SAFETY MODERNIZATION ACT (FSMA), WHICH IS DESIGNED
TO ENHANCE THE SECURITY OF AMERICA'S FOOD SUPPLY CHAIN.
RiteHite.com
Contamination – An unsecured or poorly designed loading
dock position creates a gaping hole in a building. These
holes or gaps in coverage create entry points for unwanted
pests, including rodents, insects and other creatures. In
addition, visible daylight at the dock (sometimes referred
to as “white space”) indicates gaps that can allow dust,
snow and other contaminants into a building. For obvious
reasons, this is a major concern when it comes to supply
chain integrity. Organizations like the American Institute
of Baking International (AIB) have strict standards when
it comes to inspections at food manufacturing facilities
and distribution centers. According to its Consolidated
Standards for Inspection guide, all external doors, windows
or other openings must be close-fitting or otherwise pest-
proofed to less than ¼-inch or 6 mm.2
Cargo Theft – Inbound Logistics magazine reports an
estimated $30 billion in cargo is stolen each year in the
U.S. and the most highly sought after shipments are
pharmaceuticals, consumer electronics, apparel and
food.3 Despite serious efforts by the industry to combat
cargo theft, the numbers are still on the rise. From June to
August of this year, FreightWatch reported 202 thefts in the
U.S., with an average loss of $166,454. Thefts increased
by 5 percent, while the average dollar loss increased by
9 percent. Of the thefts reported, food and drink were
the most commonly targeted. Unsecured trailers at busy
loading docks are a prime target for cargo thieves, as well
as dropped trailers and those left unattended by drivers.4
2
Terrorist Threats – According to the Federal Bureau of
Investigation (FBI), terrorists consider America’s agriculture
and food production tempting targets. America’s food
supply is among the most vulnerable and least protected
of all potential targets of attack.5 Loading docks with
unsecured trailers are susceptible to theft. Furthermore,
a common practice that puts companies at risk is when
the security seal on a trailer is broken, or put in place by
non-company personnel on the drive approach. Security or
surveillance may not be as present on the drive approach,
which means food could be easily stolen, poisoned and
used as a terrorist weapon.
RiteHite.com
AUTOMATIC VEHICLE RESTRAINT
An automatic vehicle restraint can help prevent theft,
reduce contamination and improve the safety of dock
workers. An automatic restraint – like the Dok-Lok® from
Rite-Hite – wraps around a trailer’s rear-impact guard
(RIG), securing the trailer to the loading dock. This helps to
reduce trailer separation accidents and serves as a theft
deterrent. In addition to improving safety and reducing
damage to equipment, a tight connection reduces white
space where dirt, debris, insects and other environmental
contaminants can enter a building.
The installation of an automatic vehicle restraint is just
the fi rst step to improving loading dock security and
safety. Some automatic restraints like the Dok-Lok can be
integrated into building management or security systems,
providing another level of security and protection. The Dok-
Lok from Rite-Hite is considered the industry standard for
securing trailers at the loading dock because it offers the
most substantial wrap on RIGs and the widest vertical
engagement range (9-30 inches). Some models can even
help secure overseas or intermodal containers, which are
increasingly more common at the loading dock.
IT’S IMPORTANT FOR EVERYONE INVOLVED IN THE FOOD SUPPLY CHAIN TO ADDRESS THESE COMMON ISSUES FOUND AT
THE LOADING DOCK. TO DO SO, COMPANIES NEED TO CONDUCT A THOROUGH EXAMINATION OF THEIR LOADING DOCK
ENVIRONMENT – INSIDE AND OUT. IT STARTS BY ANSWERING SOME OF THESE IMPORTANT QUESTIONS:
3
• WHAT TYPE OF TRAILERS ARE BEING RECEIVED
AT YOUR LOADING DOCK?
• ARE THE TRAILERS BEING PROPERLY SECURED
TO THE LOADING DOCK?
• WHERE ARE THE TRAILER SECURITY SEALS
BEING CUT AND PLACED?
• DO YOU SEE GAPS OF DAYLIGHT AROUND YOUR
SEALS, SHELTERS AND LOADING DOCK DOORS?
• ARE PRODUCTS BEING DAMAGED OR CONTAMINATED
DURING THE LOADING AND UNLOADING PROCESS?
• ARE YOU MAINTAINING PROPER ENVIRONMENTAL
CONDITIONS BY SEALING ALL FOUR SIDES OF THE
TRAILER AT LOADING DOCK OPENINGS?
• ARE YOUR LOADING DOCK PITS BEING PROPERLY
WASHED DOWN AND SANITIZED?
IN ADDITION TO ADDRESSING THESE SERIOUS QUESTIONS, IT’S IMPORTANT FOR BUSINESSES TO BRING IN A LOADING DOCK
CONSULTANT WHO CAN ANALYZE SPECIFIC APPLICATIONS AND PROVIDE PROPER SOLUTIONS. A LOADING DOCK PROFESSIONAL
WILL TYPICALLY RECOMMEND A SYSTEM OF PRODUCTS THAT WORK TOGETHER TO ENHANCE THE OVERALL SECURITY, SAFETY
AND FUNCTIONALITY OF A LOADING DOCK.
5
RiteHite.com
VERTICAL DOCK LEVELER
Once a trailer is secured at the loading dock, the next step
is bridging the gap between the loading dock fl oor and the
trailer bed. A vertical-storing dock leveler is considered the
standard for maintaining cold chain integrity, environmental
control and security. Unlike a pit-style leveler, a vertical
leveler (when in the stored position) allows the loading
dock door to close directly on the pit fl oor – rather than
the leveler itself – reducing energy loss by minimizing
outside air infi ltration. This also helps to protect the dock
door from damage. In dry or cold storage applications, this
tight seal helps reduce dust, debris, rodents and other
contaminants from entering a building. It also reduces
energy loss by controlling the exchange of air. A vertical
dock leveler also improves security by minimizing points
of entry at the loading dock. And fi nally, the vertical design
makes it easy to clean or wash down the pit fl oor when the
leveler is in the upright and stored position.
There are a variety of companies that offer vertical dock
levelers; however, there are some important features to
consider. First, look for a “drive through” application that
allows dock workers to open trailer doors inside the facility.
Opening and closing trailer doors inside a loading dock,
rather than on the drive approach, helps to ensure cold
chain integrity by minimizing outside air exchange into
a cold environment. Equally as important, loading dock
workers are placing or removing the seal from inside the
building. This reduces the chance of theft or tampering.
Also, it’s important to look for a vertical leveler that
provides the smoothest path between the facility fl oor and
the trailer. This helps reduce “dock shock” or whole-body
vibration to forklift operators, as well as damage to product
and equipment. For example, Rite-Hite dock levelers with
Smooth Transition technology reduce dock shock by up
to 76 percent when compared to standard levelers. The
Smooth Transition design uses a constant-radius rear
hinge that reduces the bumps and gaps at the rear of the
dock leveler. A two-point crown control and optimized lip
chamfer at the front of the leveler reduce the speed bump
effect normally felt by forklift drivers as they enter and exit
the trailer.
6
RiteHite.com
1 "Estimates of Foodborne Illness in the United States." www.CDC.gov. Centers for Disease Control. Web. 2013. .
2 AIB International. Consolidated Standards for Inspection. 31 Dec 2012. Web. .
3 Palmer, Jared. "The Cargo Theft Threat." Inbound Logistics. Jan 2010. Web. .
4 SCDigest Editorial Staff. "Logistics News: Unsafe Transportation World, as US Cargo Thefts Continue On." SCDigest.com. 25 Sep 2013. Web. 9 Oct. 2013.
.
5 Olson, Dean. United States. The Federal Bureau of Investigation. FBI Law Enforcement Bulletin. 2012. Web.
.
The information provided herein is provided as a general reference regarding the use of the applicable products in a speci c application. This information is provided without warranty.
It is your responsibility to ensure that you are using all mentioned products properly in your speci c application and in accordance with all laws and regulations.
• Drive approach
• Loading dock dimensions
• Loading dock door confi guration
• Building construction (Brick, metal, etc.)
• Weather conditions (Extreme heat, snow, etc.)
• Types of trailers (Semi-trailer with rear-impact
guard, intermodal containers, etc.)
• Weight and type of materials being loaded/
unloaded
• Security and safety risks
• Environmental conditions inside the facility
A RITE-HITE REPRESENTATIVE WILL CONDUCT
AN ON-SITE VISIT TO ANALYZE ALL ASPECTS OF
A LOADING DOCK ENVIRONMENT, INCLUDING:
SEALS AND SHELTERS
A dock seal or shelter creates an environmental barrier
between the back end of the semi-trailer and the inside of
the loading dock. This connection helps companies control
their environment by keeping wind, rain, dust, bugs and
other contaminants outside the building, while preventing
the escape of valuable energy from inside the building. An
effective dock sealing system also helps prevent weather-
related product damage and contamination, protecting
and securing the integrity of products as they move in
and out of a facility during manufacturing, processing and
shipping. Seals and shelters can also provide deterrence
against theft at the loading dock by sealing gaps that could
otherwise be passageways for thieves to move product.
For maximum protection, it is important to equip all
dock door openings with a system that closes the gaps
that are created when a trailer is backed in for loading
or unloading. This includes securing the tops, sides and
bottoms of the openings when the trailer is in place. Foam
compression dock seals, or full-access dock shelters that
seal trailer door hinge gaps, together with a full-coverage,
under-leveler sealing system, are recommended in most
applications. Further attention is often needed at the top
and corners of the trailer where frequent gaps remain. A
weighted header seal with corner-sealing ability provides
the best means to securely seal these areas.
Virtually all category-leading seal and shelter designs on
the market today originated at Rite-Hite, as part of the
original Frommelt line of environmental enclosures. Today,
only Rite-Hite's product line includes solutions that allow
effective sealing on all four sides. Rite-Hite dock sealing
products are distinguished by such benefi ts as guaranteed
protection against burning from the heat of trailer marker
lights; the exclusive use of state-of-the art materials to
provide the longest wear; and proprietary custom-design to
match the specifi c, unique needs of individual customers.
Popular products to look for include: Insulator Dock Seals,
GapMaster Shelters, PitMaster Under-Leveler Seals and
RainGuard Trailer Top Seals.
CONCLUSION
In most instances, a systematic approach that incorporates
automatic vehicle restraints, vertical dock levelers,
appropriate seals/shelters and the proper sequence of
operation is the best way to secure a loading dock. These
products – working together as a system – enhance
security, protect employees, reduce contamination and
improve environmental conditions within a building and
throughout a given supply chain.
To create a safer, more secure loading dock environment,
companies are encouraged to visit RiteHite.com, or call
888-841-4283 to schedule an assessment with a loading
dock professional.