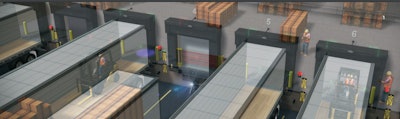
A SYSTEMATIC APPROACH TO
LOADING DOCK SAFETY
1-888-841-4283 RiteHite.com
WALTER SWIETLIK
RITE-HITE CORPORATION
Loading docks are a busy and sometimes dangerous place. In
most loading dock environments, you have semi-trucks pulling
in and out of the approach, material handlers buzzing about
and employees working around the dock. All of this activity can
lead to accidents without the proper systems and procedures
in place.
According to the Department of Labor and the Occupational
Safety and Health Administration (OSHA), approximately
100 workers are killed and 95,000 injured every year while
operating forklifts. Many of these accidents are related to
turnovers or when a forklift operator drives off the dock.
In addition, the health of forklift operators is at risk due to
repetitive vibration exposure called “Dock Shock.”
Some of the more common accidents and health risks at the
loading dock include:
EARLY DEPARTURE - A truck driver unexpectedly drives
away from the loading dock while a forklift operator is entering,
leaving or still inside the trailer.
LANDING GEAR COLLAPSE - The landing gear on a trailer
gives way causing the trailer to pitch forward or fall to the side.
TRAILER POP-UP - A loaded forklift entering the rear of the
trailer causes it to move forward and drop, causing the nose of
the trailer to suddenly rise.
TRAILER UPENDING - The weight of the forklift sends the
trailer’s nose down, causing the rear end to move up and away
from the building.
TRAILER CREEP - Repeated impact from the lift truck
causes the trailer to edge away from the dock, which can result
in the lift truck falling to the ground.
DOCK SHOCK - Long-term, repetitive vibration exposure to
forklift operators as they enter and exit trailer beds
Greater safety and efficiency at the loading dock can be
achieved when companies incorporate a system of products
and a detailed sequence of operations to create “full-time”
safety at the dock. The use of barrier systems, automated
vehicle restraints, levelers and lighted communication systems
– working together – can help reduce the risk of accidents and
injuries to workers.
For many companies, a loading dock safety strategy may
encompass one or all of the following elements:
INTERLOCKING SYSTEMS - An interlocking system prevents
the operation of equipment until certain conditions are met.
For example, an automatic vehicle restraint would not release
a trailer until a loading dock barrier is put in place. Interlocking
systems are focused on the safety and security of workers.
INTERCONNECTING SYSTEMS - An interconnecting system
allows a piece of equipment to operate only when another piece
of equipment is activated first. An example is when a button
is pushed to activate a dock leveler, then a vehicle restraint
engages. Interconnecting systems are focused on safety as well
as enhanced efficiency.
To determine which system is most ideal for your loading dock
application, you must first address some important questions:
What types of trailers are coming to your loading dock? What
is the process for securing these trailers to ensure the safety
of material handlers? What type of communication system
is being used to alert drivers and workers of vehicle restraint
status? When a truck departs, how is the loading dock opening
secured?
Companies like Rite-Hite (www.Rite-Hite.com) can help you
address these questions and provide recommendations
on what products, systems and procedures will work best
for your environment. The process starts by breaking down
your sequence of operations to fully understand your risks,
while identifying process improvements. The end result is a
customized solution to meet a specific application.
In a typical loading dock environment, the process starts when
a truck driver is backing up in the approach. Communication
is key at this point. The truck driver should see a green light
indicating that it’s clear to back into the loading dock bay.
Conversely, loading dock workers and material handlers should
see a red light inside the facility alerting them that it’s unsafe
to enter the trailer. Additional communication/safety options
include a barrier system covering the loading dock door until
the truck is secured at the dock. Once the trailer has backed
into the dock and is secured using a vehicle restraint, the lights
inside the building change to green letting workers know that
it’s safe to remove the barrier and enter the trailer.
The information provided herein is provided as a general reference regarding the use of the applicable products in a specific application. This information is provided without warranty.
It is your responsibility to ensure that you are using all mentioned products properly in your specific application and in accordance with all laws and regulations.
1-888-841-4283 RiteHite.com
DOK-LOK® VEHICLE RESTRAINTS
Outside, a red light tells the driver not to pull away. The process
follows a similar pattern when a trailer leaves the loading dock.
Rite-Hite is recognized globally as one of the true innovators
in loading dock safety and productivity. The company offers
a variety of solutions to address many of the issues that
companies face at the loading dock and beyond. The following
products work together to create a safer, more production and
more profitable work environment.
The Dok-Lok from Rite-Hite is considered the industry
standard for securing trailers at the loading dock because
it offers the most substantial wrap on rear-impact guards
and the widest vertical engagement range (9-30 inches).
Some models can even help secure overseas or intermodal
containers, which are increasingly more common at the
loading dock. In addition to the Dok-Lok, Rite-Hite offers
wheel-based restraints for lift-gate trailers or trailers with
damaged (or missing) rear-impact guards.
Traditional vehicle restraint systems use a red or green
light on the control box and outside the building to indicate
restraint status. This is an important safety feature, but it
has limitations. For example, what if the control box inside
the building is not in the line of site of the forklift operator?
What if the forklift load is obstructing the control box? What
if the control box is covered by pallets? Fully-integrated
communication systems that provide instant, status-at-a-
glance feedback provide the safest solution.
For example, Rite Hite offers the Rite-Vu™ Light
Communication System, which provides clear, constant
communication of restraint status to the forklift operator
when entering and exiting the trailer. In addition to lights on
the control box, the system features Corner-Vu lights that are
located in the upper corners of the interior dock door. These
lights provide a highly-visible status report as the forklift
driver enters the trailer. There is also Leveler-Vu lights that are
mounted on the dock leveler to confirm restraint status as the
forklift driver backs out of the trailer. With the Rite-Vu system,
everyone is on the same page, including the truck driver,
loading dock personnel and material handlers.
RITE-VU™ LIGHT
COMMUNICATION SYSTEM
The information provided herein is provided as a general reference regarding the use of the applicable products in a specific application. This information is provided without warranty.
It is your responsibility to ensure that you are using all mentioned products properly in your specific application and in accordance with all laws and regulations.
1-888-841-4283 RiteHite.com
DOK-GUARDIAN™
SUMMARY
Full-time security at the loading dock often includes a
removable barrier to guard the loading dock opening when
a truck is not present. The Dok-Guardian Safety Barrier from
Rite-Hite is designed to stop up to 10,000-pounds traveling
at up to 4 miles-per-hour. It provides a four-foot high visual
barrier that stretches across the door opening and can be
easily seen by workers. The Dok-Guardian can be interlocked
with a Rite-Hite vehicle restraint, creating a sequence of
operation that prohibits the barrier from being removed until
a vehicle restraint is fully engaged.
Finally, it’s important to look for a dock leveler that provides
the smoothest path between the facility floor and the trailer.
This helps reduce “Dock Shock” or whole-body vibration to
forklift operators, as well as damage to product and equipment.
For example, Rite-Hite dock levelers with Smooth Transition
technology reduce vibration by up to 76 percent when
compared to standard levelers. The Smooth Transition design
uses a constant-radius rear hinge that reduces the bumps and
gaps at the rear of the dock leveler. A two-point crown control
and optimized lip chamfer at the front of the leveler reduce the
speed bump effect normally felt by forklift drivers as they enter
and exit the trailer.
In most instances, a systematic approach that incorporates vehicle restraints, barrier systems, advanced communication
systems and the proper sequence of operation is the best way to secure a loading dock. These products – working together as
a system – enhance the safety and security of workers, while minimizing product damage and downtime.
To create a safer, more secure loading dock environment, companies are encouraged to visit RiteHite.com, or call 888-841-4283
to schedule an assessment with a loading dock professional. A Rite-Hite representative will conduct an on-site visit to analyze all
aspects of a loading dock environment, including:
LOADING DOCK LEVELERS
• DRIVE APPROACH
• LOADING DOCK DIMENSIONS
• LOADING DOCK DOOR CONFIGURATION
• BUILDING CONSTRUCTION
(BRICK, METAL, ETC.)
• WEATHER CONDITIONS
(EXTREME HEAT, SNOW, ETC.)
• TYPES OF TRAILERS
( SEMI-TRAILER WITH REAR-IMPACT GUARD,
INTERMODAL CONTAINERS, ETC.)
• WEIGHT AND TYPE OF MATERIALS BEING LOADED/UNLOADED
• SECURITY AND SAFETY RISKS
• ENVIRONMENTAL CONDITIONS INSIDE THE FACILITY