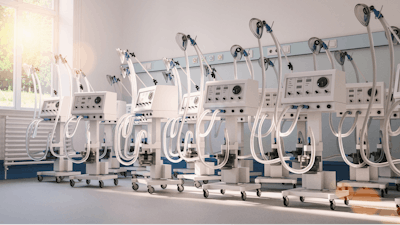
The COVID-19 outbreak has disrupted supply chains on a massive scale, with manufacturers everywhere contending with the pandemic’s impact on supply and operations. While manufacturers continue to work to deliver goods and services quickly and safely to those at risk of infection and those working on the frontlines of the medical response, supply shortages have required quality teams to work with production shortages and manage the changes properly.
As manufacturers focus on accelerating production of various products needed to combat the health crisis, supplier quality shouldn’t let up.
For medical device manufacturers, where precision in lifesaving products is vital, the slightest drop in a supplier’s quality performance can result in nonconforming materials, out-of-spec products, production downtime and product recalls. To anticipate supplier quality issues before problems spread, manufacturers should always be vigilant of warning signs that a supplier’s quality is failing.
Supplier Quality Warning Signs
Without understanding the quality and reliability of their suppliers, manufacturers risk not knowing if a supplier’s quality system is failing. When it comes to recognizing early problems with a supplier’s quality, there are some telltale signs, including quality degradation, late deliveries and slow communication. The following are what some of these warning signs may look like:
- Shipments with rising scrap rates or failing parts per lot. A pattern of delivering nonconforming materials, components or parts should sound an alarm.
- Delays in shipments. A pattern of missing ship dates can often indicate that a failing manufacturing process is affecting the supplier’s quality.
- Decline in response time from a normally responsive supplier. Becoming unresponsive or slow to respond to inquiries about quality issues may mean the supplier is avoiding you.
According to LNS Research, manufacturers with poor visibility into supplier performance have a median supplier defect rate more than double the remainder of the population. Recognizing the signs of failing quality before they spread relies on visibility into a supplier’s processes.
To gain greater visibility into supplier quality, it is critical that manufacturers work with their supply chain partners, communicating and collaborating to ensure the highest level of quality – during a global pandemic or otherwise.
Visibility Through Communication & Collaboration
Manufacturer-supplier relationships should always be built on communication and collaboration, but the added urgency during a massive health crisis means manufacturers must work more closely with their supplier partners to improve visibility and resolve any quality challenges. If quality problems are recurring and the supplier fails to identify, correct and communicate the issue to the customer, then lifesaving product deliveries are delayed or user safety is threatened.
If there are issues hindering optimal supplier quality performance, the manufacturer and supplier should together determine corrective actions for the supplier to implement within a specific time frame and deliver quick changes to the product and needs. This can only happen with open, honest communication between the manufacturer and supplier.
Establishing direct, two-way communication includes identifying responsibilities and defining expectations for each party, developing and documenting the criteria for supplier performance and identifying major quality problems and corrective actions. This should help hold both parties accountable, quicken response times and streamline the entire sourcing process. The supplier scorecard is a useful tool in this regard, as it sets up a structured measurement or cadence of collaboration.
To help a supplier reach a better state of quality, there needs to be a robust and well-managed process that relies less on mandating specific solutions and more on establishing active, ongoing collaboration. A collaborative manufacturer-supplier partnership is especially important during urgent, large-scale supply chain disruption. Actively including suppliers in the quality process can be a great motivator.
By asking suppliers for their input, questions and goals on a continuous basis, manufacturers are more likely to improve visibility into supplier quality, enable better processes and ensure higher-quality materials or parts. For manufacturers, this kind of active, ongoing collaboration has the dual benefit of improving their own efficiency and lowering their own costs.
Greater communication and collaboration improve visibility into a supplier’s current state of quality. This allows the partnership to resolve persistent quality challenges across the extended supply chain and improve business for both parties.
Real-Time, End-to-End Monitoring Needed
In the current climate of COVID-19, real-time visibility is necessary to run a successful supply chain where lifesaving products continue to be delivered to patients and the workers treating them on the front lines. However, the same climate also makes real-time visibility into what is happening a key challenge among manufacturers of all kinds everywhere.
Communication and collaboration with suppliers are critical to ensuring high-quality materials and parts. Real-time, end-to-end supply chain monitoring is also essential for gaining the intelligence that will help minimize the impact of disruptions on quality processes and quickly bring lifesaving products to market.
Terrance Holbrook is director of product at MasterControl, a provider of cloud-based quality and compliance software for life sciences industries.