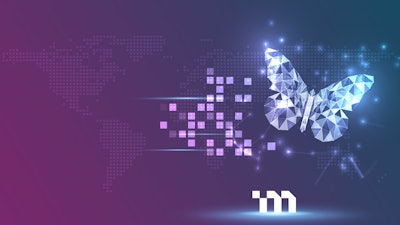
In recent years, investments in core information technologies have accelerated and expanded across manufacturing sectors. As new digital technologies make it possible to gather and analyze greater amounts of data across machines and functions, manufacturers can be faster, more flexible and more efficient in producing higher-quality products.
Of course, digital transformation requires more than just purchasing and implementing software or hardware. For life sciences manufacturers, digital transformation means numerous workflow processes must be reviewed, multiple sites and siloed departments must be incorporated, legacy equipment and paper-based systems must be integrated or replaced, and other existing data sources must be consolidated. There are also scalability, security, regulatory and usability factors to consider.
It can be a massive, time-consuming undertaking. Where do you even start? Digitizing an organization’s existing systems and processes requires both a realistic short-term strategy and a patient long-term commitment. Below are a few best practices to consider when starting a digital transformation journey.
#1: Start Small and Smart
Manufacturing business technology runs on ongoing, disruptive change. As we navigate Industry 4.0 with industry-wide talk of a fifth industrial revolution forthcoming, it’s easy to get lost in the scope and speed of change. The first step forward is to focus on identifying specific areas of improvement and piloting small, smart technological changes that make an impact in those areas.
A full digitization implementation may rightfully seem overwhelming. Instead, digital transformation can be initiated through a “small automation” approach. Rather than doing too much too fast, organizations can focus on quickly implementing flexible and adaptable technologies that fill the gaps left by current enterprise systems. This “small automation” approach is easier to roll out and control, and it is much less costly than large-scale IT initiatives. It is also more flexible than big automation, with the technologies enabling small automation being relatively to easier to configure.
Ultimately, taking a smaller, smarter approach to replacing paper-based and hybrid systems means companies can quickly improve process performance, increase employee productivity and realize significant cost savings – all while minimizing disruption to operations and being agile to pivot when needed.
#2: Prioritize Interconnectivity
Today, disconnected systems and operations, along with siloed information and communication, can lead to a lot of waste and, worse, a lot of mistakes. An incremental shift into a fully digital environment is a start in digital transformation. While taking gradual steps toward digitization, the long-term goal should be interconnectivity. To realize the far-reaching benefits of transformation, manufacturers must go beyond silos. There will need to be a wholesale shift in perspective for a holistic view of the data within a business.
The focus must be on connecting all workflows, data, systems and human insights throughout the organization. Manufacturers will need to automate the collection and analysis of data across several different areas – from R&D and manufacturing to supplier management and patient care – as well as a whole range of other sources – including sensors and wearables – to drive smarter, more agile operations.
Shifting to a more holistic view of data means manufacturers must digitally integrate people and systems across operations and functions, which can be done by capitalizing on platform dynamics. Digital platforms can streamline connections and information exchanges across ecosystems – connecting multiple data sources and gathering, sharing and analyzing data to create meaning from it. The result is more fluid cross-departmental collaboration, data management and shared insights that enable more competitive operations.
#3: Empower Workers
Transformation doesn’t come from technology. It comes from process improvements and greater decision-making enabled by collaborative technologies. And digital transformation doesn’t mean replacing people with machines. It means enhancing processes and freeing up people to leverage their experience and insight. The real benefits of digital transformation can only be achieved when it supports workers.
Manufacturing business technology is about optimizing people and processes to increase efficiencies, decreasing the chance of human error, and releasing workers from having to perform repetitive tasks so they can focus more on value-adding activities, which in turn leads the way to enhancing employee and business performance. With greater access to digitized data that is more accurate and complete, for example, personnel in both manufacturing operations and quality assurance can better understand how the shop floor is working and make more informed, data-driven decisions about production and quality.
Digital transformation is more than a shift in technology — it is a shift in mindset. It is an opportunity for manufacturing businesses to take a human-centric approach to smart factory technology and empower digitally connected workers to thrive within a data-driven manufacturing environment, where an organization’s people are empowered to make better decisions to drive business.
Final Thoughts
If an organization’s people are conditioned to operate in a highly risk-averse environment, they will continue to use the tools they are familiar with, whether traditional paper-based or hybrid solutions utilizing spreadsheets. Doing so means they are missing out on proven benefits of digitization, while increasing operational costs and increasing risk.
Change is hard because it’s disruptive, but digitization efforts don’t have to be completely disruptive. As with any new change in an organization’s technology or mindset, digital transformation efforts require that workers be engaged in the process throughout the implementation to ensure understanding and even trust in the technology and the data.