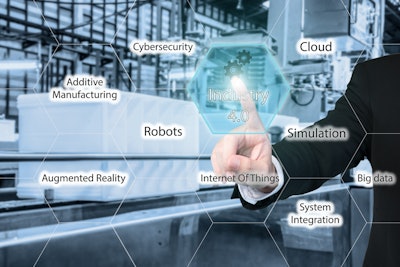
When you hear the words “automation” and “manufacturing” in the same sentence, you probably think of assembly lines staffed by armies of tireless robots. The association between innovation and job losses stems from an image of technology that replaces the need for humans in manufacturing. With Industry 4.0 on the ascent, it’s understandable that the manufacturing labor sector is anxious about being its human workforce being replaced by machines.
It only takes a quick glance at the data to dispel those worries. A 2015 study showed that, by 2025, the US will likely add 3.5 million manufacturing jobs. Up to two million of these positions will be in new or emerging fields – servicing web-connected devices, for example. This suggests that technologies like artificial intelligence, machine learning, ERP and other data-driven advancements will have a positive impact on those who work in manufacturing.
Some have predicted that the sky is falling. In reality, the tide is rising.
Living Proof: Robots Haven’t Increased Unemployment
Germany offers a portrait of what an increasingly-automated manufacturing sector could look like. Europe’s most powerful economy has installed manufacturing robots aggressively since the mid-1990s and enjoyed greater profits and profitability as a result. Automation has not had a negative impact on German manufacturing employment totals; in fact, workers with previous exposure to automation have found opportunities to move into higher-skilled and higher-paying jobs.
Data-driven technologies give the human workers of today and tomorrow the means to streamline their work activities and automate tedious tasks in order to focus on more difficult ones – which is likely to have a positive impact on wages and job prospects. Despite the preponderance of objective and anecdotal data, there is still widespread anxiety that digital transformation will decimate workforces. In reality, the opposite is significantly more likely.
Here are examples of how technology is improving the lives of manufacturing workers by making them more productive, more efficient and better poised for a successful career in this industry.
1. Making Sense of Data
In the era of connected devices, it’s possible for manufacturers to collect massive amounts of data. Technologies like ERP software integrate and organize this data on a single platform, eliminating the need for manual data entry from multiple sources. The time and effort you save on data entry can be redirected towards analyzing your data and gathering insights, something that requires a human understanding of the company and the industry. Let technology do the coordinating and calculating. Then let manufacturing managers decide what the numbers mean and how to act on them.
2. Keep Equipment Functioning
Industry 4.0 technology monitors machine performance, noting declines in output and recommending preemptive maintenance if and when necessary. This improves efficiency by allowing you to focus on the equipment that most needs attention, and reducing the likelihood of unexpected failures. It also eliminates the need for a human to manually inspect and monitor every single machine on the shop floor, but it doesn’t eliminate the need for a human expert altogether.
Once a problem is flagged, human technicians are called to service the machine, a dynamic and unpredictable process that will take machines decades to handle autonomously. The industry will need human workers to diagnose and expertly solve issues with devices connected to the Internet of Things, machines using artificial intelligence, and technologies used for additive manufacturing. This need opens more opportunities for those who possess skills in troubleshooting and repairing these advanced technologies.
Humans and technology work together to prevent machine failure while reducing the cost of maintenance.
3. Planning a Business Strategy
Humans can make guesses and assumptions. Machines can make predictive forecasts by analyzing the massive amounts of data in an ERP system. Those forecasts are remarkably informed and accurate, which is an incredible asset when deciding what to produce next, which market to move into, or how to adjust to upcoming changes in your supply chain.
Ultimately, only humans can make these strategic determinations because only they understand the company’s goals and the market conditions. Reducing the manual labor needed and the risk of human error in compiling the data by using technology for predictive analytics gives manufacturers more accurate information to guide their strategy. Smart decision-makers armed with the best information available tend to lead their companies in the right direction.
4. Handling the Heavy Lifting
Machines are great at lifting heavy loads and working non-stop for hours on end. They are not as good at navigating through complex spaces and performing sophisticated motor skills. In this context, machines can be used essentially as robotic beasts of burden. Workers don’t have to waste energy or risk injury through overly strenuous work or performing repetitive tasks for hours at a time. Still, while machines can be leveraged to handle tedious jobs, they shouldn’t be left to work unsupervised.
The guidance and oversight offered by human technicians, machinists, and software engineers ensure that the technology is in the right place and working on the right task. The manufacturing industry is in need of skilled human workers to program machines for specific production jobs, calibrate machines when processes are changed or adjusted, and troubleshoot devices that aren’t working correctly.
5. Organizing Logistics
Logistics is getting more complicated all the time with companies spending over $1 trillion on shipping in 2017. With Industry 4.0 advancements, intelligent systems can tackle the considerable task of organizing and arranging shipments. This eliminates the need for many low-level package handlers. However, at the same time, more shipping means a greater need for delivery drivers. Plus, logistics must be managed by humans to ensure that shipping does not go off the rails.
6. Leveraging Expertise and Experience
As baby boomers begin to retire, a flood of institutional knowledge is leaving manufacturers. Modern technologies like ERP systems allow companies to record much of this information – such as industry knowledge, customer history, equipment expertise, company processes, and more – and then pass it along to the next generation of employees. Technology can also aid in employee training and education, helping workers keep their skills up to par as Industry 4.0 evolves.
7. Facilitating Communication and Collaboration
Success is not guaranteed in Industry 4.0. New tools may be available, but when everyone has access to the tech, the competitive landscape starts to even out. The companies that will succeed are those that find ways to innovate and improve beyond what the competition can deliver. It’s ultimately up to humans to come up with the brilliant ideas, but thanks to data-sharing platforms and collaborative tools, it’s much easier for teams to think outside the box.
It’s clear that, at this point, technology will not – and frankly, cannot – replace the human element in manufacturing. Instead, it will replace repetition, fatigue, confusion, and inefficiency; which is something everyone in the industry can support. Instead of worrying about how technology subtracts from current job duties, it’s time for manufacturers to get excited about all that it will add.
Aaron Continelli, president of Cre8tive Technology and Design, started things small in 2005. What began as a one person consulting firm has now become a staff of 58 with three office locations. Specializing in ERP system sales and services, Cre8tive Technology and Design became an EPICOR Partner in 2007. Since then, Cre8tive Technology and Design has emerged as one of EPICOR’s ELITE and won the 2013 and 2015 Americas Partner of the Year as the Top Revenue Producer.