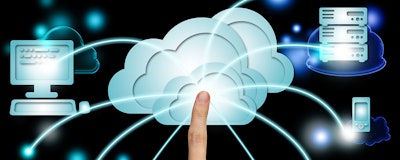
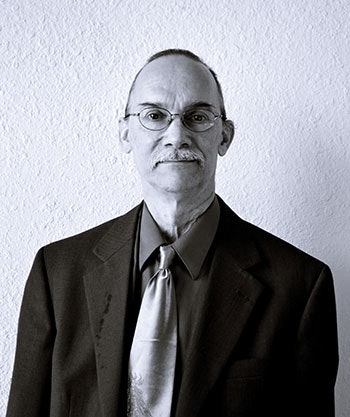
Manufacturing in the U.S. is undergoing a major disruption cycle. Basic manufacturing that requires fewer skills and less sophisticated equipment is moving relentlessly overseas, while domestic manufacturing is moving towards greater levels of automation and skills-based processes. The second phase of this inevitable trend is a move to the cloud, stepping away from the traditional model of costly, on-premise manufacturing software that must be managed on-site by highly skilled and highly paid engineers.
Among the top ten highest ranking MRP software offerings, only one lacks a cloud version. Larger players such as SAP, Oracle and Epicor, now have cloud versions of their flagship ERP systems, while smaller players and newcomers are starting right out of the gate with born-in-the-Cloud manufacturing software. These born-in-the-Cloud products are especially attractive to smaller or mid-size manufacturers, which may not have the internal IT resources or talent to run more sophisticated on-premise MRP or ERP systems — and the cloud versions are less expensive, easier to run and usually offer the same functionality as their more costly on-premise cousins.
But as more manufacturers move to the cloud, there is a critical element that is often missing — and that is the integration layer. “In addition to growing acceptance of the cloud among manufacturers, we’re seeing an increased focus on Internet of Things,” said Renat Zubairov, CEO of elastic.io, a leading innovator in as-a-service integration. “As a result, domestic manufacturers are seeing massive amounts of data coming from sensors, switches, and other devices from every corner of the shop floor, on through the extended supply chain. Manufacturers have not yet caught up to these realities, and often face an environment with multiple cloud apps and multiple data sources, each serving a single purpose, but lacking the integration needed for a truly enterprise view. Without the integration layer, manufacturers are not getting the full value of their cloud environments.”
Full Value From the Cloud
The first wave of cloud computing in manufacturing focused mainly on facilitating data access, and on solving individual, isolated problems. Today, cloud computing and SaaS in manufacturing facilitates real-time connectivity between machines and shop floor systems, greater visibility, and a better understanding of performance at a granular level. Today’s manufacturer measures its value not in the number of machines it possesses, but in the amount of data and knowledge it is able to collect and analyze.
“The large amount of data that is now available to manufacturers helps with better decision-making, more precise analytics and more accurate forecasting,” said Zubairov. “But that benefit only accrues if those many sources of information, and the apps that generate that data, can operate from a unified position.” That is the purpose of the integration platform-as-a-service — the glue that holds the Cloud together.
Achieving full value from the Cloud in a manufacturing environment takes place when SaaS moves beyond being seen as single-point solutions, to being a strategic part of the environment from the very beginning, and with an integration framework that ties it all together. At that point, SaaS stops being an isolated solution, and it becomes the foundation of the disruption cycle we’re starting to see today.
Accessibility and Today’s Skilled Manufacturing
Today’s domestic manufacturing requires workers that are more skilled and better trained, and the shop floor — often packed with robotics, sensors collecting data from every end point, and with connections reaching far outside the factory and into the Cloud — is a very different place than it was in the U.S. manufacturing post-war heyday.
In this environment, factory workers and managers are not necessarily IT specialists, but they do require a certain degree of tech savvy, and “blue collar” manufacturing is a lot less grease and grit, and has taken on a decidedly tech-centric focus. As such, the accessibility, visibility and connectivity required to have a successful manufacturing cloud calls for both IT specialists and ad hoc “power users” to be able to manage the integration process.
Two things need to happen for manufacturers to leverage the integration platform and gain the full benefit of the Cloud: IT’s role needs to shift from “build-and-deliver” to one of facilitator, and front-line staff that are not IT specialists but are nonetheless tech-savvy “power users” need to be able to access the integration platform as well for ad hoc integration, without having to require IT’s direct intervention. This is absolutely essential in an agile manufacturing environment, where speed is of the essence, and integration requests simply cannot wait in the queue of an overworked IT department. IT will still do the heavy lifting behind the scenes, creating a library of ready-made connectors that can then be accessed by the ad hoc integrators and power users within the organization to use as needed, when needed.
Dan Blacharski is president of Ugly Dog Media.