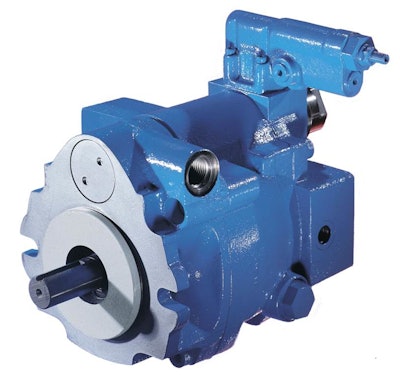
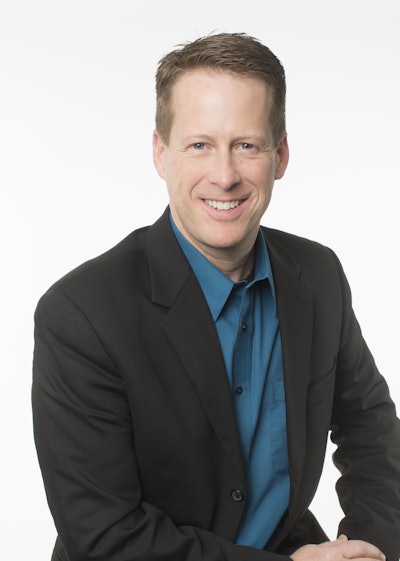
Manufacturing companies today face enormous pressure to increase operating efficiency while reducing carbon footprints. Driven by a combination of growing government energy regulations and the need to reduce operating expenses, many companies are looking to improve efficiency.
Typically, companies assume that the best ways to improve efficiency are to replace entire machines with more efficient models or retrofitting machines with more efficient motors – both costly options. However, there are other retrofit solutions that can make immediate differences in operating efficiency – without significant investment.
With the Flip of a Switch
Regardless of the machine it is powering, the efficiency of an electric motor depends on the quality of electricity that is coming to it. Old-style starters (often referred to as a contactor), which simply turn a motor on or off, transmit three-phased power from the grid to the machine. Electric motors are built to demand the same incoming voltage on each of these three leads. However, without conditioning the incoming power, that is rarely the case.
This unconditioned power impacts the motor in several ways. First, the motor must accept the different voltages as best as it can, which result in lower overall efficiency. Second, without power conditioning, motors are frequently left running, even when they are not needed, as turning power on and off with a traditional starter can cause surges in the power, which causes premature failure.
By retrofitting just one component – the traditional across-the-line starter– efficiency is immediately improved. A variable frequency drive (VFD) starter can be used in the same way as an old-style contactor, turning power to the motor on and off, and can be easily swapped out at the panel. However, the VFD starter also enables additional machine control capability, should the user choose to activate those features. In addition, VFD-style starters include built in power conditioners. Even if a manufacturer is only using the new starter for the simple on-off function, the power conditioning element makes the motor more efficient and allows the motor to be turned on and off without causing undue wear and tear to the motor or the starter.
Changing a traditional contactor for a VFD starter can make a big difference in the short term, but it also provides significant efficiency benefits down the road by enabling smarter machines that use only the amount of energy needed for the job.
Further Optimizing Energy Use
Smarter, more efficient machines are actually created by looking at the complete machine design, rather than individual components. While improving motor efficiency is certainly an important step, the machine-level approach allows complete systems across all manufacturing industries to benefit from new technology.
The retrofitted contactor solution is rightly considered a quick fix. But introducing variable frequency technology into a machine opens up a whole world of plant efficiency opportunities. By allowing manufacturers to dynamically manage the ever-changing demands of their machinery, VFDs can help balance power generation with power consumption through the use of a variable speed drive (VSD) pump solution applied to the motor. Adding a VSD pump solution offers a bigger advantage compared to only increasing motor efficiency by providing power on demand that yields substantial energy savings while providing the capacity needed for the most demanding processes.
A complete VSD solution can include the drive, as well as one or more pumps, which can be selected variable or fixed displacement vane and piston pumps. Together, the VSDs and pumps create a system which can draw on the best of electrical and hydraulic control technology to match the precise load requirements of the current duty cycle.
Starting internally, Eaton began using VSD pump solutions to improve the efficiency of the company’s injection molding equipment, and has been working to help implement this technology across a variety of manufacturing industries. The complete drive and pump solution can provide:
- Up to 70% energy savings
Instead of operating at a constant speed of 1500 or even 1800 repetitions per minute (RPM), Eaton’s VSD pumps can be precisely controlled to match the load requirements of the current duty cycle via intelligent control. By slowing or stopping the machine when the duty cycle allows, plants can eliminate energy waste.
- Quieter operation
Running a pump at variable speeds – again, rather than a constant speed – helps reduce noise whenever possible. If the machine does not need to be running, it is possible to slow down or shut down, resulting in remarkable noise reduction, which helps protect operators’ hearing and meets more stringent noise regulations.
- Reduced or eliminated cooling needs
As machines become more efficient, they produce less heat, allowing manufacturers to downsize or even eliminate oil coolers. VSD pump solutions also help reduce the amount of hydraulic oil needed and the size of your tanks, thereby extending the life of seals and oil. Both downsizing options help make machines smaller and more cost-effective.
- Pump downsizing
In addition to tank or cooler downsizing, VSD pumps make it possible to downsize pumps to cut costs. Because the system can run higher than 1500 RPM or 1800 RPM, you can reduce the pump displacement requirement proportionally for the same amount of flow— shrinking the machine’s overall footprint – and reducing overall costs.
Whether you begin by looking for a quick fix or a system wide overall, a variable speed drive solution can help improve efficiency by improving existing machine function and opening the door smarter machine control.