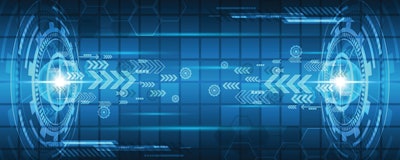
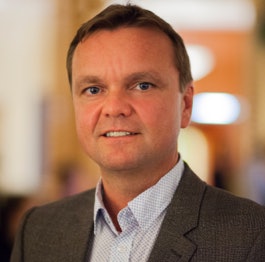
As temperatures remain high across much of the U.S. and fleet truck drivers strain their air conditioning systems, overheated vehicles becomes a major concern. Historically, avoiding a highway breakdown was due to the driver’s individual awareness. Today, IoT technology is revolutionizing how vehicle manufacturers are alerted to issues through real-time sensors which, in turn, directly impacts the safe delivery of goods to their destinations.
A shining example of connected devices are digital twins — defined as virtual enhancements of real-world assets — that are changing the product journey from concept to consumer. Gartner’s Top 10 Strategic Technology Trends for 2018 highlights the trends that will impact organizations most this year, including technologies like AI and analytics. The report shows that the next three to five years look particularly promising for digital twins, especially in the context of IoT. New market research also shows that the digital twin market is expected to reach over $15 billion by 2023. With this in mind, I’ve examined the opportunities of digital twin technology below, taking a specific look at its impact on the enterprise automotive industry.
Predictive Maintenance: Predicting Failure Before Failure Occurs
With digital twins, businesses benefit from being able to react to product issues from remote locations in real-time. Through intelligent data collection, digital twins provide manufacturers with digital representations of their products, helping remedy issues directly after moments of impact.
However, shifting from a reactive to predictive approach is even more valuable. Staying one step ahead of the roadblocks inevitably leads to success. With predictive maintenance, digital twins provide enterprises with the ability to avoid failure, reduce maintenance costs and eliminate time lost from product inefficiency.
In the case of trucking fleets, sensors linked to real-world objects visually alert manufacturers of performance issues such as brake operation, or maintenance issues, such as overheating. Through predictive maintenance, the truck manufacturer can see that a vehicle is about to break down, allowing them to digitally correct the failing engine cooling system. As a result, the driver avoids repair wait times, mechanic costs and potential safety concerns to themselves and others on the road. With this, enterprise fleets can also be ensured that shipments will make it to their destination on time and intact.
Smart Collaboration: The Benefit of Archived Insights
This success of digital twins in the enterprise stems from collaboration and knowledge sharing. In business, it’s always best to “work smart.” With this in mind, businesses should create cohesive organizational networks that are easily accessible by all stakeholders. By implementing asset intelligence networks, businesses guarantee that insights collected from digital twin sensor data are stored in a central repository. This network also houses maintenance strategies, customer service processes and performance analytics. Manufacturers can, in turn, connect and share insights about asset performance with operators and service providers over these platforms.
Consider the fleet management example: before trucks begins shipment deliveries, manufacturers, operators and service providers are cohesively aware of past automotive performance through this archived knowledge. All parties are therefore conscious of whether there were any mechanical issues with vehicles in the past before the key is put into the ignition. This knowledge not only ensures that safety standards are fully addressed, but that all stakeholders are aware of historical product performance to utilize for future corrections and accurate digital management.
The Future: Live Engineering and Performance Visualization
Archived networks of information not only provide manufacturers with the ability to preemptively correct current product issues, but help them to develop better performing products for the future. Through digital twins, businesses have a visual, data-driven understanding of how and why products failed. With this analysis, they have the power to improve future product performance and design. For instance, say an enterprise scheduled a vehicle fleet to make a cross-country journey. Prior to this, the manufacturer knows from digital analysis that this same fleet had broken down during a past trip, pinpointing the exact “how” and “why.” With this knowledge, business leaders can then adapt their approach — calculating the stressors of the journey and fixing the necessary components so that these breakdowns do not happen again.
Digital twin technology saves time, keeps employees safe and helps businesses avoid costly repairs. With these benefits in mind, it’s important for businesses to identify where their operations are falling short and what this means for not only their bottom line, but for their employees. Expectations for the technology might be high like the current temperatures, but beating the heat begins with clear analysis and implementation.
Hans Thalbauer is SVP of Extended Supply Chain and IoT at SAP.