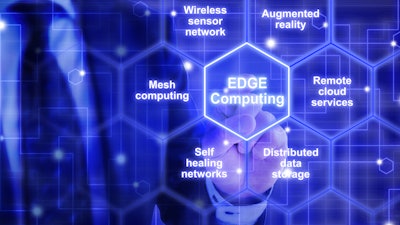
The COVID-19 pandemic slowed the deployment of Industrial Internet of Things (IIoT) technologies in factories and warehouses for several reasons, including supply chain disruptions, chip shortages and reduced business spending over economic concerns. However, it’s clear that the pandemic will likely be a catalyst for growth in the adoption of IIoT technology as companies look to maximize the efficiency of their production lines and facilities while also monitoring the health and safety of their employees.
IIoT, also sometimes referred to as Industry 4.0, simply holds too much potential value to not find a home in most modern factories and warehouses. Gartner predicts that by 2025, 50 percent of enterprises will use IIoT platforms to improve operations. Analyst firm Research and Markets projects smart manufacturing technologies will grow from $181.3 billion in 2020 to $220.4 billion in 2025, a CAGR of four percent.
IIoT connects sensors, equipment, controls, and industrial computing platforms to provide visibility and control of the equipment and processes that warehouses and factories depend on for efficient operation. These sensors and applications generate large volumes of data and need to deliver analytics in real-time for plant visibility and decision making.
This requires a computing architecture with low latency, which is impractical exclusively in the cloud. Deploying local edge computing can solve this challenge, but companies in the manufacturing sector that wish to deploy IIoT technology at the edge must proceed with caution, as these environments come with their own particular challenges.
Whether in a factory, warehouse or micro fulfillment center, edge computing supporting IIoT does not enjoy the precisely controlled conditions of a data center. In fact, this computing is typically operating in particularly harsh conditions, and failing to account for the specific power, environmental and management challenges that exist in these environments can result in reduced network performance up to and including equipment failure and prolonged downtime.
Below are several factors to consider when deploying edge computing in harsh, industrial environments, as well as best practices for addressing these challenges.
Power Variations: As with any edge location, dedicated power backup is essential to prevent disruptions in utility power from impacting system availability, but in manufacturing and automated warehouse environments power conditioning can be even more important. The machinery operating in these facilities can generate electrical noise capable of disrupting IT equipment operation. Different types of UPS systems employ different approaches to power conditioning and so the type of UPS system selected will determine how effectively the UPS will be at removing various power disturbances.
Environmental Conditions: Most factory environments are unable to maintain temperature and humidity within the range required for reliable IT equipment operation. Dedicated cooling will be necessary in most industrial environments, and that requires a plan for heat rejection. Specifically, it is preferable to reject heat directly into the factory space where it will be exhausted through the normal HVAC system or ducted directly out of the building.
Air Quality: Most factory environments also have a higher concentration of airborne dust and particulates than a dedicated data center. These contaminants can impact the reliability and life expectancy of IT equipment if they are pulled into the equipment by their fans. Protecting IT equipment requires dust-protected or sealed IT racks or enclosures that prevent unfiltered outside air from reaching the equipment. With dedicated cooling integrated in the enclosure, a clean, temperature and humidity-controlled environment is created, regardless of outside air quality.
Physical Security: The core philosophy of edge computing is to locate computing and storage close to the people and equipment it supports. In manufacturing, that typically means having IT equipment where it is vulnerable to access by unauthorized personnel. Lockable cabinets can help prevent unauthorized access. Another best practice is to deploy sensors on the door that will trigger alerts when the door is open.
Network Infrastructure Visibility: Most edge computing sites are located in environments where dedicated technical resources are scarce. Remote monitoring capabilities give centralized IT specialists visibility into equipment performance and environmental conditions, allowing them to ensure equipment is operating within manufacturer-specified ranges and power protection systems are operating as intended. When sites are equipped with additional sensors, remote monitoring can generate alerts for situations that could put equipment at risk, such as elevated temperatures, water intrusion or unauthorized access.
With so many other industries embracing digital transformation to navigate through the pandemic and other major changes in the market, it seems inevitable that more industrial companies will look toward IIoT to better track their personnel, machines and processes in order to improve efficiency and productivity. But without the proper protection or procedures, edge deployment in these environments can be difficult to implement and harmful to a company’s IT equipment, so it is best to work with a trusted partner.
To learn more, contact a local Vertiv representative or visit Vertiv.com to find the representative nearest you.