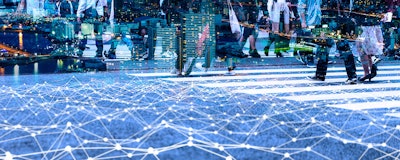
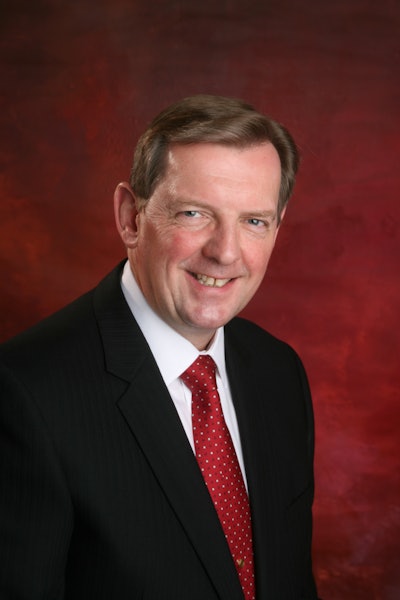
The manufacturing industry is leading the way when it comes to the Industrial Internet of Things (IIoT) implementations. Manufacturing must continuously strive to improve operations to remain competitive, and the data available through IIoT implementations enables attainment of this goal.
According to McKinsey, the manufacturing sector stores more data than any other, so there is a tremendous store of value just waiting to be unearthed. Manufacturers have been turning this data into actionable information to improve operations for decades, but in the past most implementations didn’t use the internet, but instead used internal company intranets.
Although these implementations provided value, and will continue to do so, the IIoT creates new opportunities to collect much more data, which can then be used along with existing data to further improve operations, creating smarter manufacturing plants and facilities. But there will be some challenges along the way, as with the introduction of any new technologies.
IIoT Challenges
The first challenge is converting manual data collection activities to automatic data collection. This is primarily done by installing instruments, the “things” in the IIoT, and connecting them to systems for display, analysis and other purposes. These instruments measure variables previously collected manually.
The second challenge is processing the raw data collected by instruments. The data is used for two purposes. The first is real-time control of the machine or process, and the second is viewing and analysis via the IIoT, with the “I” representing either the internet, an internal company intranet or a combination of both.
For real-time control, the data must be transmitted to the automation system, with outputs from instruments usually connected directly to the control system’s inputs. The automation system performs the data processing required for the purposes of real-time control.
Data collected for real-time control is often passed through the automation system to historians or other types of databases. This works well for data points needed for real-time control, but is a very expensive method for collecting data only needed for IIoT purposes. For this type of data, edge computing is a better solution, providing a gateway to smarter manufacturing.
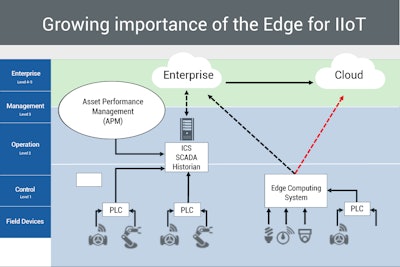
Edge Computing Fundamentals for IIoT Implementations
The Figure depicts a typical automation and IT system architecture for a manufacturing facility. Field devices such as instruments, motor drives and control valves are found at Level 0, and real-time controllers are installed at Level 1.
These real-time controllers, often PLCs, can send the data they collect to other applications at Levels 2-5. But as mentioned, this is a very expensive way to add the new points of data associated with the IIoT and smart manufacturing applications.
The data should instead be collected and processed at the edge. As shown in the Figure, edge computing systems can collect data directly from Level 0 field devices via standard Ethernet IP interfaces. They can also collect data from PLCs and other controllers not connected to Levels 2 or higher. This is often the case with PLCs used for local control of a machine, the islands of automation found in many plants and facilities. With the right level of flexibility, edge computing systems can also act as gateways to the internet by including security capabilities, critical when communicating outside the plant.
Most PLCs are IIoT-enabled with Ethernet ports, so connecting them to edge computing systems is straightforward. Many new field devices are also IIoT-enabled, but most older ones are not. For these field devices, their outputs can be sent to the inputs of Ethernet-based I/O, not shown in the Figure. These Ethernet-based I/O systems can then be easily connected to the edge computing system.
Edge computing systems are designed to not only interface with Level 0 and 1 devices and components, but also with the higher-level systems found at Levels 2-5. Most have multiple Ethernet ports for interfacing to all levels, along with support for common industrial Ethernet protocols.
Edge Computing Advantages
There are many advantages of using edge computing systems instead of sending field device data directly to upper level systems. In many cases, the field devices are simply not capable of interfacing directly to upper level systems due to hardware and software issues. This is an easy task for an edge computing system as most are designed with this functionality as a primary feature.
Sending raw data to upper level systems is very inefficient at best, and at worst results in overwhelming these systems with data processing tasks best performed at the edge. Performing data processing at the edge allows clean and compact data streams to be transmitted to all upper level computing systems.
For example, an instrument will typically transmit raw data once per second. The edge computing system can be programmed to only send data when it changes by a preset amount, greatly compacting data transmissions. Data can be filtered to eliminate temporary blips caused by process shutdowns and other abnormal operations, and it can be processed to infer likely readings when there are gaps. Some edge computing systems can even perform analytics at the edge, transforming data into actionable information, and sending it the right person directly via a built-in web server connected to the internet.
Edge computing systems differ from traditional industrial PC’s in a number of ways, providing further advantages. They can inherently support multiple operating systems and applications, making it easy to upgrade and add either or both through virtualization. This flexibility is critical for evolving IIoT implementations.
Edge computing systems are often deployed in the harsh and remote environments typically found in manufacturing plants, so they need to ruggedized. They also need to simple to deploy, use and manage. Edge computing systems must also be self-protecting to keep applications up and running, and cyber secure. Finally, an edge computing system should be able to operate autonomously to self-diagnose and repair itself, with little or no human intervention required.
All of these functions enable and ease IIoT implementations, making manufacturing plants and facilities smarter and more productive.
John Fryer is senior director of industry solutions at Stratus Technologies.