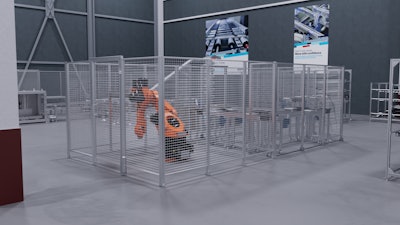
Hardware safety measures remain a critical element of the manufacturing infrastructure. While today’s plants are constantly changing to meet customer demands, it’s imperative for end users to have a comprehensive understanding of how industrial safety measures impact operations and how modern innovations are expediting and streamlining that process.
Fundamentally, end users need to stay up to date on available solutions. Safety isn’t a one-size-fits-all approach, and if insufficient shopfloor safety solutions are implemented, the consequences could not only endanger workers and equipment but also cost the end user unplanned time and resources to adjust sooner than if the right technology was purchased initially. By having a holistic grasp of industrial safety solutions, managers can be better prepared when they conduct risk assessments with third-party vendors, especially ones that represent a safety supplier. It’s critical to view these assessments through an objective lens so as not to compromise the evaluation in favor of a certain supplier’s products. For example, end users who know what options are available for protective fences are acting in the company’s best interest regarding worker productivity, and ultimately, their safety.
How has Industry 5.0 impacted how manufacturers are selecting products? By leveraging modern engineering design tools, they can take control of the initial design, assess risks, and plan for proper safety equipment before the purchase is even made. This hands-on approach is the catalyst for speed-to-market and drastically reduces repeated attempts to design and revise a line. A recent case in point involves an end user who previously had up to 20 revisions throughout the design process before they would get to a final, approved version. Sketches were done manually and often contained inaccuracies and vague directions. This would ultimately extend the design process to more than a year. But, by utilizing modern engineering software, the manufacturer was recently able to go from design to install in less than nine months. The software drastically reduced downtime and empowered the manufacturer to provide clearer direction to the supplier on exactly what they wanted. That relationship is a key component to long-term success and shouldn’t be viewed as transactional, but rather consultative. If needs or processes change, the end user should have a trusted supplier to guide them through it.
The biggest trend within manufacturing is the gradual shift to fully automated processes, and how each end-user is approaching that transition. There are a variety of safety measures to consider in such a footprint, including ISO standards that have long guided solution usage. Protective fencing is a unique use case, particularly when dealing with robotics. Humans delivering products to a robot require additional safety devices to let the robot know when a person is in the area. Having the robot wait for a human to deliver products increases cycle time and slows production. Automation designed to remove the human interaction point away from the robot makes for a safer machine, reduces cycle time, and increases production. Direct human interaction with the robot is reduced to maintenance-only procedures. Protective fencing can provide maintenance access through safety interlocked doors or removable panels. The protective fencing keeps employees away from the risk, but any access point to the risk needs to have safety interlocks to prevent the robot from running when one is open, as an employee now has access to the robot.
For semi-automated operations that maintain some element of a human workforce, safety solutions need to not only protect employees but also equip them to do their job correctly and without strain. Ergonomic technology, like manual workstations, is important so that employees aren’t straining their muscles when completing tasks in the same position for an entire shift. These systems are designed to allow flexibility to bring a product to an operator, so they don’t have to overreach and develop fatigue. Often, these workstations, which are typically made from aluminum framing, can be disassembled and repurposed into other solutions, which further adds a return on investment to a solution that already satisfies a safety necessity.
Amidst the digitalization and the concept of Industry 5.0 and the Industrial Internet of Things, safety must stay top of mind for all manufacturers, who need to be educated on what solutions are out there and how they best fit within their footprint. It remains paramount that for any manufacturing operation to be successful, there needs to be a clear and streamlined integration between all safety measures, including both hardware and software. The digital marketplace is making it easier for manufacturers to select and implement those solutions, which ultimately helps increase speed to market and promote efficient operations in a safe environment.
Chris Lupfer is the Director - Indirect Channels, Assembly Technology at Bosch Rexroth.