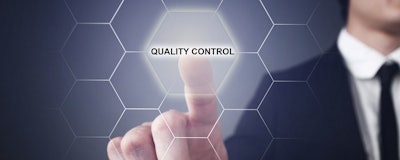
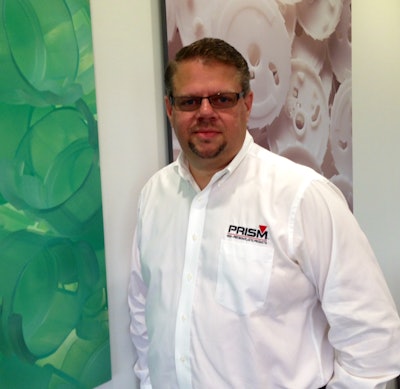
For manufacturers in any industry, high quality and consistent, reliable performance are top priorities. Traditionally, the quality control department serves as the arbiter of that quality and consistency, working to ensure that only the highest quality finished products make it out the door and that any mistakes or sub-par production outcomes are identified and addressed.
As some enterprising manufacturers are demonstrating, however, there is another way. For these forward-thinking organizations, extensive quality controls are built in to the manufacturing process with such rigor and attention to detail that the need for a quality control department is fully eliminated. By leveraging cutting edge technologies and automated processes, some organizations have achieved jaw-dropping levels of consistency, precision and quality.
To better understand how to design a manufacturing process with built-in quality controls that make it possible to operate without a quality control department, it is important to appreciate the benefits, challenges, key considerations and best practices associated with this strategy.
A New Paradigm
The quality control department is such an ingrained feature on the manufacturing landscape that the notion of operating without that safety net can seem risky, or even dangerous. The reality, however, is precisely the opposite. They key to adapting an approach that makes back-end quality control redundant is to appreciate the fact that the traditional quality control department is a reactive enterprise. It functions as a kind of after-action backstop, a way to identify and correct mistakes after they happen.
Instead of worrying about mistakes in a reactive manner, think about it from a proactive perspective: focusing on engineering every part and refining every process meticulously and with unmatched precision and consistency the first time. Commit to a quality-first approach, and use technology and automation to ensure that commitment is carried out. Such an approach can come with a higher price tag and additional complexity initially, but it saves significant resources over time. And, most importantly, it can achieve spectacular, even unprecedented results when executed correctly.
To understand what is possible, consider what we have accomplished at PRISM Plastics. As a manufacturer of high precision injection molded plastic components in the automotive, medical and industrial spaces, it is absolutely essential that we operate within tight tolerances and maintain the highest level of quality — even with high volume production. Over nearly a decade and a half, our quality-first approach has enabled us to achieve a defective rate PPM of less than one. This extraordinary level of consistent quality has been reached while manufacturing and shipping approximately half-a-billion parts per year from three facilities in Michigan and Texas — all without a quality control department.
To replicate these kinds of results, it is important to understand the details of a quality-first production process, including the best practices required to establish and maintain such a process.
Best Practices
Secure “buy in”
Quality-first requires the full and enthusiastic participation of every employee. Quality control is no longer a department, but it has to become a pervasive mindset. When everyone buys in and takes personal responsibility for quality and consistency at every step in the manufacturing process, the results can be eye-opening.
Focus on the process
The process is the beating heart of your operation, and repeatable processes that minimize variation and ensure consistent quality are absolutely essential. Every manufacturer is different, but all sound production processes display certain universal characteristics. Foremost among those is:
- Simplicity, using uniform (and therefore interchangeable) equipment and materials;
- Automation, relying on automated processes that can be easily monitored and controlled;
- Intelligence, using detailed, real-time information to track production and help further refine the process; and
- Vigilance, firmly maintaining strict adherence to established systems, standards and processes.
Design matters
Beyond the process itself, the design of the production facility can impact your quality outcomes. A thoughtfully designed facility can streamline and simplify production. Generally speaking, work to focus your efforts on a few key products in consistently designed and highly controlled environments. Outsized ambition and complexity are the enemies of consistency and quality. Limit the size of each facility and the number of machines/equipment operating in each. With fewer machines and automated processes, it is easier to operate longer hours and with fewer monitoring personnel. Facility standardization is also important. With layout and functionality consistent across different facilities, equipment, processes and personnel can transfer easily from one to the other without a loss in efficiency or consistent quality.
Take your measure
Eliminating the quality control department does not eliminate your need to monitor processes and outcomes. Gathering sophisticated and highly targeted metrics and measurables make it possible to conduct periodic in-depth analyses of processes and performances.
Utilize automation and technology
The phrase “you’re only human” resonates for a very good reason: humans are imperfect, and mistakes happen. A quality-first approach, however, requires that mistakes do not happen. The best way to eliminate mistakes is to reduce variation, and the best way to reduce variation is to replace that human element with automated processes wherever possible.
For instance, using a combination of pneumatics and optical detection helps ensure mold integrity at all times. Our facilities utilize CT Scanning extensively to perform part validation, wall thickness and void/inclusion analyses, and make part-to-CAD and part-to-part comparisons. CT scanning allows engineers to operate within even the tightest tolerances and most complicated cavitation.
Ultimately, quality control is not a discrete step in the process, it is an ongoing priority. By treating it as such, and taking meaningful steps to ensure quality throughout the manufacturing process, you can eliminate your quality control department while simultaneously achieving exceptional results for quality and consistency.
Rod Bricker is co-founder and president of PRISM Plastics.