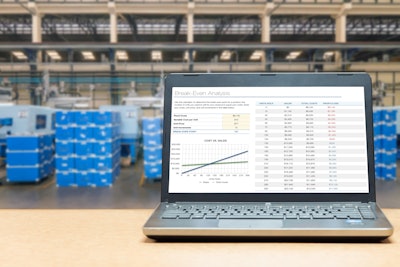
Manufacturing’s economic role is changing. It’s still a key economic driver, but the way manufacturing creates jobs and improves productivity has shifted. The primary focus today is on using big data to drive productivity gains.
Harnessing the power of big data to improve efficiency and ramp up productivity requires the ability to reveal new insights and unleash innovation. Big data analytics allow manufacturers to recognize previously hidden patterns and uncover new information, which in turn can lead to better processes, more control over production variables and more efficient supply chains.
None of this is news to manufacturing leaders: 67 percent are planning to make investments in big data analytics, according to a Honeywell Process Solutions-KRC Research survey. These leaders understand that big data analytics can help them reduce costs and compete effectively.
Generating Performance and Efficiency Gains
Even a small improvement in asset performance can lead to big increases in productivity. Reducing equipment breakdowns decreases inefficiency and prevents losses from unscheduled downtime, which is why manufacturers concentrate on optimizing asset performance.
To improve asset performance, manufacturers find valuable data on machine logs, and the Internet of Things (IoT) can further enrich that data by enabling the flow of real-time performance information. For many manufacturers, coping with a large stream of information is a challenge, but the right data integration, management and analytics tools can handle the volume and put data into perspective.
Big data-driven predictive maintenance can also help manufacturers maximize the value of assets by preventing expensive breakdowns and unexpected downtime. The Honeywell-KRC research showed that big data analytics can decrease breakdowns by up to 26 percent and reduce unscheduled downtime by almost 25 percent.
Improving Production and Supply Chain Operations
Supply chains are longer and manufacturing processes are more complicated today than in years past, thanks to increasing inter-connectedness and globalization. As a result, manufacturers who are seeking ways to streamline processes and improve supply chain operations need to be able to review process components and supply chain links in detail. Big data analytics make it possible.
Using sophisticated analytics, manufacturing leaders can evaluate every step in the production process and review supply chain operations at the granular level. With the ability to zero in on the smallest details, manufacturers can identify where improvements are needed and identify dependencies in creating contingency plans.
The manufacturing sector has traditionally focused on mass production, leaving customization to niche market operators. It wasn’t that manufacturers weren’t interested in the customization market, but from a time and cost perspective, it made sense financially to focus on mass production. That’s changing.
Now that analytics tools can detect signals that indicate a change in customer behavior more quickly, manufacturers can have more lead time to produce customized products at a lower price point. Innovations in big data analytics can allow product engineers to capture, analyze and visualize customer behavior almost instantly.
With the tools needed to closely examine each stage of processes, manufacturers who use big data analytics can see where customization work can be inserted into production on the factory floor, or where they can halt production to allow partners to complete customization. This provides new opportunities for manufacturers to compete in the lucrative product customization market.
A Deloitte study on the mass personalization sector shows how the ability to delay completion of the production process enables manufacturers to profitably take on made-to-order requests. The study also says that postponing production can allow manufacturers to increase factory efficiency and reduce inventory.
Eight Tools in Big Data’s Toolkit
Forward-thinking manufacturers are already optimizing asset performance and using big data tools to increase profits, diversify product lines and become more efficient. Here are eight tools in the big data manufacturing toolkit that are making a difference:
- Data storage: Data-driven manufacturers need adequate storage to house information on equipment, supply chain operations and production processes. With robust data storage capabilities, they can access the datasets they need for analysis.
- Data cleanup capabilities: It’s essential to have tools that enable users to receive and integrate data in all the formats in which it arrives — from every source. Manufacturers use cleanup tools to transform unrefined data into standard, usable formats for sharing and analysis.
- Profiling abilities: To gain maximum transparency into production processes and supply chains, manufacturers use profiling tools to capture information. This allows them to inventory data and maximize its value.
- Data mining tools: Data discovery tools let manufacturers access the exact information they need when they need it, which supports production and supply chain decision-making.
- Data mapping capabilities: Mapping tools enable manufacturers to quickly identify dependencies and create plans to prevent bottlenecks. Data mapping also improves security by allowing users to identify leakage and risk.
- Analysis tools: Data analytics give manufacturers key insights by revealing patterns, predicting outcomes and measuring impact. Armed with the ability to analyze bottlenecks, predict equipment failures and identify supply chain problems, users are better decision-makers.
- Data visualization tools: The ability to see data in visual form is a game-changer, making dependencies clear and results unmistakable with charts, graphs and more. A literal “big picture view” lets decision-makers react much more quickly.
- Data monitoring: Results depend on data quality, so manufacturers need data monitoring capabilities to ensure their information meets quality standards. Data monitoring tools allow them to keep tabs on equipment and production performance, and automate quality assurance.
Manufacturers recognize that big data analytics aren’t a luxury — they’re a necessity in an increasingly data-driven economy. That’s why manufacturing leaders who fully understand data’s potential are looking for end-to-end solutions.
When seeking a big data solution, it’s important to keep in mind that comprehensive data integration and management capabilities are the key to unlocking the value of data and gaining insights to improve productivity and efficiency. With cutting-edge data integration and management tools, manufacturers can use big data to compete and win.
Andy Uhlenberg is a Senior Account Executive for Liaison Technologies, a leading cloud-based integration and data management solution provider. Liaison's ALLOY® platform is focused on breaking down the barriers between data silos.