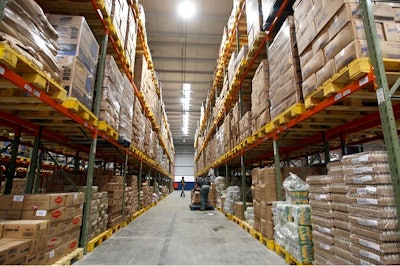
Today, spreadsheet-based warehouse inventory monitoring systems are becoming a thing of the past, and manufacturers, distributors and wholesalers need a good warehouse management system (WMS) in place in order to become more efficient and to stay current and competitive. Instead of just treating every customer individually, it is now necessary to make sure that everyone—retailers, wholesalers and distributors—has access to more information. This enables your supply chain to blend seamlessly together and have a better working relationship, from the beginning of the distribution process to the end.
A WMS system can also help by coordinating your warehouse layout in a more effective way so it enhances your workplace flow and provides everyone with more accurate information. It's harder to manage your inventory if you don't have proper visibility of your products at any given time. Also, when your WMS and warehouse are not set up in an efficient way, workers could spend a lot of effort searching for items in places that are too far apart, which can slow down production. Let's take a look at a couple of areas to see how warehouse layout can go hand in hand with your WMS in order to provide better efficiency.
The Receiving Area
Ideally, the best receiving practices are to move items to their storage locations with as fewer touches as possible, especially with products within the food and beverage, medical device/pharmacy and soft goods industries, where items are time-sensitive or more prone to damage. You can set up your WMS to know your warehouse layout and it will inform you exactly when your inventory is due to come in. In this way, you will have more accurate receiving schedules that communicate information about incoming loads prior to their delivery. This will allow workers to pre-assign storage locations and reduce an item's receiving cycle time. This is important because items held in receiving for too long can become damaged or perish, and problems in this area can trickle down and affect every aspect of your company. With proper coordination between layout and WMS, you save on time, labor and costly mistakes, and the incoming product will have fewer touches overall.
The Stocking Area
This space should ideally be located as close to the receiving area as possible in order to reduce damage to goods. If possible, placing these items near enough to the eventual active picking location is better because it will minimize a worker's total replenishment travel time. Your WMS can help you with a more accurate placement design and can also allocate certain items based on velocity. In this way, a faster-shipping product can be stored for a shorter period of time, and the system will show it needs to be placed closer to the picking station. A slower-shipping item that is replenished less frequently can be placed further away. The WMS also helps with the speed and efficiency of your workers, because it tells them exactly where received goods should go as soon as they come in. By having accurate, updated cycle counts to guide them, they can start placing items as soon as possible. This helps with better inventory control as well, because workers can easily check an item for product availability before they start stocking, and if there is something in an "empty" spot, they can identify it as an inventory issue and then update the item as having been recovered.
Another way to simplify things is by dividing your facility by zones based on the pick type. Similar items with the same storage and picking methods will then be grouped together, which should make the order picking and re-slotting process even easier.
These are just a few of the ways your WMS can help you have a more coordinated and effective warehouse layout so your inventory will stay current. This system also provides you with more accurate information on product availability and location for a better, more speedy and efficient service. This is especially important when working in industries such as food and beverage, pharmaceutical and soft goods, where ensuring product safety and availability is key to customer satisfaction. To sum it up, Davison Schopmeyer, managing partner with enVista’s Supply Chain Service Group says, "Consumers are now thinking in terms of ‘days’ and ‘hours’—not weeks—when it comes to deliveries, and that’s pushing the need for real-time visibility, more accurate data and better flow-through type processes in the warehouse." We couldn't agree more.
Joe Vitiello is VP of Professional Services for Aplicor. To learn more about how a warehouse management system can help your company, contact Aplicor at www.aplicor.com.