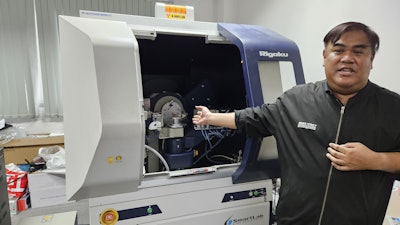
BANGKOK – Trade tensions and tariffs continue to push U.S. manufacturers toward diversified operations. This shift has opened the door for countries like Thailand to showcase its industrial potential.
READ MORE: China Tariff Crunch Not Going Anywhere: 4 Moves to Make Now
Thailand’s industrial growth, especially in the semiconductor and advanced electronics industry, recently received strong government backing. Meanwhile, the country’s educational institutions and companies collaborate to align classroom learning with local factory needs.
Last December, Thailand’s Semiconductor Board approved the framework for a national semiconductor strategy and an initiative designed to train, upskill and reskill more than 86,000 people in preparation for a surge in foreign direct investments that the Thailand Board of Investment (BOI) expects to approach $15 billion.
Worth noting, the Semiconductor Board is chaired by Thailand Prime Minister Paetongtarn Shinawatra.
An interactive digital display at the Thailand Board of Investment's office in Bangkok shows the country's business landscape.Nolan Beilstein
Tanita Sirisup, the BOI's senior executive investment advisor, said the board will work with a global consulting firm to conduct a study that supports the development of the Semiconductor Board’s strategy.
“The policy framework will provide opportunities for semiconductor manufacturers to diversify their production base in a country that offers a conducive investment environment as well as market opportunities in the smart electronics and automotive industries,” Sirisup said.
The training, upskilling and reskilling initiative includes 1,400 master’s and Ph.D.-level researchers. However, Thailand’s university education system follows a significantly different approach from what young manufacturing workers in the U.S. have experienced.
Pitcha Prasitmeeboon, the vice president for international affairs at King Mongkut’s Institute of Technology Ladkrabang (KMITL), offered insight into both systems having earned her bachelor’s, master’s and doctoral degrees at Columbia and UCLA.
She explained that KMITL applicants must commit to a specific program before setting foot on campus. Once enrolled at KMITL, the students follow a largely predetermined four-year schedule that centers around a common core of math and science courses.
The school’s engineering programs also implement project-based assignments into fixed semesters to keep students on a unified track and encourage them to begin hands-on projects in their first year.
In contrast, American colleges and universities promote a more holistic experience as students explore various studies before committing to a major, take electives beyond their core courses, switch majors and pursue degrees outside their initial focus.
The classroom structures also differ with Thai professors managing all aspects of a course, while American institutions often rely on graduate and undergraduate teaching assistants to help with labs, recitations and grading.
“More than 90% of [KMITL] graduates move directly into industrial roles thanks to a curriculum co-designed with partner companies, compulsory internship and optional co-op placements that immerse students in live factory environments and a teaching philosophy that frames theory through hands-on problem solving,” Prasitmeeboon said. “This tight industry linkage ensures skill-for-skill matching, so new hires don’t have to relearn basic tools or workflows and will soon be documented in a personalized ‘Skill Transcript’ that scores each student’s hard and soft competencies, giving employers a data-rich snapshot of their job readiness.”
Prasitmeeboon also highlighted the benefits of a flexible approach to education, which she said encouraged interdisciplinary learning and adaptability.
“The exploration in various classes, such as arts, histories and humanities, helped develop critical thinking, communication and cultural awareness by exploring human experiences and expressions throughout history and across cultures,” Prasitmeeboon said. “These courses encouraged students to analyze information, understand diverse perspectives, and grapple with complex questions about what it means to be human.”
Still, Thailand’s tight alignment between academia and industry directly benefits its semiconductor and electronics companies.
Delta Electronics displays products at its facility in Thailand.Nolan Beilstein
K. K. Chong, the head of sustainable development at Delta Electronics (Thailand), said the company’s Automation Academy, operated in partnership with seven Thai universities, accounts for the majority of the company’s new hires.
According to Chong, the decade-old program provides training for students and university faculty using Delta’s industrial automation equipment.
“As of 2024, more than 3,000 students have participated and benefited from the program,” Chong said. “Over 70% of our new hires are from the partner universities, which are among the top engineering universities in Thailand.”
Silicon Craft shows its products at its facility in Thailand.Nolan Beilstein
Bodin Kasemset, the CEO of Silicon Craft Technology, said his company encourages high school students to enter semiconductor engineering programs at its partner universities, developed through collaborations with government education offices.
Kasemset added that Silicon Craft’s partnerships with universities and professors involved in funded research projects help the company recruit interns during their third or fourth year of school.
Different educational systems have led to varying workforce demographics between Thailand and the U.S., as seen at Kimball Electronics, which operates one facility in Thailand and two in the U.S.
“There is a more balanced mix of gender of workers in the same job in U.S. factories, while one gender may be a majority in the same job in the Kimball Thailand factory,” Kimball Electronics (Thailand) Limited General Manager Meechai Charatpattanawong said. “The age range of workers may be wider in U.S. factories, whereas the age of workers is more concentrated in a particular range in Kimball Thailand.”
Products on display at Kimball Electronics' Thailand site.Nolan Beilstein
Perhaps the most noticeable difference between U.S. and Thai factories is the presence of women on the factory floor. As U.S. manufacturers struggle to attract women to factory roles, these positions are often held by women in Thailand and throughout Southeast Asia.
More Thai women have entered the workforce, but cultural expectations still mainly position men as primary providers. As a result, Charatpattanawong explained that, in industry, men tend to work more “heavy-lifting, higher skill jobs” that pay more, while women typically take on operator positions on production lines.
“In contrast, many entry-level manufacturing jobs in the U.S. have either been automated or relocated offshore, which may explain the lower visibility and appeal of such roles among women there today,” Chong said.
Thailand’s coordinated efforts, including government policy, education and workforce development, position the country as a competitive alternative for manufacturing investment. As U.S. companies evaluate expansions, Thailand presents a compelling case.