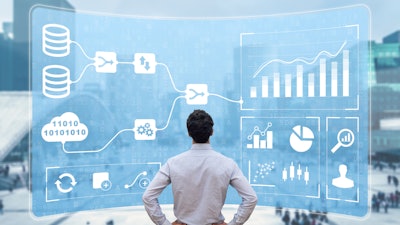
To help organizations increase the efficiency of global supply chain operations, Oracle offers their Smart Operations. It offers new supply chain execution capabilities in Oracle Fusion Cloud Supply Chain & Manufacturing (SCM). Powered by advanced technologies like artificial intelligence (AI), the new capabilities within can help customers improve factory output by increasing productivity, enhancing quality, reducing unplanned downtime, and improving visibility across operations.
βAs organizations look to insulate their operations from ongoing disruptions, many leaders are turning to technology to increase output, improve quality, and build resiliency,β said Chris Leone, executive vice president of applications development, Oracle. βThe new smart manufacturing and maintenance capabilities can help our customers reduce manual recording and monitoring processes, increase safety, improve quality, and optimize operations.β
Smart Operations for Manufacturing, Maintenance
The new capabilities within Oracle Cloud Manufacturing enable customers to combine data from connected equipment, the workforce, and supply chain processes to deliver real-time recommendations, autonomously adjust production, and execute on high-value manufacturing decisions. New capabilities include:
- Operator Workbench: Provides customers with a single user interface to capture and access information and insights as they complete day-to-day operations, such as operation start/stop, time tracking, materials and tools required, and production exception reporting. With a simple and user-friendly environment and automated data capture, machine operators have clear visibility into their daily tasks, and assembly workers gain more autonomy to execute orders and quickly track and record production.
- Digital Work Instructions: Help customers simplify complex assembly operations, including manual and automated assemblies, and enforce procedures to improve quality and consistency. With simple, intuitive work instructions, machine operators and assembly workers can improve productivity, quality, and safety, while addressing compliance.
The new capability within Oracle Cloud Maintenance enables customers to combine maintenance data with real-time asset information, workforce, and supply chain data to enable continuous monitoring and predictive maintenance. The new capability includes Maintenance Technician Workbench, which helps maintenance technicians access relevant work based on assignment or skill, while also providing insights into service history and supporting seamless collaboration with other workers.
With a single mobile user interface for all technician work execution, customers can make faster maintenance decisions. βBeing a premium player in the automotive aftermarket industry places a critical focus on our manufacturing and maintenance operations. Our customers expect a consistently high-quality product and an on-time delivery, which is increasingly challenging with the continuous supply chain disruptions around the world,β said Stefano Mariani, head of IT, Alcar Ruote. βWith these new capabilities in Oracle Cloud Manufacturing and Oracle Cloud Maintenance, our production operators will be better able to work with speed and accuracy, while capturing all of the key data associated with that work."