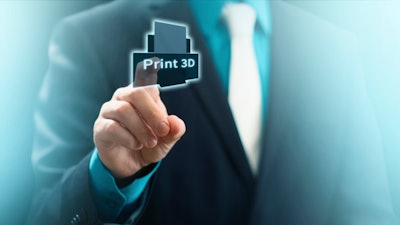
Nintendo. Walkman. The Clapper. We’ve come a long way since the 1980s, when original equipment manufacturers managed mass production of products.
Manufacturing electronics the “old” way, however, typically involves multiple steps and can take weeks or months to create a final product. Additional drawbacks include high tooling costs and limited design and customization options.
Technological innovations have led to more precise, less costly manufacturing methods, like direct-write three-dimensional (3D) printing. 3D printing, or additive manufacturing, has emerged as a powerful technology that enables the creation of complex structures through layer-by-layer deposition of materials.
A new additive manufacturing technology, direct-write 3D printing, dispenses functional inks and pastes, significantly expanding the types of materials that can be 3D printed. During the direct-write process, a micro-dispenser moves over a substrate to precisely deposit the required amount of ink or high-viscosity paste to print complex shapes in layers.
Direct-write technology employs materials like metals, polymers, composites and ceramics and can be combined with traditional 3D printed materials. Its ability to integrate multiple materials seamlessly into 3D results in the development of new, smaller smart objects. Further, direct-write 3D printed electronics allows for the integration of electronic components and sensors into 3D-printed devices, further enhancing their capabilities.
Exploring the Potential
Direct-write 3D printing fosters more advanced innovations and opens new possibilities for creating smaller, more compact electronic devices. It can produce:
- Interconnections for a variety of electronic devices, including printed circuit boards (PCBs) and flexible electronics.
- High-precision sensors with fine detail and intricate design.
- Actuators with complex shapes and structures.
- Energy generation and storage components, like batteries and solar cells.
Leading innovations in direct-ink writing show potential for fabricating more complex printed electronics including stretchable, organic and hybrid electronics, sensors and transducers. Users can produce wearable sensors, displays and circuits on-demand. Direct-write 3D printing also allows for the creation of multi-layered devices with high levels of accuracy and fine feature resolution. Additional benefits include:
- Speed and convenience: Fast prototyping and on-demand spare parts production eliminates long lead times or minimum order quantities.
- Cost-effectiveness: For small production runs or low-volume production, 3D printing can be less expensive as compared to traditional manufacturing methods.
- Sustainability: 3D printing can reduce waste and minimize material usage.
- Availability: 3D printing allows for customization of specialized parts not readily available on the market and increased availability of obsolete or discontinued products.
As innovations in direct-write 3D printing continue, these cutting-edge developments allow for real world applications and ultimately better technological advancements across many industries. Most notably, healthcare, automotive and sports industries have seen the most progress in the last few years due to the adoption of this technology. The architecture, entertainment and aerospace industries are not far behind.
Direct-write 3D printing allows for the creation of complex 3D shapes with precise control over architecture and dimensions, resulting in minimal usage of valuable materials. This technology has fostered the development of numerous novel form factors and composites and offers vast potential for applications in various fields including electronics, biomedicine and structural materials. This includes:
- Healthcare applications. Novel medical devices, wearables and health monitoring systems can all enhance clinical care quality. The integration of sensors into conventional and innovative materials will facilitate continuous monitoring of patient health beyond healthcare clinics. Furthermore, researchers are increasingly utilizing 3D printing technology to help meet objectives and expedite product time-to-market.
- Automotive applications. Within the automotive industry, direct-write 3D printing will enable faster design, testing and deployment of new and innovative car parts. This means that smaller and more complex sensors, strain gauges and other electronics that optimize car design and safety may be printed on-demand. This will be key to lowering costs for major car manufacturers without compromising quality, and it will work towards solving supply chain issues.
- Sports applications. The professional sports industry is seeing an increase in the use of equipment integrated with sensors, made possible by the innovation of direct-write 3D printing. These sensors are designed to track variables like heart rate, altitude and impact. Notably, nanoscale sensors are also capable of detecting injuries, including concussions, by providing relevant data. An increasing number of helmets, mouthguards and shoulder pads are equipped with these sensors, which can evolve into smarter versions of their former selves, thus enhancing their functionality and efficacy.
Direct-write and direct-ink writing are revolutionizing the way electronic components are designed and produced. In addition to the healthcare, sports, and automotive sectors, numerous other industries will reap the benefits of direct-write technology through enhanced productivity, accelerated research and development, and solutions to supply chain challenges.
Ramsey Stevens is CEO of nano3Dprint, a next-generation additive manufacturing solutions provider, and founder of Carbon Design Innovations (CDI).