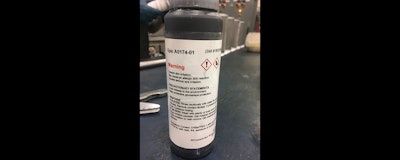
Although standard “office” labels are more than sufficient for routine applications like filing, addressing envelopes, and shipping boxes, they are not designed to withstand the range of conditions and hazards found in harsh industrial settings such as warehouses, production lines, laboratories, or construction sites.
Yet despite the availability of more durable offerings, many continue to use office-grade, “paper” labels for everything from warehouse racks and equipment to identifying chemical containers. This is often due to familiarity with such products from business settings, and perhaps an incomplete understanding of the significant differences in substrates, adhesives and other technologies used to design labels for specific applications.
Fortunately, film labels are available that are engineered to withstand harsh industrial environments. Some are even tested and certified to meet existing safety and regulatory requirements. These self-adhesive labels can be utilized for everything from barcoded asset tags on machinery to location IDs on parts bins and affixed to a variety of surfaces found in industrial settings such as metal, wood (pallets), glass, plastic and ceramic.
Paper Labels In Industrial Settings
There can be serious consequences to using standard paper labels in an industrial setting. For example, exposure to moisture, abrasion, chemicals, heat, and even sunlight can lead to torn, smeared, discolored, unreadable labels, or labels that fall off.
This can compromise safety, reduce productivity, and may lead to regulatory fines or legal consequences. For example, a missing or illegible label could not only result in an OSHA fine, but also serious injury and litigation if someone were to spill a bottle of a harsh chemical or worse, consume it. Similarly, equipment damage, unusable product, and downtime could result if the wrong solvent or lubricant is used in production.
Even slightly damaged labels can be surprisingly costly, such as when inventory barcode scanning errors lead to misplaced equipment and inventory. Besides the cost of the label, estimates peg the labor costs to reprint the label at $10-$20, with up to $100 more to identify and fix any issues related to incorrect scanning.
Characteristics Of Durable Labels
Although standard paper labels and industrial film labels appear similar at a glance, a tremendous amount of R&D and testing goes into creating each product so that it works for its intended application. Because of this, it is much more cost effective to use the right label from the start.
“There are significant differences between office labels and industrial film labels, including the materials and adhesives used,” says Tina Huff, a group product manager at Avery Products, a leader in printable, self-adhesive labels. “For the best results, they should work with a trusted supplier that tests labels for their intended uses and provides specifications for resistance to water, chemicals, abrasion, UV, as well as service temperatures on request.”
According to Huff, most self-adhesive labels are constructed of four key layers: a topcoat, substrate, adhesive, and liner. “The material characteristics of each of these layers determine how well typical paper, durable industrial, or any label, performs in its workspace,” she says.
Since standard paper office labels are intended for an indoor environment, the topcoat is not waterproof, and the paper substrate tears easily and is not moisture or chemical resistant.
In contrast, film labels can have a protective topcoat that is waterproof, even extremely chemical resistant in some instances. The substrate is a durable, scuff and tear-resistant film that can be made from materials like polyester and vinyl. The adhesive is high performance permanent that is also waterproof and chemical resistant. While the topcoat, substrate and adhesive can vary for an industrial label, each adds a level of strength to the entire label “sandwich” construction.
To ensure products will perform properly in the field, companies such as Avery scientifically test and evaluate how the labels stand up to a host of potential situations found in industrial environments. These tests run the gamut, and can include exposing labels to a variety of common industrial chemicals such as isopropanol, and hydrochloric acid, as well as with cleaners, fuels, oils, lubricants, and salt water.
In addition to increasing the durability of the label topcoat and substrate, additional innovations in label design and construction can improve performance further.
Avery, for example, offers labels with technology which ensures that if a new label with TrueBlock® technology is placed over another label that has any printed information, the old information does not bleed through which could create confusion, cause incorrect bar code scans or simply make it difficult to read.
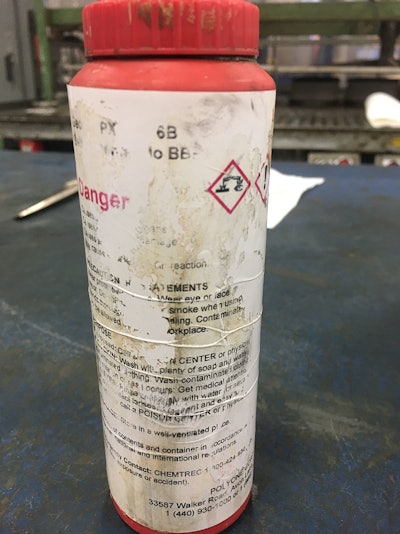
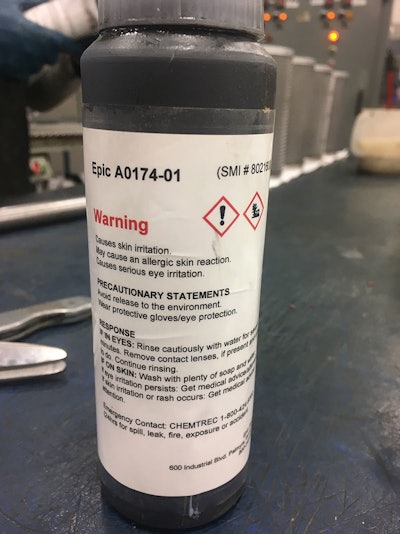
Another innovation, Self-Laminating Labels, addresses a common workaround when using office-grade labels: covering them with clear tape in an attempt to increase longevity. By offering true lamination that can be easily applied by the user, these labels provide extra protection against abrasion, dirt, moisture, chemicals and UV.
For Natalie Davis, a Product Design Drafter and Safety Coordinator at Itasca, IL-based Solberg Manufacturing, utilizing paper labels covered with tape clearly was not working.
“Our previous labels on our acetone and alcohol dispensers in the production area kept rubbing off and had to be replaced,” explains Davis. “We tried putting see-through tape over the labels for protection, but the incompatibility of the tape with the harsh chemicals caused the tape to crinkle and the label was impossible to read.”
When Davis switched to Avery Self-Laminating Labels, she found it resolved any issues of label readability and longevity.
“I put the durable labels with clear self lamination on all our dispensers, and after weeks of use and handling, it hasn’t really affected the labels,” says Davis. “The label information is easy to read and the clear lamination is easy to clean if it gets dirty. This has improved safety and saves the time and expense of having to print new labels and switch the labels every week.”
Global Harmonized System (GHS) labels represent another improvement in label durability that can be critical to achieving compliance with new government regulations.
GHS labels, which are regulated by OSHA and established by the United Nations to create a unified system for identifying and communicating hazardous chemicals, are required on chemical containers, including smaller containers used in down packing.
When Lani O’Connor, a Safety Manager at Tollman Spring Co. could not find any small GHS labels, “As a temporary solution, I began printing our GHS labels on regular paper stock,” she says. “Since they weren’t chemical resistant, the ink would quickly smear and run. I was spending a lot of time printing and replacing labels.”
After doing some research, O’Connor discovered Avery UltraDuty GHS Chemical Labels. These labels were created to withstand outdoor use for up to two years, are tested to be waterproof for at least 90 days and resist a wide variety of chemicals while remaining difficult to tear. Due to the harsh environments these labels are used in, the products are typically rub-tested with wet sandpaper.
“The first time the labels came out of our printer they worked perfectly,” says O’Connor. “The labels are chemical resistant and are available in a number of sizes that accommodate all of our GHS labeling needs.”
These industrial labels are compatible with laser or inkjet printers. Users can print in full color using a printer they have on hand, without having to purchase a specialized and costly thermal transfer printer, plus multiple colors of ribbons.
Armed with a better understanding of industrial labels, safety and facility managers can now avoid the pitfalls of using office-grade paper labels in such harsh settings. By doing so, companies not only eliminate the time and energy required for frequent replacement of labels, but can also avoid potential confusion and the additional hidden costs when labels become unreadable, fall-off, or otherwise fail.
Del Williams is a technical writer based in Torrance, California.