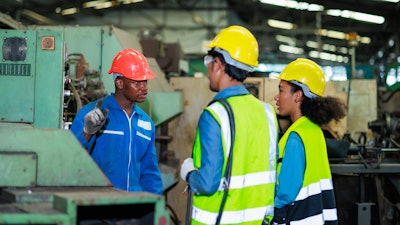
A 2018 survey published by the Manufacturing Institute says that 3.5 million manufacturing jobs will need to be filled in the next decade, and 2.4 million will go unfilled. As of December 2023, there were 601,000 unfilled manufacturing jobs.
How did manufacturing ever get into this jam?
The National Association of Manufacturers (NAM) and their Manufacturing Institute have been surveying their members on the skilled worker shortage for at least 20 years. Still, there is no evidence their membership anticipated the current crisis of skilled and entry-level workers by investing in training programs to replace retiring workers.
In fact, a January 2020 training survey by the Manufacturing Institute shows that the average number of hours of training per employee among their members is only 27.7 hours per year—and for new employees, it was 42.9 hours per year.
Why is it hard to recruit workers
- Labor Participation Rate (LPR): The LPR rate dropped from 67.2% in 2001 to 62.5% in January 2024. The Bureau of Labor Statistics projects it will continue to decline over the next decade due to the aging population.
- Birth rate: The number of U.S. births has been declining every year since 2008. Experts say women are becoming mothers later in life. The fertility rate in the U.S. declined from 2.12 (births per woman) in 2007 to 1.64 in 2020—though it ticked up to 1.66 in 2021.
- Retirement: Millions of skilled manufacturing workers have retired, and another two million will retire by 2028.
- Reducing immigration: Immigrants have been a source of new manufacturing workers, and the industry will continue to need immigrants for entry-level jobs now and in the future. However, Republicans in Congress want to reduce immigration with sweeping changes in border security, asylum, parole, and broad extension of entry for specific kinds of migrants—this could make recruiting entry-level workers harder.
- Bad image: Young people, their parents, and counselors do not consider manufacturing a good career. They have watched as multinational corporations outsource jobs and close plants for decades. Surveys show that one in three parents won't encourage manufacturing as a career.
- Public education: Education is still focused on getting a college degree. Vocational training and the trades have been deemphasized for many years.
- Competition: Manufacturers face heavy competition for entry-level talent from warehouses, distribution centers, and delivery companies, which is feeding the e-commerce boom.
- Work flexibility: Many young people want more flexibility and a work-life balance and are less willing to accept traditional 8-to-5 jobs.
- Apprenticeships: Manufacturing has not invested in the advanced training needed to replace skilled workers. The Department of Labor website for Registered Apprentices shows that in 2009, there were a total of 420,000 registered apprentices and 18,889 (6.6%) were in manufacturing. Today, there are 585,000 people registered in the federal apprentice program, and only 15,600 (3%)are in manufacturing. The total number of apprentice registrants in other industries has grown by 28%, but the number of manufacturing registrants has declined.
Despite all the publicity, high school workshops, and Manufacturing Day ceremonies, I don't think the public's view of manufacturing will change until multinational corporations address the issues of job security, training, and wages.
The days when manufacturers could put an ad in the paper to find a skilled or entry-level manufacturing worker are, for the most part, over. They are fishing in a shallow lake that has been fished out. If manufacturing wants more skilled workers, it must create them from scratch. They need to invest in the advanced training necessary to create the skilled workers they need now and in the future.
Solutions
Manufacturers need to create a culture that prioritizes worker satisfaction and appreciation. They need to build a positive culture that can appeal to a wide variety of younger workers. Here are some ideas:
- Job Security: Every student and parent knows that multinational corporations have outsourced jobs and closed plants for 40 years. Changing the view of manufacturing as an unstable industry will require corporations to offer job security and long-term employment. It is the primary obstacle to recruiting the skilled people needed.
- Career: To recruit the necessary people, manufacturing really needs to describe the opportunity as a career—not just another job
- Competitive Wages: America's corporations have been on a 40-year crusade to lower labor costs. According to the Bureau of Labor Statistics, in 2023, non-supervisory production workers in manufacturing were making a mean hourly wage of $17 per hour or $32,640 per year. To attract entry-level workers, the industry will have to match the starting wages of companies like Amazon and FedEx.
- Diversity: Manufacturing must diversify and appeal to underrepresented groups such as women, people of color, people with disabilities, and veterans. If recruitment of women becomes a priority in manufacturing, then manufacturers will also have to address the problem of child care.
- Apprentice Training: Manufacturers also need to publicly commit to long-term job training and paid internships. Replacing the highly skilled workers leaving the industry will require some kind of apprentice training that leads to journeyman status. This advanced training is a step towards a career, not just a job. If companies want to reshore production to the U.S. or bid on upcoming infrastructure projects, they will have to bite the training bullet and create the skilled workers needed. The government could help by offering apprenticeship loans to help companies finance this training.
- The Gig Economy: Young people want more flexibility and a work-life balance. One answer is the gig economy, which offers more flexibility, new challenges, and travel. These traveling gig workers might be a new source of both the entry level and trained workers.
Mike Hagen, CEO of American Structures and Design in Sumner, WA., suggests that diversity also needs to include non-native English-speaking immigrant employees and second-chance employees coming out of the penal system—or recovering from substance abuse. Hagen also thinks that if manufacturing is going to hire more women in manufacturing, childcare support must be addressed.
Childcare solutions vary from government subsidies to help defray the cost to providing facilities on-premises for childcare. To meet the need for work flexibility, he suggests that companies consider hybrid work schedules, such as working four ten-hour days and allowing remote work on certain days of the week, to allow white-collar workers flexibility with their family lives.
Timeline According to Manufacturing Institute and Deloitte Surveys:
- 2003: 10 million skilled workers will be needed by 2020
- 2005: 90% of survey respondents report shortages of skilled workers
- 2015: 3.5 million manufacturing jobs will need to be filled by 2025
- 2018: In the decade 2018 to 2028, 2.69 manufacturing workers will retire and 2.4 million jobs will be vacant
- 2021: U.S. manufacturing is expected to have 2.1 million unfilled jobs by 2030
Suppose multinational corporations can see the benefit of investing in American plants and workers rather than continuing their investments in low-cost countries. In that case, there is no reason we cannot reduce the skills gap and train the highly skilled workers needed by 2028. If they can't or won't, nothing will change, and in 2028 the Manufacturers Alliance for Productivity and Innovation (MAPI) will issue another survey showing the skills gap has worsened.
Michael Collins is the author of a new book, "Dismantling the American Dream, How Multinational Corporations Undermine American Prosperity." He can be reached at mpcmgt.net.