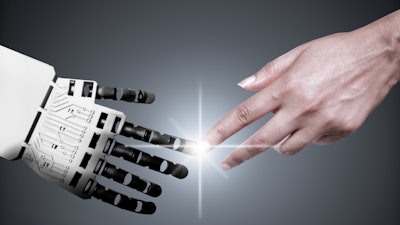
The United States is experiencing a resurgence of domestic manufacturing in response to the vulnerability exposed by supply chain disruptions, exacerbated by geopolitical tensions and the global pandemic. Reshoring initiatives aim to bolster supply chain resilience by reducing dependence on foreign production, but the success of these initiatives is contingent on the availability of a skilled manufacturing workforce.
This skills gap leads to vacancies in roles that are increasingly difficult to fill. A recent U.S. Chamber of Commerce report on labor shortages included this stunning statistic: even if every unemployed person with experience in the durable goods manufacturing industry were employed, the industry would fill only around 75% of the vacant jobs.
An acute skills gap threatens to undermine this domestic manufacturing resurgence, as a disconnect between the skills possessed by the existing workforce and those demanded by modern manufacturing technologies challenges organizations of all sizes. Bridging this gap is essential to revitalizing the industry and achieving supply chain resilience.
As companies struggle to fill vacant roles, employee training, including reskilling and upskilling, can play a significant role in mitigating staffing difficulties.
LNS Research, a leading research and advisory firm focused on empowering industrial organizations, released a recent report that elucidates the impacts that these issues have on manufacturers. A full 72% of industrial organizations are reporting that frontline workforce hiring, onboarding and retention issues have negatively impacted operational performance.
Addressing new problems requires new solutions. By leveraging the power of artificial intelligence (AI), organizations can incorporate more learning processes into the everyday work of frontline workers – essentially bridging the gap between knowing and doing.
The Solution
One way to achieve this is by operationalizing learning and bringing it closer to the factory floor using artificial intelligence (AI) and connected worker technology. Operationalizing learning means taking a more systematic approach to training and workforce development, rather than treating it as a one-time event.
Continuous skills development is paramount in modern manufacturing, where technology evolves rapidly. AI-based advanced analytics enable data-driven improvement of work processes, individual and team performance and learning, as well as overall operational performance. AI-driven training platforms can personalize learning experiences for each employee, identifying skill gaps and offering tailored training modules. This not only enhances the workforce's competency but also ensures that skills align with the evolving demands of the organization.
AI-powered solutions make learning more accessible, engaging and effective; and by integrating training and learning solutions into the everyday operations of the company, manufacturers can create a culture of continuous learning and improvement. With AI, organizations can incorporate more learning processes into the everyday workday of frontline workers – essentially bridging the gap between knowing and doing.
AI-based advanced analytics enables data-driven improvement of work processes, individual and team performance and learning and overall operational performance.
Additionally, AI-powered learning solutions can be customized to each worker’s skill level, making it easier for them to not only learn at their own pace, but also match their experience level. By harnessing the power of data, these tools can provide the right training to the right worker at the right time, delivering hands-on learning experiences based on their actual job performance and providing on-the-spot guidance and, when needed, immediate reskilling.
AI-powered solutions for frontline industrial workers can monitor worker performance in real-time, providing instant feedback to help workers improve to provide access to content to help resolve issues contemporaneously.
Investing in employees’ skills development not only ensures that organizations are achieving their operational goals, it also has numerous benefits for frontline workers that inure to their employers. Gallup’s latest Employee Engagement index highlights this fact, showing that engaged employees have higher wellbeing, better retention, lower absenteeism and higher productivity.
Workers who feel valued are less likely to leave, and providing those workers with the training and support they need on a daily basis saves organizations time and money by helping to retain their employees in the first place. The same Gallup survey revealed that only half of American workers understand what is expected of them, with a third of respondents affirming that they need more opportunities to learn and grow at work.
Organizations that offer robust training opportunities help their workers grow and move forward in the company, as employees are imbued with a sense of purpose and progress.
Upskilling and reskilling initiatives in manufacturing organizations extend well beyond their initial goals of improving retention and morale. They are powerful tools for elevating product quality, increasing productivity, enhancing efficiency and fostering adaptability in the face of technological advancements. These advantages not only benefit the bottom line but also position the organization as a forward-thinking and attractive employer in the competitive manufacturing landscape.
Supporting manufacturing workers is critical to the success of the resurgence of U.S. manufacturing and the overall resilience of the supply chain. The skills gap that plagues the industrial sector must be addressed, and AI is a powerful tool in this endeavor. By providing real-time skills training, offering on-the-job guidance, enhancing productivity and optimizing operational efficiency, AI empowers manufacturing workers to meet the evolving demands of their jobs.
As manufacturing continues to evolve, embracing AI technologies becomes not just an option but a necessity for the industry's future growth and competitiveness.