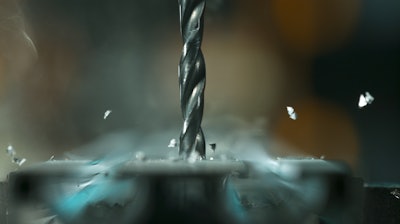
How do you approach cross-hole deburring at your facility? Today, manufacturers and machine shops have varied answers to this question. That’s because removing cross-hole burrs can be an arduous task, particularly on parts with complex shapes and diameters.
Some manufacturers hesitate to trust the process to an automated cross-hole deburring tool. Instead, they turn to inefficient and risky hand-deburring methods to get the job done. Others have implemented more sophisticated tools, but they’re not getting the results they need.
The benefits of getting the cross-hole deburring process successfully automated and out of your employees’ hands are too compelling to disregard. And it’s certainly worth another look if you’ve tried automating the process before with sub-optimal results. With the right tools, you can:
- Deftly handle cross-hole deburring without the headache.
- Realize consistently improved productivity and quality.
- Save on costs related to labor, scrap, tool replacement, employee health concerns and more.
- Optimize resource management by eliminating manual cross-hole deburring at your facility.
- Increase throughput and open your operations up to additional, more complex jobs.
What it comes down to is choosing the right tool for deburring cross-drilled holes in a reliable, repeatable way. That way, you won’t find yourself second-guessing the quality of your output or the value of your investment.
Tool Selection Makes All the Difference in Deburring Cross-Holes
The tools you choose can make or break the success of your cross-hole deburring process. For example, if you’ve been deburring cross-holes by hand, you’ve likely noticed a few clear downsides.
Some of the most significant drawbacks are quality concerns and the risk of damage. In cross-holes, the burrs are often difficult to reach and easy to miss – especially if you’re deburring small cross-holes. The part might get damaged or overworked in the process of reaching them, and parts may get dropped during handling. Other issues include:
- High overall cost of disposable tools.
- Inconsistent results from one part to another.
- Employee over-exertion, injury and dissatisfaction.
If you’ve implemented automated tools that don’t meet the right selection criteria, you might’ve hit some roadblocks as well:
- Inadequate tool performance: You’re finding the tool simply can’t work the complex shapes and diameters of the part you need to deburr. Some automated deburring tools are only designed to perform quality work on flat holes, and others have strict limitations when it comes to complex shapes, hole sizes and inner diameter ratios.
- Short tool life: The tool is wearing out faster than expected, leading to reduced consistency over time and more frequent replacement. For instance, brushes made with nylon will have shorter lifespans compared to those made with continuous ceramic fiber, a proprietary material from Xebec Deburring Technologies which won’t deform and has a long life.
- Incomplete burr removal: Burrs are still left on the part after automated deburring, necessitating post-process deburring. This could be considered a compromise when your tool can’t work the full complexity of a part, but it’s inefficient when compared to a process that applies a more appropriate tool.
Selection Criteria for Cross-Hole Deburring Tools
- The right cross-hole deburring tool for your application depends on several factors, including but not limited to:
- Whether the tool will approach through the cross-hole or the main bore. Different tools are required for each approach.
- The machine type you are working with. Different tools work best in different machines. Some can be used successfully in multiple machine types.
- The diameter and angle of the cross-hole. Some tools are only designed to deburr flat holes. Others can only successfully deburr cross-holes of certain sizes and complexities.
- Your anticipated production volume. With a higher production volume, you’ll want a tool that can perform continuously (even in lights-out situations) and guarantee quality results time after time without constant replacement.
- The ideal tool life for your operations. If a long tool life is important to you, the material of the tool will be critical. For instance, continuous ceramic fiber brushes and tools will perform better and last longer than many alternatives.
High-Performance CNC Tools for Removing Cross-Hole Burrs
Use your selection criteria to consider which of the following tools is right for your CNC application.
Tools to Approach through the Cross-Hole
If you’re approaching through the cross-hole and you’re looking for a tool that can deliver top performance, repeatability and a long tool life, even with complex shapes and diameters, consider the Xebec Back Burr Cutter and Deburring Tool Path. This spherical, carbide cutting tool will achieve ultimate reliability, consistency and tool-life by using a constantly shifting cutting edge. It also has the added benefit of a ready-made path, the Xebec Deburring Tool Path. The tool is capable of deburring:
- Flat holes
- Cross-holes with inner diameter ratios of 1:3 or less, 1:2 or less and 1:1
- Elliptical and off-center cross-holes
- Angled cross-holes
- Broken cross-holes
- Slotted holes
- Tapped/threaded holes
- Any shaped hole with a custom-made path
If your part has less complexity, you might consider the following tool options:
- ORBI tool: Can work flat holes, cross-holes with inner diameter ratios of 1:3 or less, cross-holes with inner diameter ratios of 1:2 or less and angled cross-holes. May be able to work slotted holes.
- Rotary blade tool: Can work flat holes and cross-holes with inner diameter ratios of 1:3 and 1:2 or less.
- Blade tool: Can work flat holes and may be able to work cross-holes with inner diameter ratios of 1:3 or less.
- Clothespin tool: Can work flat holes and may be able to work cross-holes with inner diameter ratios of 1:3 or less.
Tools to Approach through the Main Bore
If you’re approaching the part through the main bore, you’re looking at inner diameter tools. For the best performance and longest tool life, consider the Xebec Brush Cross-hole. When you use cross-hole deburring brushes like these with continuous ceramic fiber, you have an edge on reliability and consistency. The Xebec Brush Cross-hole can be used with a range of hole diameters because the brush expands due to centrifugal force. It is capable of deburring multiple cross-holes, irregular holes and counterbore flat surfaces.
If your part is less demanding and you have a very small production volume, you might consider blade tools with internal coolant pressure systems or flexible honing tools.
The Case to Re-Evaluate How You Deburr Cross-Holes
Area Tool, a manufacturer of high-precision, tight-tolerance parts for many companies in the medical hardware, aerospace and telecommunications industries, has realized significant returns on their investment in Xebec ceramic fiber brushes. In one instance, they were working with CPM 10V, an extremely hard material, using carbide files to manually remove the burrs. Now they run a Xebec brush over the part while it’s still in the CNC for much easier deburring. After the machining is complete, the hand-deburring process is unneeded and they get consistently high quality results. Their ability to run machines “unattended” has improved productivity dramatically.
Considering the complexity of most cross-hole deburring projects, it makes sense that each manufacturer has their own process to complete the jobs. However, when you choose to be more intentional with your tool selection and deburring method, you can remove these complex burrs and major production headaches – and improve productivity and profits in the process.
About the Author
Matt Seibert is an industrial engineer for Xebec Deburring Technologies, manufacturers of automated deburring and surface finishing tools. He utilizes his engineering and manufacturing background to help identify and offer deburring and surface finishing solutions for machined parts and can be reached at [email protected].