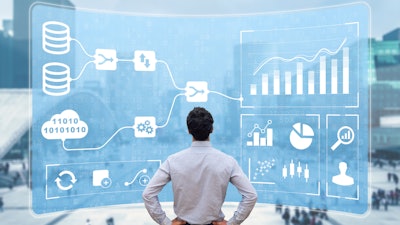
In the race for technological advancement, the manufacturing sector has faced some notorious challenges in keeping pace. Whether due to monetary constraints, implementation challenges, workforce resistance or other hurdles, the industry tends to struggle with technological adoption.
This delay not only leads to inefficient practices, but also results in dysfunctional and ineffective data management, which has far-reaching consequences. Neglecting to harness the power of modern technology most likely means manufacturers miss out on the benefits of accurate, real-time data, which is essential for optimizing processes and driving growth.
Data is the backbone of any modern manufacturing process. It informs decisions, streamlines workflows, and identifies inefficiencies. Yet, many manufacturers are not tapping into this invaluable resource. When data collection is inconsistent or entirely absent, the potential for optimization and revenue generation diminishes significantly.
In fact, poor data quality costs companies an average of $12.9 million every year. For Unity Software, a video game software development company, the cost was even higher. The organization previously reported a loss of $110 million in revenue and $5 billion in its market cap, citing the ingestion of bad data from a large customer.
Inefficient data practices create an environment where reporting becomes a massive undertaking, often involving manual pulling and compiling of data from disparate sources. This not only wastes time, but also sets the stage for errors and missed opportunities. A centralized tool that consolidates data can go a long way toward remedying this quagmire, offering manufacturers a comprehensive and integrated view of their operations from start to finish.
Leveraging Quality Data
Quality data isn't just about numbers on a spreadsheet — it's about actionable insights that drive business performance. Accurate data provides a consistent and unified view to significantly boost sustainability. When waste and inefficiencies throughout the production process are reduced, organizations can operate more efficiently, and deliver superior customer service. Some of the other key benefits of having functional and holistic data include:
- Improved Efficiency. With accurate data, manufacturers can streamline their operations, reducing downtime and waste. This leads to faster production cycles and a more agile response to market demands. According to a McKinsey & Company case study, users can spend between 30-40 percent of their time searching for data if a clear inventory of data is not available or accessible.
- Cost Savings. Data-driven decision-making can significantly cut costs. For example, optimizing resource allocation and reducing waste can lead to substantial financial savings. Companies that improve their architecture to move away from a fragmented environment can typically save between 5-10 percent in the first six months and between 10-30 percent over the next three years.
- Enhanced Sustainability. Sustainability is more than just a buzzword in the current landscape, and efficient data management can help manufacturers minimize their environmental footprint. Optimized production processes help companies reduce waste and improve resource usage.
- Demand Prediction. Staying agile in response to market fluctuations is crucial. Leveraging impactful data enables manufacturers to determine the source of overruns, downtime, lost productivity, and excess inventory — and quickly adjust to meet market trends.
To truly reap the benefits of quality data, manufacturers must not only invest in the right software, but also ensure its proper implementation. Selecting a unified software solution that offers full visibility into operations is crucial. It should seamlessly integrate with current systems and be user-friendly for employees at all levels.
Implementing new technology comes with its own set of challenges. From training staff to integrating with current workflows, every step must be handled meticulously. Manufacturers can simplify the process by gaining active support from top leadership, cleaning and optimizing their data and processes, and planning for future growth and ROI drivers. Additionally, they should avoid distractions and focus on executing the plan, rather than getting bogged down in non-essential features.
The manufacturing sector can no longer afford to lag behind in technology adoption. In today's digital age, inefficient practices and dysfunctional data are significant barriers to success. By investing in a centralized data management tool and ensuring its proper implementation, manufacturers, business executives, and supply chain leaders looking to stay ahead of the curve can significantly enhance performance, cost efficiency, and sustainability.
It’s time to leverage the power of quality data and modern technology to drive organizational momentum.
Jason Chester is the VP of Strategic Accounts at Advantive.