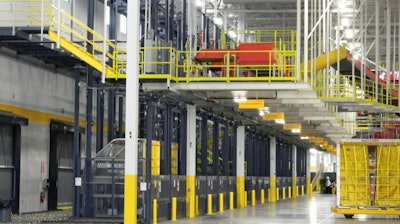
Multilevel automated warehouses raise the game for materials-handling logistics, adding sheer scale and compounding complexity for workflows, infrastructure and integration.
In this blog, we break down seven of the biggest challenges that engineers and project managers face when rolling out multilevel warehouse automation solutions. We’ll also address how the powerful, optimized lifting capabilities offered by vertical reciprocating conveyors can help solve each of these challenges.
Full Stack: Challenges of Multilevel Automation
Multilevel warehouses are becoming more common as distributors look to increase speed and build scale closer to target markets in urban areas. For all the advantages, though, moving products between floors in a multi-story facility is always a serious challenge. Here’s why:
1. Limited Space
The goal of Multilevel facilities is to make the most of every available square foot of space. Material handling equipment needs to provide maximum functionality within a minimum footprint to ensure there is sufficient space for:
- Human and Automated Vehicle Pathways
- Dock Space
- Meeting Safety & Compliance Regulations
- Expansion
2. Multiple Floor Levels
Transporting materials to multiple floor levels adds complexity to automated systems. Selecting the right equipment for multi-level materials movement provides flexibility in loading/unloading options (manual, diversion, dumper) and also ensures that the equipment can accommodate the vertical travel speed and load capacities needed to transport materials safely between floor levels.
3. Diverse Products
Today’s multi-faceted warehouse must be able to move a variety of products and material loads safely and efficiently. Variability in the size, weight, shape and fragility of the products being moved can affect the equipment you select. Automated systems must be able to adapt to ever-changing requirements.
4. Variable Load and Travel Patterns
Tight corners, repurposed spaces and multiple floor levels often equate to complicated material handling maneuvers when moving goods between levels. Horizontal conveyors might need to make sharp turns and lifted loads might need to enter in one direction and exit in another.
5. Complex Workflows
From inbound to outbound, receiving to storage, storage to the last 100 feet of the warehouse (SLAM), the flow of products through your facility needs to be precisely coordinated. Adding vertical space adds to the already challenging warehouse-wide planning needed to prevent bottlenecks, disruptions and downtime.
6. Customizable Equipment
All this added complexity makes it difficult to find off-the-shelf automation equipment. Larger warehouses often require equipment purpose-built to perform each task, typically outfitted with customized integrations and connecting equipment.
7. Safety
Automation at height also brings increased safety challenges, including the need to prevent items from falling from upper floors or platforms and measures to prevent workers from being trapped or injured by lifting equipment.
VRCs: Multiple Levels, Multiple Solutions
Vertical reciprocating conveyors (VRCs) offer a robust, versatile industrial lifting solution designed specifically for the challenges of moving loads between levels in crowded facilities.Designed to move goods, not people, VRCs do not require the same maintenance or regulatory burden as an elevator, but provide reliable lifting capabilities customized to your needs. VRCs are built around a robust core lifting technology powered by either hydraulic or mechanical systems and are particularly well suited to handling the complex challenges of multilevel facilities. Here’s how:
1. Room to Move
When PFlow introduced VRCs in the 1970s, we designed them with versatility in mind. Our material lifts can fit into places where forklifts, inclined conveyors or scissor lifts simply won’t work.VRCs can be incorporated into new construction or existing facilities, placed next to mezzanines or balconies, installed through floors, in existing elevator shafts and even placed on the outside of a facility to accommodate safe and efficient material lifting.
2. Taking It Higher
Forklifts, scissor lifts and inclined conveyors face serious limitations when it comes to elevating heavy loads. With VRCs, the sky’s the limit. Our material lifts raise loads of almost any weight by just a few inches to over 200 feet and our heavy-grade steel structures can be built to handle loads of up to 100,000 pounds.
3. Tough but Gentle
VRCs have the strength to lift the heaviest loads, even those material loads that require special handling due to their fragility or sensitivity. PFlow’s mechanical material lifts feature heavy-duty roller chains featuring chain over sprocket design along with a gear reducer assembly that ensures smooth lifting and lowering travel and bounce-free stops.
4. Turn for the Better
Moving materials between floors involves complex handling challenges. PFlow’s straddle, cantilever and four-post VRC designs enable loads to be moved onto and off the lift in almost any direction.
5. End-to-End Synchronization
Warehouse automation means ensuring every load makes it from receiving to storage and from storage to shipping with minimal disruption. PFlow conveyors automate lifting with reliable, repeatable functionality that can be synchronized or coordinated with other equipment like horizontal conveyors or pick modules, making them ideal for complex multi-floor workflows.
6. Made to Measure
No two material handling applications are the same, so why choose an off-the-shelf solution that doesn’t meet all of your needs? Fortunately, PFlow VRCs are designed to meet your specific needs to provide unmatched versatility and return on investment.We work with you to understand your needs and build customized VRCs from the ground up to meet them. Talk to us about your load requirements and integration challenges. With almost 50 years of experience designing and manufacturing VRCs, we can develop a solution to your material handling challenges.
7. Do No Harm
VRCs are a safe, efficient and reliable material lifting solution. Incorporating VRCs into your multi-level automated warehouse can reduce or remove manual lifting of materials by forklift or other more manual means. In addition, VRC lifting solutions also include multiple layers of safety features like gates, enclosures, mezzanine backstops and interlocks to protect both workers and materials from harm and damage.
Raise Your Lifting Game
VRCs are great for helping to solve the challenges inherent in automating and optimizing operations at multiple levels, but they also come with other built-in benefits, including:
- Increased efficiency: Lifting more cargo and doing it faster with less handling equals more efficiency, no matter what you’re moving.
- Reduced Costs: VRCs reduce your dependence on manual handling and forklift operations, helping you save money on fuel, maintenance and labor costs.
- Reliability: Quality VRCs are built from quality materials and made to last, delivering performance you can trust cycle after cycle, year after year
- Integration: By making lifting reliable, repeatable and controllable, VRCs provide a platform for integration, both with connecting equipment and across your facility.