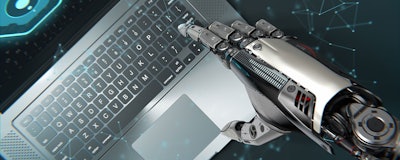

Enterprise adoption of automation is on a steep upward climb across industries. According to Gartner’s 2019 CIO survey, organizational use of these technologies has increased by more than 270 percent over the past four years, with no sign of slowing down.
Digital transformation has the potential to drive enormous value across industries—and the manufacturing sector is no exception. But as a recent study by Nintex revealed, manufacturing organizations face several industry-specific issues that are slowing the momentum of digital progress. By strategically addressing these problems, manufacturers can begin to realize the benefits automation offers.
The Hurdles to Realizing Transformation Value
According to Nintex’s 2018 Enterprise Digitization Progress Report, there are two roadblocks actively preventing manufacturers from realizing the value of digital transformation: unprepared IT departments and a lack of top-down communication.
The first step to a successful enterprise digital transformation strategy is having the internal capabilities to carry it out—specifically, a prepared and proactive IT department. Right now, that doesn't exist in the manufacturing sector.
Nintex’s digitization report—which surveyed 650 line-of-business employees and 450 enterprise decisionmakers—found that among manufacturing employees, only 29 percent felt their IT department was extremely prepared to handle the needs of digital transformation. By comparison, almost half of employees in the financial sector were very confident in their IT teams’ digital preparedness.
What accounts for manufacturing workers’ low level of confidence in their IT departments? Part of it could be due to a sense of disconnect from transformation efforts and from the IT department in general. As Nintex’s study found, the notably majority of employees—77 percent—want to be involved in transformation efforts. When they don’t feel like they are, they begin to view digital transformation and automation not as resources that will augment their work, but instead as active threats to their jobs.
Inadequate training of frontline workers is a separate (though related) issue that’s impeding manufacturers from seeing a return on their digital investment. Of the enterprise decisionmakers surveyed by Nintex, roughly one-third pointed to insufficient training of line-of-business workers on new technologies as one of the top challenges standing in the way of digital progress. And indeed, the survey found that fewer than half of frontline employees are even familiar with the concept of digital transformation—a number that highlights an awareness gap between the c-suite and the frontline. Bridging this gap is critical to digital progress.
The Value of Digital Transformation for Manufacturing
For manufacturing leaders, the first step to realizing the benefits of digital transformation is to address the internal issues holding it back. That means making a more concerted effort not only to promote frontline awareness about digital transformation planning, but to proactively include these workers in the process. And on the IT side, departmental leadership should consider an approach to IT that prioritizes cross-departmental engagement over the traditionally siloed role into which many IT workers are often boxed.
Once manufacturing leaders have strategically addressed issues surrounding poor top-down communication and inadequate training, they can begin to experience the far-reaching benefits of a considered transformation strategy:
- Increased productivity: By strategically implementing automation technology, manufacturers can more effectively manage production and better delegate tasks according to priority order.
Consider HillPhoenix. A manufacturer of large refrigeration units, the company needed a solution to streamline its daily inspection efforts. Before digitizing, the inspection process was completely paper-based—employees used handwritten notes to record quality findings. This manual process increased the risk of errors, wasted inspection time with paper forms, limited tracking records and created more cumbersome processes.
After deploying workflow automation solutions, however, the company transitioned its inspection process from a system based primarily on memory and handwritten notes to one supported by a digital platform. The implementation of this platform not only decreased production-line errors, but significantly improved productivity.
- New levels of innovation: By driving greater productivity and alleviating the burden of lower-level tasks on the human workforce, automated solutions lay the foundation for more innovation.
Companies like New Belgium beer illustrate how automation can drive greater innovation. The company traditionally relied on Outlook and SharePoint to track and manage tasks related to product launches. However, this system created communication gaps and scheduling delays, which set it behind as new competitors were being introduced daily.
The company needed a better way to oversee task management, improve communication among team members, and shorten launch timelines. By implementing no-code workflows to schedule and coordinate tasks, the company was able to significantly expedite lower-level processes and therefore channel more time and resource into innovation.
By better prioritizing top-down and cross-departmental communication at the outset of a digital transformation plan, manufacturing leaders can lay the groundwork for successful long-term strategy. And once they do that, they can make new leaps in productivity and innovation.
Ryan Duguid is chief evangelist at Nintex.