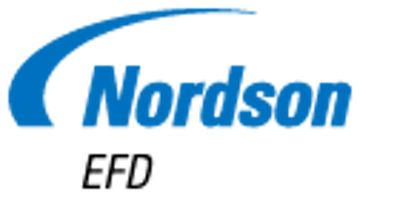
1
Problem
Many solder users have preconceived notions and worries
involving reflow profiling guidelines. Years of reading
profiling recommendations in industry publications has
made it clear that if the solder supplier gives them a tidy
drawing on a piece of paper with times and temperatures
that it will magically solve all their reflow problems. This is
often an incorrect assumption.
Let us begin the discussion with a question. Do you
believe you can get a good solder joint with a soldering
iron: ‘yes’ or ‘no’? (Figure 1).
The temperature of a soldering iron does not resemble the
temperature required for a solder joint to form. The iron
is at a much higher temperature than required for reflow
of the solder joint. This large difference in temperature is
used to force rapid heating. Peak temperature and time
above alloy liquidus are in the hands of the operator and
the heating capability of the soldering iron.
Figure 1
If your product goes in one end of an oven and comes
out of the other end with no damage or defects in your
product, can you tell what the reflow profile looks like?
Does it matter what happened in the middle? Your goal in
making a reflow profile is to ensure you don’t have defects
like flux and alloy spatter, tombstoned components,
overheated substrates and components, cracked vias, cold
solder joints and the like; nothing more and nothing less.
Maybe you don’t use convection ovens. How does a
reflow profile guide apply now? In most cases they do not
apply except for the most general of concepts such as
peak reflow temperature.
When it comes to reflow, it should be specific to what
you are trying to accomplish with your product, not
just duplicate the reflow profile on the solder supplier’s
profiling guide. If the suggested profile is not possible or
not desirable with your product, you should contact your
solder supplier to confirm it is intended to perform as
needed with the heat cycle that best suits your product.
Recommended profiles are almost always written for use
with convection ovens and circuit boards. They are also
designed to meet customer expectations of what they
should look like. In truth, for circuit boards, there is usually a
fairly wide window of opportunity for success. Your heating
process needs to be designed to achieve the highest yield
with your products and your heating equipment.
A Brief History of Circuit Board Reflow
Much of today’s reflow profiling philosophy evolved to
compensate for the technology available when surface
mount assembly was young. That technology was
primarily infrared reflow ovens, vapor phase systems,
and high mass convection reflow ovens. What follows
is a brief and simplified history that explains why the
electronics industry has mostly moved away from the
early heating options.
Infrared energy is very inconsistently absorbed on a
populated circuit board (Figure 2B). Due to uneven
heating, the person in charge of profiles would heat the
board up to a safe temperature below the solder reflow
temperature, then have a “soak zone” to let the board
equalize in temperature through conduction.
Convection IR
Figure 2A Figure 2B
The colder shadowed and reflective spots are allowed
to catch up with other spots on the board that were
significantly hotter due to color and reflectivity differences.
Temperature differentials from point to point of more
First Principles of Solder Reflow
John Vivari, Nordson EFD
2
than 40° C were not uncommon. It takes some time for
thermal energy to spread through conduction and achieve
point-to-point temperature differential of less than 5° C,
hence the aforementioned “soak zone.” Next the heat is
turned up to increase temperature to the next plateau until
temperature equalizes at the desired peak. The philosophy
behind “Ramp Soak Spike” reflow profiling grew because
of infrared reflow and the need to get good results despite
the limitations of that heating technology (Figure 3).
Figure 3
Many people choose to use the “Ramp Soak Spike”
process with low mass, quick-response convection ovens
that do not necessitate that kind of heating profile. While
such a profile usually works, it is rarely optimal for today’s
solder paste chemistry. In general, a solder paste will work
best, wetting wise, if you take less time to achieve reflow.
Vapor phase heating does not promote the concept of a
profile. Immersing a product into a boiling liquid causes
very rapid temperature increase. Vapor phase is good for
limiting peak temperature and ensuring all the solder melts
at the boiling temperature of the fluid used. On the down
side, the fluids are expensive and the rapid ramp can
cause component tombstoning and other thermal shock-
related problems.
High-mass convection ovens had to be profiled based on
the long thermal recovery times inherent in the system.
Attempts to use such ovens for short reflow profiles (without
a soak time) would often overheat single boards, work well
with a limited number of boards added at regular intervals,
and fail to reflow solder if the ovens were fully loaded. With
these ovens, longer profiles made for better consistency.
With the advent of low mass convection reflow ovens,
most limitations on reflow heating process were taken
away. Full or empty, black or green, the oven treats every
product the same. Only the thermal mass of the parts
plays a significant role in how long it takes to heat an entire
product to the desired temperature.
With a shorter profile you minimize consumption of the
oxide, reducing flux chemistry from pumping a lot of hot
air onto the flux and the surfaces that it cleans. You get
better wetting with a shorter profile because there is more
activity in the flux to get the job done, and the flux remains
fluid enough to flow well. A typical example of a shorter
profile is the “Ramp to Peak” profile with a fairly constant
ramp (Figure 4).
Figure 4
Keys to Success
There are four steps to success no matter what kind
of product you have or what kind of reflow equipment
you use. Some may be mere formalities based on the
simplicity of your product.
Step one: Find out which components, if any, are
temperature or thermal shock sensitive. Most parts aren’t
sensitive at conventional reflow soldering temperatures.
If you do have sensitive parts, they will limit how fast,
how hot, and where you can heat your product. Some
products require localized heating. It may be necessary to
investigate alternative heating methods.
Step two: Find out if you have any relatively large, heavy,
or otherwise difficult-to-heat parts. Such parts may limit to
how fast your product may be heated, with the equipment
in use, without damage. As with temperature sensitive
parts, it may be necessary to investigate alternative
heating methods and secondary reflow operations.
Step three: Match a solder product to the components
and heating process you intend to use. Despite the
seeming simplicity of this step, keep in mind that
there are a bewildering variety of solder pastes, solder
wire styles, and fluxes supplied in dozens of solder
alloys. Each has a specific purpose as someone is
using it to satisfy a particular need. Factors such as
the equipment available, application method, operator
training requirements, solder joint consistency, and flux
performance in the heating and cleaning processes will
be key to the decision-making process.
Step four: Test and tune your reflow process for optimal
yield. Easier said than done, this step can push the
process development cycle back to Steps 1, 2, or 3 due to
unacceptable results. Here is where reflow profiling can in
fact become critical.
3
Reflow Process Development, Condensed
If you are not heating with an oven, the heating cycle
is unlikely to look like a published profile. That’s fine. It
doesn’t have to. Your goal is to get the right amount of
heat to the right location within your targeted cycle time.
Success is measured in first pass yield and throughput,
not degrees C per second and time above liquidus.
Temperature ramp rate and time above solder alloy
liquidus are only important if they can damage your
product. It usually only takes a second or three for liquid
solder to finish moving and wetting to the available
surfaces after it reaches reflow temperature. If you are
heating slowly, it may take longer. The hotter the solder
gets, the faster the solder wets.
Does the time above liquidus matter? Only to the extent
that all the solder needs to reflow and finish wetting. The
truth of the matter is that the solder joint is formed and the
liquid solder alloy stops moving after about 1.5 seconds.
Time beyond that spent above liquidus is not generating
any benefit with regard to joint quality. Extra time thickens
the intermetallic layer, which is more brittle than the bulk
solder joint, and increases substrate scavenging.
Intermetallic compounds form when two unlike metals
diffuse into each other. In soldering, this is tin into copper,
nickel, and other solderable materials. During laser reflow
of solder paste, the entire reflow heating cycle can be
completed in under a second with full wetting and a
textbook-perfect fillet. Excessively thick intermetallic
layers can contribute to brittle fracture of solder joints.
Scavenging is most often of concern with plated parts and
printed thin films. In extreme cases the entire solderable
surface can be dissolved. Again, more time above liquidus
is not a benefit.
The ideal heating cycle is no longer than the time it takes to
make sure every joint has reflowed and wet out completely.
For those that do use reflow ovens, including circuit
board assemblers, all the same rules apply. For circuit
boards, Nordson EFD recommends you begin your
heating experiments with a heating rate of somewhere
around 1° C per second from room temperature to peak.
If the oven available produces a stepped profile instead
of a straight line profile, that is fine. If you need to slow
things down to get a lower temperature differential
from point to point on your product, go right ahead.
Gradual, even heating results in fairly uniform product
temperatures. It is a process that can be reproduced on
a very wide variety of ovens.
Preventable Reflow Problems with Circuit
Boards
There are techniques you can use to prevent defects
through good profiling. The temperature and time ranges
detailed in profiling guides are usually chosen to give a
wide enough window to apply such techniques.
At the beginning of a heating cycle the single largest issue
is explosive vaporization of low boiling point materials that
are either part of the flux or have been absorbed during
use. Alcohol and other solvents and absorbed moisture
can explode if heated too fast. Solder and flux spatter are
the most common indicators that you have a problem that
deserves attention. If you need to, slow your heating rate
up to 130° C to dry the paste more gradually so it does not
explode.
Beyond the 130° C point, where water and most low
boiling point materials will have finished evaporating, you
have the temperature range up to alloy solidus. At these
temperatures, the activators in the flux fulfill their function,
cleaning the solder and substrate of oxides. Spend too
long here and the flux activity can be mostly or completely
consumed, resulting in poor wetting and what appears
to be unreflowed solder despite achieving a peak well
above alloy liquidus. Longer heating processes can be
accommodated with higher activity flux formulations. As a
goal, do not spend any more time between 130° C and the
alloy solidus than is required for acceptable point-to-point
temperature differential on your product.
The next critical point of the heating cycle is around the
alloy solidus temperature. Once you get to just below
the liquid point, some heating processes need to slow
down. The most common reason for care during alloy
liquefaction is to prevent tombstoning (Figure 5).
Figure 5
Tombstoning occurs when a difference in temperature
between the two pads allows the paste on one pad to
reflow before the other. The difference in surface tension
between the two pads produces torque which lifts the
part. By slowing the ramp as the metal liquefies, you
will minimize the chance of generating a tombstone.
Thinking of it a different way, instead of soaking below
the liquefaction temperature of the alloy, utilize a slower
ramp rate, something under 1° C per second, as you go
through that liquefaction zone. Nordson EFD recommends
controlling ramp from about 5° C below solidus to 5° C
above liquidus of the alloy. As chip components get
smaller and smaller, your risk for tombstoning increases.
Time spent above liquidus and peak temperature
should be based on process robustness. Typical
4
recommendations of 15 to 40° C above liquidus are based
on the fact that solder alloy wets better the hotter it gets.
Temperatures in this range will ensure optimal wetting.
Solder joints form at just a few degrees above liquidus
but wetting will not look typical and may not meet
reliability requirements.
These recommendations are also based on common
processing limitation for circuit board materials. If your
circuit board material is not as temperature-sensitive,
getting hotter may not have a down side.
Time spent above liquidus is a function of the heating
and cooling capabilities of your oven and the goal of
reflowing the unmeasured cold spot on your product,
every time. By adding five or ten seconds to reflow time,
the likelihood of a cold solder joint can be eliminated.
Exactly how long this time is for your product depends
on the specific thermal constraints.
Conclusion
Some people use lasers to reflow solder in less than a
second. Others have heating times of 20 minutes or more.
Most fall in between these two extremes. All you have
to do is match the heating process and solder product
to your soldering need. Understand the limitations and
opportunities your components, equipment and solder
material present and take full advantage of them.
Written by:
John Vivari
Nordson EFD
40 Catamore Boulevard
East Providence, RI 02914
[email protected]
Request samples
If you’d like to test EFD solder paste or thermal compounds,
please request samples. Simply go to
www.nordsonefd.com/SolderSampleRequest.
Request More Information
Nordson EFD’s worldwide network of experienced solder
paste specialists are available to discuss your dispensing
project and recommend a system that meets your
technical requirements and budget.
Call or email us for a consultation.
800-556-3484
[email protected]
www.nordsonefd.com/recommendations
Connect with us
For Nordson EFD sales and service in over
40 countries, contact Nordson EFD or go to
www.nordsonefd.com.
Global
East Providence, RI USA
800-556-3484; +1-401-431-7000
[email protected]
Europe
Dunstable, Bedfordshire, UK
0800 585733; +44 (0) 1582 666334
[email protected]
Asia
China: +86 (21) 3866 9006; [email protected]
India: +91 80 4021 3600; [email protected]
Japan: +81 03 5762 2760; [email protected]
Korea: +82-31-736-8321; [email protected]
SEAsia: +65 6796 9522; [email protected]
©2018 Nordson Corporation v121218