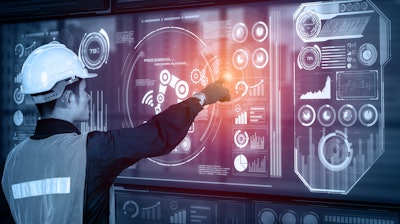
The automation industry has experienced astronomical growth in the past few years. In fact, according to a recent Statista report, it is expected to generate $214 billion this year alone. Of that, the process automation segment is estimated to exceed $83 billion. Automation is vital to most modern industries, including industrial software development, which is expected to be worth $43 billion.
In short, automation is big business.
It is no secret that the manufacturing industry is the most automated sector worldwide. Not only does it rely on robotics and AI for production, it also generates nearly two petabytes of new data each year. And while manufacturing is one of the most automated industries in terms of production, most companies still rely on manual solutions such as Excel spreadsheets and whiteboards not designed to support collaboration. The result is often lengthy, confusing planning cycles based on outdated, inaccurate data. Even the slightest changes can create issues that make this approach impractical for long-term success.
Excel alone cannot provide real-time insights. Automating processes such as sales and operational planning (S&OP), budgeting, and forecasting can assist in achieving that end. For those companies still relying on manual planning and budgeting methods, the time has come for an upgrade in the Office of the CFO. While automation has long since been applied to the area of production, simple solutions are available today for automating critical data management processes, too.
Because innovation inevitably leads to acceleration, the ability to quickly analyze large data sets in order to transform them into usable insights is a challenge nearly all manufacturing organizations face. Labor-intensive work processes to prepare and manage budgets need to be replaced with automated ones to avoid confusion in long budgeting cycles. With the rapid increase in data volume, manufacturing companies are rapidly shifting from on-premise to virtual and cloud computing environments.
Maturity Levels for Digital Transformation
Digital transformation relies on the maturity level of an organization that provides the setting for modern, continuous capabilities toward process improvement and optimization. In terms of financial planning processes, there are three maturity levels:
- Manual-based planning processes.
- A hybrid of manual and automated processes for tactical improvement through digitalization.
- A strategic enhancement of planning processes through full-blown digital transformation.
While it is clear that manual processes are a part of yesteryear, technical improvements through digitalization itself do not add sufficient business value. In order for true digital transformation to occur, planning processes must be based on collaboration, business logic, and data integration. The good news is there are already existing solutions to ease organizations through their transformation.
Cases in Point
Magna is a leading global automotive supplier with 348 manufacturing facilities and 91 product development, engineering, and sales centers located in 28 countries. Headquartered in Ontario, Canada, the manufacturer has 31 factories and 10 R&D centers in China. Overwhelmed by the deluge of data, Magna recognized the need to embark on the journey toward digital transformation. Executives realized a new Enterprise Performance Management solution was required to meet the daily demands for accurate, real-time insights.
The finance team upgraded its planning solution, which allowed them to simplify the planning process, formulate rolling forecasts combined with strategic development, ensure faster user implementation, and obtain more timely and relevant data analysis. The team now has access to a 360-degree view of operations with the ability to compare plans, forecasts, and actuals.
Founded in 1946, the Swiss-based company Heiniger AG is a leading manufacturer of high-quality animal shearing clippers for livestock and pets. The family business has subsidiaries in Australia and New Zealand with qualified sales partners in over 50 countries worldwide.
Increased analysis requirements and a change of their ERP system made the acquisition of a new solution for reporting and planning necessary. Heiniger needed flexible options for analysis that easily integrated with their existing systems and selected a new solution to meet their planning needs. Ease of use, implementation, top notch flexibility, and data integration were all key factors in their decision.
As a result, Heiniger simplified its planning across the entire enterprise. The team estimates a time savings of over two hours per week through its digital transformation. Various departments can now perform self-service analysis while the sales team can easily access customer data via the mobile solution. Planning rounds can now be carried out until the final plan values are determined, which are then seamlessly fed back from the new solution into their ERP system.
The manufacturing industry is tasked with aligning its automation efforts beyond the production line to improve efficiency and effectiveness. Digital transformation is clearly the path forward for better business performance.
Dr. Liran Edelist is the president of Jedox.