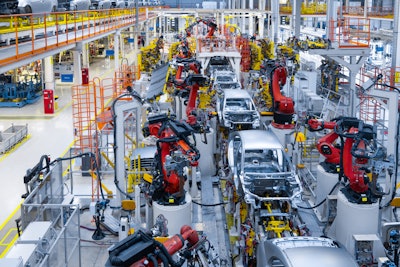
Automotive manufacturing is transforming as technology innovation, shifting business models and changing driver behaviors impact the way cars are designed and built. Technology innovation is increasing the complexity of car designs, while rising adoption of ride sharing services are pushing the limits on product reliability and “zero failure” safety and security, as cars must withstand multiple drivers and longer driving times.
These changes present unique challenges to electronic manufacturing services (EMS) providers that serve tier one suppliers and automotive OEMs. In order to successfully navigate the evolving ecosystem, EMS providers must address a number of new trends and requirements in their manufacturing operations, including:
Increasing Electronic Content
New technology for advanced driver assistance systems (ADAS), vehicle communications and infotainment applications are filling up the cockpit of cars, while sensors and other electronics are increasing under the hood for driver assistance, safety and autonomous capabilities. New designs are also enabling further electrification of the powertrain for environmentally friendly electric car models.
IHS Markit indicates that the automotive semiconductor market will increase from $37.4B in 2018 to $58.5B in 2023, at a compound annual growth rate (CAGR) of 7.7 percent, while IC Insights forecasts sales of automotive-related electronic systems to increase from $152B in 2018 to $162B in 2019. As cars turn into IOT-connected supercomputers, EMS providers must adopt more advanced quality methods, systems and skill sets to keep pace.
Electronic Component Shortages
Steady and rising demand for more electronics in vehicles is also contributing to a shortage of components that is likely to continue into 2020 and beyond. This makes it challenging to maintain linearity of production and requires a great deal of flexibility as products are being built. As a result, both IT and quality management systems need to be developed to deliver high levels of flexibility while ensuring regulatory compliance.
Growing Safety Requirements and Regulatory Scrutiny
Once an automotive product leaves the factory, the opportunity for failure must be virtually eliminated. During production, EMS providers need to use advanced processes that comply with regulations and provide process controls for pristine execution with zero defect performance. This requires a robust quality management system (QMS) and compliance with IATF 16949, the most widely used international standard for automotive QMS.
Increasingly, manufacturers must also become compliant with ISO 26262, an international standard for the functional safety of electrical and electronic systems in production cars. Not only must manufacturers adopt this standard while also complying with IATF quality standards, they also have a wider responsibility to ensure that all of the component suppliers they work with can support the product’s automotive safety integrity levels.
Unique Customer Specifications
Contract manufacturers must also comply with customer-specific requirements. Their customers and the automotive OEMs have very specific, unique quality management specifications, in addition to industry standards. Contract manufacturers must be in full compliance with these requirements, along with fully ensuring zero defect performance and adequate process control in their factories.
These requirements also lengthen the amount of time it takes to set up, validate and certify a new automotive production line. Overall, full compliance to IATF certification for a new line can take up to a year and a half, including all of the validations and closure on all Production Part Approval Process (PPAP) deliverables from the automotive supplier and the automotive OEM. In many cases, it also requires modification to the factory floor plan and new equipment acquisition – not a simple or inexpensive task.
Best Practices
In order to successfully address these complex requirements from multiple parties, EMS providers can use a number of proven approaches to help them increase their competitive edge:
- Design an Advanced Product Quality Planning (APQP) plan. Taking time up front to conduct full planning that considers customer requirements, all the way through to full production, ultimately saves time and helps EMS providers steer clear of mistakes down the road. An APQP plan is a phased gate process that includes risk analysis at every step, ensuring that production doesn’t move forward to the next chronological action unless all previous steps have been completed. When looking at processes, tooling and systems design, it’s also a very effective method for removing operator dependency at key points in production.
- Implement a global, vertically integrated QMS. Operating under a single global QMS not only ensures compliance to standards for global customers but also makes it more efficient when adding new sites to the automotive manufacturing footprint. In addition, vertically integrating a QMS with automotive suppliers at regional sites allows the supply chain to digitally connect and collaborate across locations. When supporting a common customer in Europe, Mexico and China, digital collaboration means that all parties can share data, look at in-process results from one site to another, learn from past experiences and avoid repeating mistakes. Audit results and customer feedback from various visits can also be used to proactively drive improvements at all sites.
- Leverage Industry 4.0 technology for real time monitoring and analysis. Modern, cloud-based MES platforms, combined with robotic automation and machine to machine (M2M) communications, enable real-time data monitoring and analysis capabilities that add more agility to automotive production. Tapping real-time data generated from activities on the factory floor, quality and factory staff can perform root cause analysis and make process adjustments very quickly. At Sanmina, we use our cloud-based MES platform to connect different departments to one central source of information during the APQP process. This facilitates more proactive communication and enables real time review of production status so that production can move more efficiently from one gate to another. Based on its success, we are looking to deploy this approach at other locations. A cloud-based MES platform also manages traceability – not only for tracking products and their components but also to track process points, tools, templates and operator activity involved in the build process. This streamlines operations, while also storing a complete history of data to ensure compliance with regulatory bodies.
- Cultivate best practices across teams and sites. It’s critical that everyone is consistent in understanding and complying with customer requirements, especially for global customers that have automotive products produced at several different locations and regions. It’s also important to collaborate and find solutions to common problems that are proactively shared and implemented across all sites.
As the automotive industry continues to change rapidly, it’s critical that EMS providers act as a seamless extension of their automotive customers and provide flawless execution. Applying best-in-class quality methods and Industry 4.0 technology facilitates faster, real time communication and ensures consistent global operations that translate into improved regulatory compliance. Having a centralized knowledge base also provides the flexibility to correctly and consistently adapt global operations based on changing external circumstances. Delivering high-quality, zero defect products is vital not only from a quality and safety perspective for automotive OEMs, but also translates into a positive driver experience, the ultimate benchmark for best-in-class customer satisfaction.