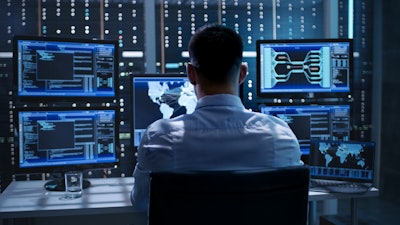
The proliferation of Industry 4.0 initiatives has combined with lean manufacturing strategies to make the availability of data, plant connectivity and IT security increasingly important. Throw in some e-commerce and the demands being placed on industrial IT departments have become exponentially more significant.
As these needs continue to grow and become more prominent, some manufacturers are outsourcing their IT to companies like EVERNET. We recent sat down with their CEO, Eric Buhrendorf to discuss how such an arrangement can be effective, as well as other prominent trends impacting information technology in the industrial realm.
Jeff Reinke, IEN: What are the advantages for a manufacturer to outsource IT?
Eric Buhrendorf, CEO, EVERNET: Without a doubt, manufacturers that outsource their IT functions gain access to a larger, smarter, less expensive and more available talent pool. Outsourcing also allows a business to operate “leaner” by only spending money on exactly the IT services the business needs. Additional cost savings come from the elimination of in-house IT employee salaries and benefits which weigh on payroll, regardless of their productivity and work output.
Most providers like us form very strong bonds and relationships with clients and essentially act and engage with the business as if we were employees, but they only pay for what they use. They can also concentrate on their core business without worrying about back-end systems.
JR: Downtime is a killer on the plant floor. An advantage of an in-house IT department is their ability to respond immediately. How does an external IT provider match that response time?
EB: Certainly resources that are located onsite can have a faster response to failures, but only related to physical issues such as if a cable gets unplugged, a wire is severed, or a computer system has some internal failure. However, physical failures constitute a relatively small percentage of possible system issues and can almost always be troubleshooted extremely quickly over the phone. When there is a physical issue, the resolution can often take an extended time, like ordering a replacement part or getting a wire repaired (depending on the type of break of course – in wall, or patch cable) so an onsite IT staff would face the same extended repair time.
We encourage the companies we work with to assign an internal Point of Contact whom we can train to effectively interface with us. For all other issues that can be resolved remotely, in-house IT cannot compete with the speed and effectiveness of an outside IT partner, notably a comprehensive Managed Services provider. In most cases, we spot an issue before the company does, we fix it, and down time is avoided proactively – or we are able to schedule the repair at a more strategic time for the business.
JR: Cybersecurity continues to be a huge concern. How do you work with manufacturers to ensure personal and proprietary data is kept secure?
EB: Oh boy, do you want the short answer or the long answer? Short answer: Through active, long lasting, trusted relationships with our clients, we continually advise, educate, support and aid them in implementing the best practices and technologies available.
Long answer: Let me start by saying, there is no panacea to cyberthreats and forgive me for inserting FUD here, (Fear Uncertainty and Doubt), but an attack on individuals and businesses is not IF but simply a matter of HOW.
Recently hackers have gotten into company systems through employee emails. We offer training to educate employees about possible security threats. The best way we can protect data and systems is through a full-service IT management methodology that can monitor, mitigate and respond to risks while working within budget constraints. Very few companies have every single recommended technology and/or process in place.
The fact is IT can be expensive. But by treating IT like the lifeblood of the business that it is, and implementing the best practices, tools, and processes available, we are able to guide our customers to a very high standard of security.
JR: What do you think are the key factors to consider in working with an external IT service provider?
EB: To select the best partner to fit their needs, a company should get a sense of the provider’s goals and culture. Will you be a valued colleague or just a faceless account? Will they respond quickly to your requests? While every company must work with profits in mind, I believe and have proven that profit follows good, quality work every time.
Notice I didn’t say experience or knowledge of technology. I’ll let you in on a little secret – the tech piece of our work is the easiest part of what we do as an IT provider. If you get a sense that your provider is taking too long to sort out an issue or constantly tells you an issue cannot be resolved, then you simply need a new provider. A good provider brings solutions, not excuses. To prevent unexpected costs, make sure their billing procedures are clear and upfront.
JR: How does working with a contracted IT provider impact software, automation and other, related purchasing plans?
EB: A business should rely on its IT provider for all initial consultations for purchasing, and the provider should always act in the company’s best interest first. Beware of an IT provider that binds sales of products and services to the provider, making it seem that your company will always NEED this provider, lest you forfeit the benefits of said products. Good, honest, providers don’t build their business that way. Your company should be able to switch to another provider without impacting access to products.
JR: Looking forward, what do you think will be the most disruptive technology hitting the manufacturing sector over the next 5 to 10 years?
EB: I think automation is going to CONTINUE to be the most disruptive, non-specific technology over the coming decade. We can already see the will and desire of the people to bring manufacturing back home. The only way that is possible is a continued transition from human labor to automated, robotic and/or artificial intelligent labor. Technology’s very virtue is to facilitate doing more with less…technology provides capital. Manufacturers who leverage resource planning tools, processes, and equipment will be best positioned for the future.
Additionally, 3D printing for either production, molding, or modeling will continue to be disruptive to manufacturing.