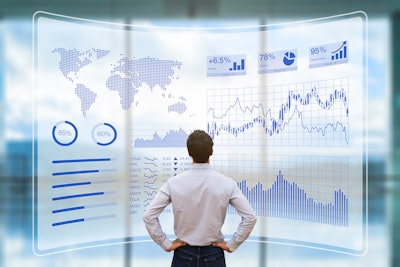
When managing equipment in an asset-intensive organization, any supply and demand shocks can affect return on investment, as the output fluctuates in value.
Because capital assets have long lifecycles of 10, 20, maybe even 50 or more years, executives, corporate boards and financiers must see a way to liquidate the cost of these assets given fluctuating conditions. It is simple enough to profitably manage assets during periods of sustained economic growth, or even a typical recession.
But during a drastic change in demand, significant portions of an asset portfolio may be idled. Regulatory changes or changes in global trade patterns can render useless the assumptions used to justify an asset in one region while placing a premium on productive capacity in another. Mothballing or reactivation of equipment carries hefty price tags, and the equipment is not worth much from a resale perspective on the open market.
A New Breed of Data Reporting
Standard business intelligence (BI) tools let executives see what has just happened. But there is a new breed of reporting solution, operational intelligence, designed to bring fighter jet tactics into the board room. Operational intelligence (OI) was created to help pilots make rapid adjustments in real time, moving through the stages of observation, orientation, decision and action (OODA) faster and smarter.
OI speeds up a company’s movement through the OODA loop. It is built around a business map—a clear visualization of how value flows through the organization. Metrics are aligned with the business map to better identify constraints in the enterprise value stream. The software then runs analysis to provide a way to take immediate action directly in those operational systems, enabling rapid response to emerging information.
For organizations substantially impacted by external factors such as commodity prices, OI can include external data on leading indicators, providing advance notice of potential business impacts before business signals would manifest themselves looking simply at internal metrics.
As they move through that OODA loop, executives must make decisions about their geographically dispersed, global portfolio. Enterprise Asset Management (EAM) software must support them in this by enabling them to streamline refits, shutdowns, decommissioning or construction and commissioning of new assets, ensuring that all health, safety, environmental and corporate social responsibilities are adhered to.
Modern EAM includes templates used to manage similar assets or asset classes at multiple sites without creating each asset separately in the system. Entire classes of assets can be created rapidly with standard maintenance, parts, tools and other data. Managers can edit these objects to accommodate individual site differences including regulations in different countries. Organizations moving capacity from one location or division to another will reduce non-value-added work while increasing standardization and consistency.
Support for e-Commerce
For decades, maintenance, substantive refits and overhauls have been undertaken increasingly by contractors rather than maintenance department staff. The percentage of industrial organizations outsourcing maintenance increased sixfold between 1990 and 2000 alone. As volatility increases, this collaborative approach to maintenance, and even operations contracting, will become more common because contractors can staff operations in a more flexible fashion than they could with direct employees.
Some of this contracted maintenance work may be performed by equipment vendors as part of a full lifecycle support contract. In others, maintenance of equipment, facilities, and projects requiring specialized tools, materials testing and other maintenance work may be put out to bid or handled under a contract framework agreement with maintenance or construction organizations.
To better manage the broad spectrum of maintenance organizations, executives of asset-intensive companies will need EAM software that automates the process of letting work to bid, accepting bids and tracking performance against the contract. EAM must also offer contractors web-based portals to report completion of tasks, submit invoices and act as a more integral part of the organization.
Unfortunately, most EAM software were designed more as an isolated computerized maintenance management system (CMMS)—a work management tool for maintenance technicians. A point-to-point integration with finance, inventory, risk management and quality functionality of enterprise resource planning software may be possible. But as business conditions and the financial return on asset operations change, executives relying on separate systems with a limited set of integrated fields will find it difficult to make decisions based on real-time visibility of operational cost and asset readiness.
In order to deal with volatility, EAM must be the system of record—not a point solution that lives alongside the software used to run the business—and address the entire design-operate-maintain asset lifecycle. EAM software needs to be designed as a pure play application from the general ledger right down to the individual equipment object on a facility floor.
Consider the conundrum faced by an executive team as new productive capacity comes online. A head pressure problem develops in a critical compressor unit. Maintenance finds it lacks the information to diagnose the problem because it is buried in a stack of CDs and binders left by the consulting engineers that designed the asset.
Other data is contained in as-built documentation left by the contractors. Tracking down the information necessary to operate the asset winds up costing downtime, man hours and dollars the company can ill afford. Often, executives also find a new asset suffers from unplanned stoppages caused by the same design flaw as the asset it replaced. Although data contained in years of maintenance records would have revealed the design changes that were necessary, the system engineers did not have the ability to review that data in a meaningful way. As a result, an opportunity to increase productive capacity and lower cost is lost because of inefficient handling of asset data.
Geographic, market and technological changes are obsoleting assets and requiring new capital investments more rapidly than ever before. This means asset-intensive businesses need the visibility and control to react to changing conditions. Without an operational intelligence system and streamlined asset lifecycle management tools they will be unable to quickly reconfigure assets and face a delay in action and decision-making that will leave them exposed to enterprise risk.
As IFS Vice President of Sales, Katherine James is responsible for the organization’s strategy, development and execution within her territory.