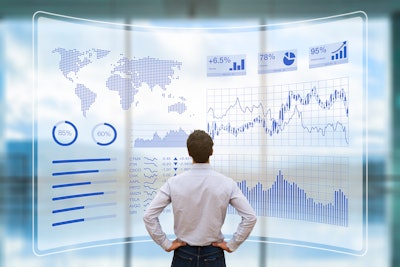
The IoT is enabling advances across multiple market sectors, but it is the Industrial IoT (IIoT) that is having the most impact. It is already the biggest IoT vertical and covers multiple types of projects across industry, from simple data collection to more complex projects incorporating just-in-time manufacturing and predictive quality control.
The biggest benefit of the IIoT is how it is creating innovative solutions to help manufacturers achieve their business objectives by delivering better services and products to their customers. There are three principle reasons for implementing an IIoT application – to make money, to save money, or to stay compliant – and sometimes all three can be delivered. Certainly, at Telit, we would not counsel anyone to consider investing in an IIoT project unless it meets one or more of those three objectives.
Data is the New Gold
A properly implemented IIoT should enable manufacturers to collect data from every step in the process. Every machine can and should produce data, and the processing of that data should deliver invaluable information that helps create more efficient processes and factories. Look back 10-15 years, and there was a big shift in production, with manufacturing operations leaving the U.S. and Europe for China because labor cost was the most important consideration.
The IIoT is set to have the same effect as labor costs; data is the new gold. Information from the IIoT will make manufacturers’ assets perform in a more cost-effective manner – so the better the data, the greater the improvements.
Let’s look at some examples of the transformational effect of the IIoT. One of the largest car vendors in the world implemented a replacement IIoT solution that significantly reduced latency in their systems.This reduction was so relevant that in just one plant it created 3,000 minutes more of uptime. This plant produces at a rate of about $30,000 per minute, so that’s an extra $90 million.
Additionally, integrating the solution operator by operator, line by line and shift by shift, there is now a continuous link between what is being produced and how it is being produced, increasing productivity and quality control. Based on the data gathered, the manufacturer achieved significant reductions in both set-up time and line downtime.
Global names like Mitsubishi and Honda rely on the IIoT to remotely connect sophisticated machinery with technicians and engineers who constantly check manufacturing performance levels, ensure preventative maintenance, and quickly react to any issues that may affect production. Chip giants utilize the IIoT to maintain top-level cybersecurity to protect its IPR from hackers. Multinational pharmaceutical companies use the IIoT to audit every step in the manufacture of their products to ensure full compliance with regulations and laws.
The IIoT isn’t limited to high end manufacturing. Anything can be connected. In Brazil, the IIoT is used to transmit data about the condition of the sewer network and sends alerts to maintenance crews when cleaning is required. The IIoT can also be used to explain unusual behavior.
At a manufacturing plant In Mexico, an application measuring the productivity of each machine was able to show how one machine was producing less at night than during the morning and afternoon shifts. Upon investigation, it was revealed that the operator on the evening shift was leaving the machine on a regular basis – to chat with his girlfriend.
Manufacturers are embracing the technology and investing, and without needing to hire an army of software engineers to rewrite protocols. There are experts in the IoT space that can deliver guaranteed connectivity across all systems – reducing the implementation time to a couple of days.
The IIoT is changing the face of manufacturing, from predictive maintenance and supply chain management to condition monitoring. Yet only a fraction of the market potential has been explored so far. If you look at the Fortune 500, there isn’t one company that doesn’t have an IIoT application, but in most the technology is yet to permeate the whole organization.
There are huge untapped possibilities, and work to be done to achieve the true revolution that the IIoT promises. This applies not only to the actual manufacturing processes, but throughout the supply chain, leveraging connectivity for better traceability and quality control. The IIoT can, and will, touch, impact, and improve every step.
Ricardo Stefanato Buranello is the Global VP - IoT Factory Solutions for Telit, and has over 10 years of experience in the M2M/IoT industry. Buranello is responsible for Telit’s global factory solutions, which is a leading provider in industrial solutions for remote connectivity, edge logic automation, OT and IT integration.