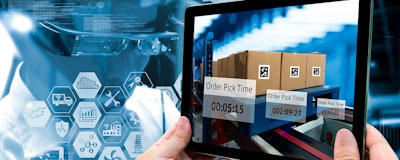
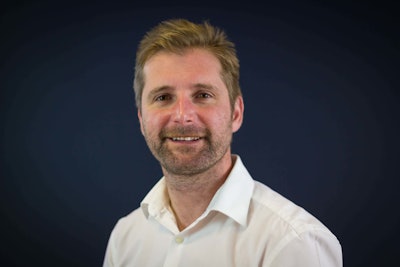
The condition monitoring market is estimated to grow from $2.38 billion in 2018, to a huge $3.50 billion by 2024. This rapid growth is attributed to manufacturers increasing focus on running assets optimally, rather than working them to the point of failure.
What’s Driving the Boom?
Remote monitoring systems aren’t a luxury. Today, necessity is driving the rapid adoption of these systems. The math is simple. The more unplanned downtime a plant undergoes, the lower the throughput for the production line. Less product means less revenue. This is why more maintenance managers are moving away from reactive maintenance, in search of continuous updates on asset health.
But, it is not just about bottom-line profits, running equipment to failure can have disastrous consequences. In the best-case scenario, it may be that a bearing fails or needs to be replaced — a relatively quick fix. However, if this failure causes damage to the motor shaft, coupling, or even the gearbox, issues of sourcing a replacement may lead to extended downtime and high costs. This time can be minimized by knowing which parts supplier to contact, particularly if the part is obsolete.
The necessity of remote monitoring is enlarged when you consider the changing workforce across the U.S. Today’s workforce looks very different than it did a decade ago. Lean staffing models brought in by past economic downturn are still apparent, bringing with it less depth of engineering talent — not helped by the national skills shortage. The new generation of workers now face the challenging combination of working with both aging legacy parts, and complex new equipment.
However, remote monitoring can also be accessed as a service, supported by off-site experts — taking the pressure aware form employees. This is part of a larger trend of vendors offering service-level agreements rather than asking for a one-time, upfront payment. Servitization is a hot topic, but this subscription model does mean less upfront costs, and ongoing support. The new business model means businesses pay remote monitoring equipment vendor for factory uptime, rather than the remote monitoring equipment itself.
How Will This Technology Be Used?
With remote monitoring as a service now available to organizations without the budget or skill for independent implementation, they make the move from reactive maintenance to predictive maintenance schedules.
These systems track parameters such as current draw, temperature and vibration, embedded in the components themselves, or placed externally as a retrofit attachment.
For example, a higher temperature could provide engineers with an advanced warning of lubrication breakdown. Similarly, by monitoring the vibration spectrum for change, it is possible to discover and monitor signs of wear precisely, by comparing to baseline values. A trained vibration analyst can detect the presence of a bearing defect, a broken impeller blade and much more.
Most factories will take a phased approach to implementing this technology. We’ll see businesses reap the benefits of tackling problematic equipment first, and with this success, remote monitoring programs can then be rolled out progressively over time. After tackling the troubled assets, high-value assets, critical assets and hard-to-reach assets can then benefit from remote condition monitoring.
The Culture Change
What was once the maintenance manager’s sole mission to persuade C-levels to update and adopt technology in their facility, is now a company wide task. Upper management is seeing this technology as an essential competitive differentiator, and the need to digitalize their factories.
This change in perception has positive implications for the industry. As remote monitoring becomes a company wide priority across the U.S., it’s the people at the top that will enable and support the expenditure of new remote monitoring systems. Ultimately, everyone will benefit from this, especially if their factory is experiencing the convergence of old legacy equipment and new technology.
As remote monitoring becomes more affordable, sophisticated and user friendly, the possibilities for the industry become endless. The servitization model certainly softens concerns over budgets and skills, while the ever-improving precision of this technology enables huge insight into the future condition of company assets.
Jonathan Wilkins is a marketing director at EU Automation.