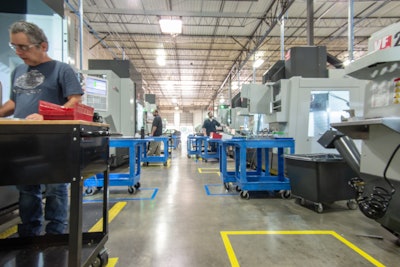
Plethora was co-founded by Nick Pinkston and Jeremy Herrman in San Francisco. The company specializes in end-to-end manufacturing and provides CNC milling and turning - supporting tolerances as tight as 0.001". Their clients work in aerospace, defense, robotics, medical, automotive, consumer goods, and more.
In June the company opened a new facility in Marietta, Georgia because its original location had reached capacity. The company is also looking to hire up to 250 employees by 2021. We recently sat down with Herrman to discuss how his company has leveraged automation and artificial intelligence to assist with this growth.
Jeff Reinke, IEN: Manufacturers would almost unanimously agree that investments in automation and AI would benefit their operations. The issue is often understanding where to start. What advice would give to an established manufacturer on where to start when upgrading automation equipment and platforms?
Jeremy Herrman, Plethora: AI requires data, and many manufacturers fail to capture the kinds of data points they’ll need to see evolutionary improvements. A great place to start is to map out your processes and list all of the relevant data points. Usually, there are third party solutions for gathering and tracking that data - even for low-tech machines like band saws.”
JR: What about integrating artificial intelligence into their production flow?
JH: Integration is everything, and if your current manual processes make it difficult to integrate automation, then you are going to face challenges. One way to prepare is to build insertion points for automation into your current workflows. It could be as simple as a checklist that a person inspects before moving a part to the next station.
Once you are collecting data from your factory, it’s time to gain insights from it. Manufacturers will often find patterns in the data that suggest areas of improvement even without applying complex algorithms or specialized databases.
JR: What do you think is the most significant competitive advantage you’ve seen from either the advanced automation or AI present in your factory?
JH: Our pace of innovation. Plethora is a manufacturing company run like a software company. We’re able to push out updates to our software quickly and iteratively, at a much faster cadence than the manufacturing world typically embraces.”
JR: How have these technologies impacted your ability to find and keep workers?
JH: At Plethora, we rely on talent comfortable with embracing new technologies and processes. On the engineering side, we’ve got engineers with a passion for solving physical world problems. On the manufacturing side, our processes are built on top of a strong foundation in CNC machining. We do a great job of training machinists on how to leverage their background and experience alongside our technology.”
JR: How much training have you had to implement to stay on top of these technologies as they continue to evolve?
JH: Being a software company, we’re iterative. Instead of big sea-change updates every 12-18 months, we’re constantly pushing out minor improvements. In a way, this really reduces the amount of ongoing training required. Each iteration, if done right, should be intuitive and non-disruptive. So while the tools our teams use a year from now may look very different than the tools they use today, they may not notice most of the little steps we take to get there.”
JR: Is there one specific technology that you think will impact manufacturing more over the next 2-5 years?
JH: Manufacturing takes time. Any technologies, software, or process improvements that can decrease the amount of time required to make a part have a greater chance of becoming widely adopted. Speeding up cycle time for customers lets them iterate on their prototypes faster, and ultimately, get to market sooner.”
JR: Do you think there is one technology that is currently being given too much priority by manufacturers right now?
JH: Artificial Intelligence is hyped by many companies these days. I’ve seen the term used to describe cutting edge neural networks, as well as traditional algorithms that have been around for decades. Machine Learning is a very real thing with tangible benefits to manufacturers in terms of continuous improvement and predictive maintenance. AI in the form of Deep Neural Networks that support true 3D geometry is still under heavy development in academia but has not yet made a large impact on today’s manufacturers.
My issue with AI hype is that it distracts from solving very real software and data problems first, starting with storing Geometric Dimensioning and Tolerancing information in the same file as the 3D geometry. This doesn’t require advanced AI; it needs the cooperation of the CAD industry to push for modern workflows to manufacturers.
JR: If you could give U.S. manufacturing one ability, gift, super power, etc., what would it be? Why?
JH: I’d ask for more standardization and compatibility across CAD vendors. The realization of Digital Twins can only be realized with interchange formats that support all Product Manufacturing Information. When you throw in new data features needed by additive manufacturing, there’s an opportunity that these formats will become more fragmented, leading to difficulty supporting new forms of manufacturing like additive/subtractive hybrid machining.”