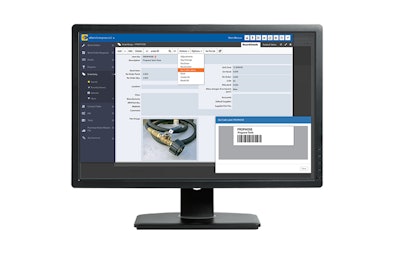
Computer maintenance management system (CMMS) software can reduce equipment downtime, extend the life of assets, reduce maintenance costs and much more. Developing advanced software features to help customers solve problems is a large part of the continuous improvement and innovation history of the eMaint CMMS software.
Unfortunately, many times organizations only use the most common features such as work order management, preventive maintenance and inventory management. However, once a CMMS software implementation is underway, companies that make time to take advantage of more than a few CMMS features expand not only the value of the software but also increase opportunities to speed up a return on investment.
Here is a list of five underused but powerful eMaint CMMS software features that we believe solve small and big issues, and improve maintenance processes.
1. Parts Checkout with Barcode Scanning – eliminate manual barcode input
This feature allows personnel to use a scanning device to capture barcode numbers on parts. Many maintenance workers use a software-enabled scan-to-web application. Once scanned, the information will appear on a computer or mobile screen including item number, description, parts on hand, unit cost, and checkout quantity. The part can then be assigned to a work order (WO) number.
- Save time when checking out parts by scanning part numbers
- Associate checked out parts to WO numbers
- Adjust parts inventory with each checkout
- Store and view parts inventory history records
- Track parts, number of parts checked out, and costs
2. Interactive Plans Feature – visualize asset location and asset data
The Interactive Plans feature makes it easy to access data and improve efficiency using an email intuitive image mapping tool. Personnel can upload a floorplan, site map, schematic, or other image using the system’s document storage feature. Assets can be pinned on the image map, and when M&R teams hover over the pin, they will see a snapshot of the asset information. Personnel can navigate to records to schedule work, view WO histories, and more.
Summary:
- Create an interactive facility map and pin the location of each asset
- Add asset ID fields and populate with important equipment information
- Connect WOs and request forms to an asset pin and click to view record information
Some companies rely on a large fleet of vehicles to carry out daily tasks, while others need to reserve space. eMaint’s Asset Reservation feature helps ensure a vehicle or room will be available and eliminates reservation conflicts.
When personnel book assets for specific times, the CMMS software sends an email notifying them when the request is approved or rejected. Once a reservation is accepted, other users cannot reserve the asset during that time. Additionally, requestors can view approved, rejected, and pending requests on a calendar screen, as well as track the vehicle or room request history at the asset level.
Summary:
- Prevent room or vehicle double booking
- Ensure assets are compliant and available when needed
- Receive email notification once request is approved
- View approved, rejected, and pending reservation requests on a calendar
4. Time Clock Feature – ensure accurate work order clock in and clock out times
The eMaint Time Clock feature allows technicians to clock in and clock out of a WO from a dashboard or mobile phone. The feature also tracks the work location and coordinates it with the technician’s sign in and sign out times.
Occasionally technicians forget to clock out of a WO once it’s completed. The eMaint system will not allow technicians to clock out if they are still signed into the WO.
Summary:
- Ensures accurate work completion times
- Tracks clock in and clock out location
- Ensures technicians sign out of completed WOs
5. Work Permit Feature – streamline and reduce processing times
Work permits are a crucial part of managing high-risk work activities in manufacturing plants and other industrial environments. Many organizations undergo seasonal, high-volume maintenance demands and need to hire contract workers. The Work Permit feature helps simplify the process.
A common work permit process often includes the use of a paper form which usually requires multiple hand signature signoffs, including the contractor. Coordinating and making sure all work permits have been routed to the proper people and contain the necessary signatures takes time.
The eMaint CMMS software can upload work permit forms as PDFs. Managers can use the built-in PDF editor to revise the document to fit the organization’s needs. Contractors can then access the stored work permit via eMaint and sign the form using an e-signature. Additionally, managers and supervisors can route, track, and view the work permit progress to ensure the required signatures have been secured. Once the work has been completed, the work permit can be linked to a WO or PM schedule.
Summary:
- Eliminate paperwork permits and processes
- Store PDF work permits in eMaint’s document storage
- Easily access and edit work permit forms using the in-app PDF editor
- Track the work permit signoff progress
- Associate completed work permits to WOs or PMs
CMMS – a first step toward proactive and predictive maintenance
CMMS helps M&R teams plan maintenance tasks, as well as analyze and use the asset data collected and stored in the system to detect equipment problems and predict failures before they happen. With the advent of the Industrial Internet of Things (IIoT), scalable computer maintenance management system such as eMaint has become an essential part of a connected reliability journey and first step toward proactive maintenance.
As the Director of Training & Education at Fluke Corporation, Weslley Cavalcante manages all online written and audio-visual training content. Additionally, he oversees a team of product trainers together deliver nearly 400 live training engagements a year. He may be reached at [email protected]. For more information, visit www.emaint.com/.