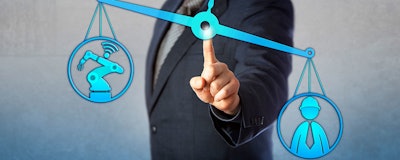

New technologies like the Industrial Internet of Things (IIoT), machine-to-machine (M2M) communications, 3D printing, AI and robotics are revolutionizing the manufacturing industry, making it more connected, intelligent, automated and fast-paced than ever before. These technologies have not only changed the face of manufacturing, but they’ve also changed the knowledge and skills demands of its employees.
While most manufacturers are still in the early stages of digital transformation, they’re already feeling the effect it’s having on their workforce. That’s why having the tools to onboard and upskill employees is more critical than ever—so employees can keep up with the business and manufacturers can get ahead of the competition.
The Widening Skills Gap
But onboarding new workers, retaining employees and attracting new ones, especially those with the requisite skills, in such a fast-paced and disruptive environment is proving to be a challenge. In fact, according to a Deloitte and Manufacturing Institute report more than 2 million U.S. manufacturing jobs will go unfilled over the next decade. As positions remain unfilled and the skills gap continues to grow, many manufacturers are casting a wider net in the search for new talent, with up to 16 percent of new hires coming from non-manufacturing sectors. The result is an even more eclectic workforce made up of employees from multiple generations, cultures and even industries.
But the manufacturing workforce isn’t the only area that is evolving. Smart manufacturers are attempting to achieve a new era of operational excellence where consistent and reliable execution drives both growth and a competitive gain. And a huge part of that operational excellence is ensuring high levels of safety, quality and productivity across the entire organization, particularly as new regulations are adopted.
As the complexity increases, employees are expected to know more than ever and often have to shift gears mid-stream to acquire advanced technology and business skills to accommodate the business. At this pace, organizations often do not have the tools to continually train employees and prevent knowledge gaps that can negatively impact the business.
Empowering the Workforce Through Training
Today’s manufacturers and their workforces are anything but traditional. And yet, despite the need to achieve operational excellence through the performance of their employees, most organizations are still using outdated training methods that pull workers away from the job floor. Because these traditional methods don’t always support the needs of modern manufacturers or today’s mobile employees, they do little to drive engagement and performance, and production can suffer as a result. This has manufacturers looking for a smarter, more effective way to onboard, upskill and keep employee knowledge up to date.
To ensure the skills gap does not increasingly widen and the existing workforce is educated on critical information (such as hazard communications and operating instructions for new machinery), manufacturers are looking at new approaches to training to empower the very people that will allow the business to achieve competitive advantage and operational excellence.
One such way is through microlearning which breaks employee learning into bite-sized chunks and allows employees to receive the training on mobile devices during the course of their work day. It also includes a gamified approach which organizations are finding further engages employees and boosts training participation rates. In fact, a recent ATD study shows that 81 percent of organizations are currently using (or planning to begin using) microlearning to support their employees.
As an example, a leading North American provider of critical component solutions for manufacturers is using microlearning to streamline the delivery of health and safety training, improve quality assurance and increase the amount of training employees receive—all without sacrificing productivity. In the process, the company is building a highly knowledgeable and engaged workforce that is empowered to make the right decisions to keep their operations safe, productive and profitable.
Change Behaviors to Drive Business Results
Because microlearning, like manufacturing, is technology driven, it can grow with individual employees as they develop throughout their careers. This allows manufacturers to increase employee knowledge and upskill their workforce on an ongoing and continuous basis—which is increasingly important in an industry where knowledge and business process requirements. As an example, many manufacturers are incredibly focused on decreasing their Recordable Incident Rate (RIR) and Lost Time Injury Frequency Rate (LTIFR), but struggle to achieve a reduction. In this case, microlearning can be used to focus on these specific knowledge gaps that need to immediately be addressed.
When employees are engaged and participate in daily training, their knowledge levels are more likely where they need to be. And, should knowledge levels start to slip or individuals begin to exhibit the wrong on-the-job behaviors, microlearning adapts to deliver tailored content to fill those gaps and change behaviors. The ability to identify and correct the wrong behaviors and ingrain the right ones enables manufacturers to prevent costly accidents and mitigate risk while keeping production moving.
Digital transformation is a major force in the new industrial revolution. However, without properly educating and upskilling the current and future workforce to reduce safety incidents, increase quality, deeply ingrain corporate values or simply bring consistency from facility to facility, team to team and employee to employee, the skills gap will continue to widen. For this reason, training methods like microlearning have emerged as a critical component of creating a knowledgeable and productive workforce. As manufacturing organizations continue to transform, employee training will play an increasingly important role in enabling organizations to achieve competitive advantage and operational excellence through the performance of their workforces.
Carol Leaman is CEO of Axonify.