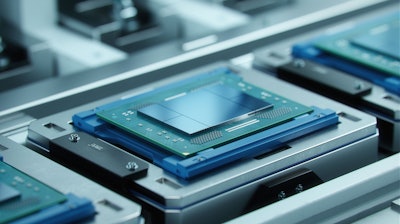
With advanced microchips powering so much of the global economy – and underpinning so many crucial defense systems – semiconductor fabs have become, geostrategically speaking, the new oil fields. Perceived threats to what has evolved into a dispersed, geographically-specialized global supply chain has many of the world’s major powers embarking on what looks to become a multi-decadal effort to onshore increasing volumes of semiconductor manufacturing.
The global effort to secure the semiconductor supply chain in general will have a cascading effect in terms of pressure to secure many specific sectors of semiconductor supply chain. Quite simply, there will be more suppliers in more places supplying more fabs that will make more chips. All that introduces risk – particularly in manufacturing.
When it comes to making semiconductor microchips, there are two primary risks:
- The first is that the shop-floor equipment – tools of production that often cost tens of millions of dollars and which have tens of thousands of components – will arrive in these new fabs harboring trojans that could propagate throughout fabs and disrupt production, or worse.
- The second is that malicious code gets introduced via one of the thousands of networked internet-of-things (IoT) sensors that help keep the hundreds of tools on the shop floor humming 24/7/365.
So, how do you mitigate those risks?
Virtual machine in a Sandbox
Let’s say a $150 million extreme ultraviolet lithography unit with 100,000 parts and two kilometers of cabling arrives at the fab. Inspecting every component is a non-starter. But you also don’t want to just plug it into the production line and hope for the best, either. Semiconductor manufacturers are now addressing this conundrum through a virtual-machine-based sandbox. It’s the same basic idea as something NASA has been doing for decades.
When you launch a robotic spacecraft, the onboard computers have flown the mission countless times already – or at least they think they have. But they’ve really been plugged into other computers that simulate vector, orientation, communications, temperature, inputs from scientific instruments, and so on.
Similarly, new approaches to semiconductor-shop-floor security have incoming semiconductor manufacturing equipment spend some quality time in a production environment simulated on a virtual-machine-based sandbox environment. There, hardware and software can be assessed for suspicious activity without introducing risk to actual production where, for example, a 3nm wafer can cost about $20,000.
IoT Safeguards
IoT sensors present a different problem. These sensors have become indispensable in keeping tabs on production, sniffing out problems with equipment slipping out of tolerance before ruining batches, and triggering predictive maintenance. The enormous volumes of production information they generate through the roughly 1,000 process steps involved in turning a silicon blank to a functioning semiconductor provide deep pools of data upon which advanced analytics increasingly feeds.
But IoT sensors also represent a new attack surface that’s ripe for bad actors.
There are two approaches to improving IoT security on the shop floor. One involves software hinging on blockchain, which lacks a central control hub (and thus lacks the vulnerability of such a hub). Cryptographic algorithms embedded in the blockchain make the data generated by the IoT tamper resistant, because the various participants in the blockchain get notified should such meddling occur.
The second way to improve shop-floor IoT security is through hardware embedded in IoT devices. Principal among these are PUF (physical unclonable function) devices that provide a physical entity with a unique fingerprint. Combine blockchain and PUFs and you’ve gone a long way in ensuring that shop-floor IoT devices are doing what they’re designed to do – and nothing more.
There is, of course, much more to securing the semiconductor supply chain than simply keeping the shop floor safe and running smoothly. These sorts of safeguards must happen beyond the walls of the semiconductor fab, too. The global semiconductor supply chain is reconfiguring itself for security in the broadest sense. Those running new semiconductor manufacturing facilities in which countless billions of dollars are being invested must also do their part to ensure the secure, uninterrupted production of these indispensable resources.
David Shen is solution management director for High Tech at SAP.