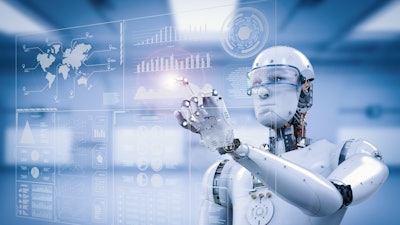
With so many manufacturing plants around the world forced to adapt and supply chains in disarray, technology has become a beacon, creating an element of visibility and automation to help navigate through severe disruption. As part of the pandemic response and recovery, manufacturers must explore new ways to make operations more agile, more resilient, and better able to navigate through uncertain times – regardless of when or where disruption comes from.
Social distancing guidelines alone are forcing manufacturers to reduce staff and implement protocols that may radically change the cadence and processes within a production environment. This means more reliance on technology and automation wherever possible so employees can be safe.
The Paper Jam
Many manufacturers are still notoriously reliant on paper processes. Bills of lading, ship cargo manifests, customs declarations, packing lists, and other documents concerning trade and transport are still heavily paper-based. But the time it takes for senders to complete the forms, to deliver them to the appropriate recipients, and for those recipients to log that information into whatever accounting systems they happen to be using, is typically way too long for them to be acted on in a timely way. Besides that, mainly for competitive reasons, suppliers aren’t always forthcoming about sharing their sensitive, high-value business information.
Although many producers have worked out satisfactory arrangements to secure essential information from their Tier 1 suppliers, maintaining visibility into Tier 2 and Tier 3 suppliers is a persistent problem. It is not, however, an impossible one. For example, according to a recent World Economic Forum report, blockchain can provide a secure vehicle for information on performance and risk as well as for payment terms1.
A Need for Better Intelligence
The issue of limited visibility is not restricted to dealings with overseas vendors or others in your global supply chain; it also applies within your own four walls. Information concerning the operating status of machinery, materials, variances, inventories, personnel, and orders in the pipeline, in addition to data about current customers, can be tremendously valuable in minimizing downtime, assuring quality, and meeting demand. But much of that data is never collected or analyzed in systematic ways to produce commercial value.
Manufacturers will need to rely on better analytics to understand and respond faster to change that is happening along their supply chain. This means harnessing more contextual data while relying on dynamic analytics to know exactly what is happening within their own four walls and out to every major component on the value chain. Supply chain disruption has been significant, which means that now – more than ever – manufacturers need accurate, real-time information to efficiently restart operations and move toward recovery.
If manufacturers had been able to see in graphic detail the supply chain disruptions that started to occur in China at the outset of the COVID-19 outbreak, actions could have been taken to minimize the impact. This intelligence could have been used to track the ripple effects onto vendors and shipping options, as well as on-demand, delivery, revenues, costs, labor and so forth just as they took place. Manufacturers could have initially taken steps to limit damages, and then to prepare how best to resume operations under the new market conditions.
You could have been proactive instead of reactive.
You don’t have to be a clairvoyant to collect this kind of information. Much of it is out there for anyone to harvest and interpret, provided they have the right data-gathering tools or at least access to people who do. The fact is that lack of visibility into the various aspects of a company’s business has always been a source of friction in the delivery of goods and services. And in times of crisis, visibility is essential to making business-critical decisions.
At least in principle, you could always look to big-ticket items to enhance your organization’s future well-being – major capital projects like new manufacturing locations, strategic acquisitions, re-equipped production facilities, proprietary transportation assets, and so on. But the technology of knowledge – the devices, software, and work processes at the heart of industry’s current digital transformation – are a more practical way to manage today’s challenges, and the returns on those investments are compelling. Even so, there is still some reluctance to make the transition.
Simplifying the Complex
Despite today’s challenges, we are in what some have called the “golden age of data,” where both the volume, the velocity, the accuracy, the types, and the sources of data are all exponentially larger than ever before. The instruments used to gather, transmit, and analyze that information are more abundant and less expensive than at any time in human history. Perhaps even more significant, there is a growing culture of openness toward data-driven, or at least data-informed decision -making, in businesses of every sort. All of this creates a golden opportunity to use data in a way that simplifies the complex to drive better efficiency and transparency throughout manufacturing operations.
At the same time, however, the collection and analysis of industry data is not a one-size-fits-all proposition. Every company’s information needs are different. So are their resources for investing in the hardware, software, and personnel required to turn data into a source of strategic advantage. But it’s getting easier. The information management toolkit is growing rapidly. Electronic devices are becoming less expensive, and most of them are getting a lot smarter. Many technologies, including cloud-based platforms, are easier to deploy and maintain.
As we ponder the new reality that will emerge from the change triggered by the coronavirus, it isn’t likely we’ll see completely unmanned factories humming along in the dark without human intervention. But, there are many positive steps manufacturers can take to harness automation and analytics to move toward a healthy recovery. Automation and data-driven technologies are already enabling manufacturers to become more agile, more efficient, more profitable, and better able to foresee as well as to handle the next crisis, whatever shape it has, and whenever it next arises.