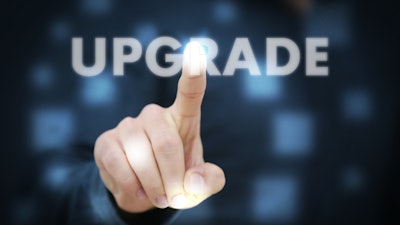
A 2019 report by Deloitte touted that almost every metric manufacturers care about was headed in the right direction. A decade of economic growth and higher levels of productivity and capacity bumped the U.S. GDP by three percent and added 300,000 new jobs in the preceding year alone. However, that report also asked the pointed question: How long will the boon last?
What a difference a year can make.
In 2019, the Manufacturers Alliance for Productivity and Innovation (MAPI) reported that the sector was expected to recover all of the productivity losses it suffered during the 2008–2009 recession by mid-2019. Now, barely a quarter into 2020, crashing oil prices and a global pandemic have again erased those gains, tossing the economy into a period of very uncertain decline. Businesses in every sector are being forced to shutter their doors until the pandemic has been contained, and the long-term economic outlook is still uncertain.
Over the previous decade, manufacturers boosted productivity and capacity and turned those improvements into better financial returns for shareholders and investors. Today, they worry about how (and for how long) shelter-in-place policies across the country will affect those gains. And they’re concerned that those same investors are pulling back, anxiously holding their breath to assess if the next Big Recession has arrived.
Of course, the recent downturn has only aggravated a tenuous staffing situation and other potential risks. In good times, manufacturers worried about the high number of unfilled job openings. Today, they still lack workers with the skills to operate today’s highly complex and technologically sophisticated factories, but many of those they do have aren’t able to leave their homes. Meanwhile, high-profile trade tensions, especially with China, continue to be a legitimate concern, prompting many manufacturers to reassess their supply chain risk.
While many manufacturers would argue a new recession has already begun, it’s not quite a Dickensian worst-of-times moment. While some are postponing technology projects, smart manufacturers will continue pursuing tools and strategies to help them better serve their customers, improve productivity, and maintain capacity. Beyond those benefits, technology is an important tool to establish the kind of work environment that will attract and retain workers when the economy is again growing.
Even in the midst of the dip, automation technology can help make the most of the resources and workers manufacturers have available. Prior to the 2020 downturn, 49 percent of manufacturers had begun tapping automation to improve their operations. While some focused on deploying robotic arms to boost productivity on the factory floor, others applied technology to automate a wide range of processes and operations.
One example of the latter is in the realm of procure-to-pay, improving the financial operations process of managing suppliers, invoice processing and outbound payments. Manufacturers are leveraging the power of AI, machine learning and robotic process automation (RPA), which can automate and improve what is typically the highly manual, error-prone process of submitting invoices into various portals to ensure they’re available for timely payment.
It’s a process that previously required skilled accountants to spend an inordinate amount of valuable time inputting data and shepherding invoices from their enterprise resource planning (ERP) system to portal after portal — a process that often leads to errors, continuous training and unhappy employees.
To understand the genuine potential of RPA, just follow the money. According to Gartner, global spending for RPA software reached an estimated $680 million in 2018, up nearly 60 percent from the year before. Gartner projects that annual spending on RPA will reach $2.4 billion by 2022. And while the current recession might seem to dampen those projections, the cost of “keeping the lights on” without the added efficiency provided by AI, machine learning and RPA is even higher.
How does it benefit a manufacturer to automate the tedious manual tasks required to move orders and invoices—all the way from procurement and accounts payable through order processing and accounts receivable? The results are universally positive – on-time payments, improved customer and vendor relationships, reduced costs and happier employees. These factors aren’t just dependent on a rosy economy.
True, employees are more fulfilled and content because they no longer have to spend hours manually doing work that’s better suited to technology. But also, AI-driven process automation frees workers to do the work they were trained to do — and to devote their time to tasks that contribute more meaningfully to a manufacturer’s bottom line.
Whether macro-economic conditions will improve, stay the same, or deteriorate is not something that manufacturers can control. But by taking steps to incorporate technologies like RPA, manufacturers can set themselves up to do well, no matter how the overall economy fares.
Steve Smith is the U.S. Chief Operations Officer at Esker, a leading provider of automated process software.