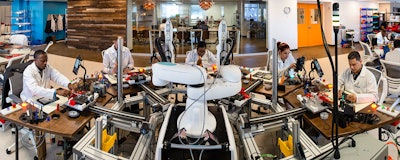
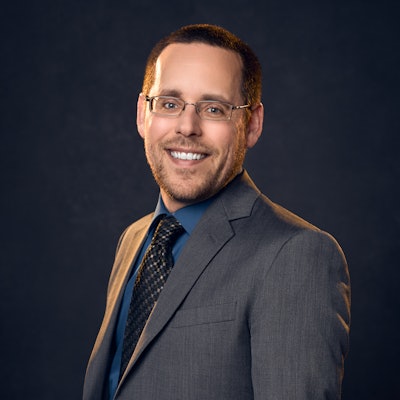
Imagine yourself on the factory floor of a computer manufacturing facility. What do you see? What do you hear? While 77 percent of Americans own smartphones, very few understand where they’re built, by whom, and how.
Sure, you could point to a billion-dollar computer company that outsources production overseas and say, “There. That’s how computers are built.” And you’d be right. That system does work. But not for everyone—and that’s a problem.
Instead of relying on foreign labor, we can combine cutting-edge technology with human ingenuity to produce high-quality products right here at home. Here’s how.
Make Your People a Priority
A manufacturing process that puts people at the center of it all—both literally and figuratively—is the difference between American manufacturing and foreign-based production. So, if you’re deciding how to implement automation in your manufacturing process, make sure your decision will benefit both the process and the people performing within it. Why does putting a premium on people matter? Two points to consider:
- Even though it seems logical to choose better, faster, and stronger technology to enhance production—you must first consider the impact it will have on your human workforce. Cobotics, for example, must create opportunities for people to contribute as collaborators and as individuals. If your people are merely cogs in the machine, you’re minimizing their potential to make meaningful breakthroughs that can improve your processes and boost morale at the same time.
- We’ve all seen videos and heard horror stories about what it’s like to work in extremely cramped and highly automated electronics factories. At my company we’ve created comfortable and collaborative workstations that enable our technicians to put a more personal touch on the production process. With the freedom to make more meaningful contributions and the power to propose new methodologies that improve processes, our technicians can do what cobots can’t: dream, imagine, and create.
Automate Processes with a Purpose
Many people assume that automation is threatening to a human workforce, but that isn’t always true. Those of us in the manufacturing industry are learning how automation can help our human workforce—not hurt it—while simultaneously enhancing productivity. It’s not only possible; it’s practical.
- For example, by implementing cobotics, we eliminate tasks that are typically too dull, dirty, dangerous, or difficult for humans to perform. Why ask a person to pick up and screw in a thousand tiny screws all day when the cobot can do it—with more precision and less anguish—in seconds? The point here is to replace the least desirable and most time-consuming parts of the job with a solution that streamlines processes. In this scenario, humans work in tandem with cobots to manufacture products in a safer, healthier, and happier environment. Worker satisfaction may be tough to measure, but according to economists, "happiness made employees around 12 [percent] more productive, while unhappy workers showed to be 10 [percent] less productive."
- Automation can free up extra time for your team to ask thoughtful questions, develop skills in other areas, and propose new solutions. With the opportunity to offer feedback, your team will feel encouraged participate in conversations that can lead to improvements in operations. For example:
The technicians on my team are usually the first to notice when a system or process can be improved. And since they’re encouraged to share their observations, we’re able to work together to create new solutions. As such, we’re facilitating lifelong learning, bridging the skills gap, and supporting worker satisfaction.
These conscious outcomes are mutually beneficial to both the team and the individual—not to mention the future of American manufacturing. If our technicians choose to further their careers in another technical setting, they’ll have the skill set and confidence to do so, and that’s what we should want as leaders in manufacturing.
Never Say Never
The accessibility of 3D printing, robotics, and IoT allows small players to compete with large-scale manufacturers for the first time.
The range of 3D printing, 3D design, and laser-cutting capabilities—paired with up-and-coming maker communities that offer access to basic workshop tools—makes the once impossible, possible.
Across the world, many people are realizing that you don’t need millions of dollars and a team of geniuses to demonstrate your idea and put something into use. A 10-year-old kid with a great idea, access to a cheap 3D printer and some basic hardware, and the ambition to learn something new now has the ability to spark a new technology revolution. If they can do it, why can’t you?
Those of us who have largely been left behind are beginning to realize we can do it on our own and without the need for major corporations. And it’s us who will make the most meaningful impact in our communities.
Matt Malloy is Director of Advanced Manufacturing at Bak USA.
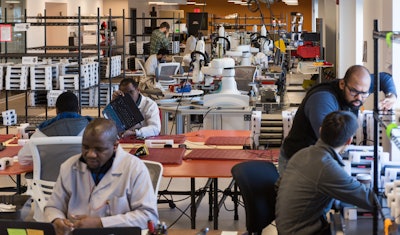