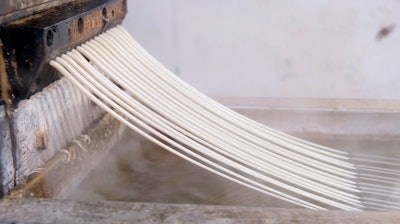
Polymer Resources Ltd., a U.S. compounder of high-quality engineering resins, announced the completion of the expansion and enhancement of its compounding facility in Rochester, New York.
To meet customers’ growing needs for engineering resins, the company upgraded an existing building on its campus to support a 40% increase in overall compounding capacity. The updated facility also features increased grinding and shredding capacity for recycling plastic waste to support circularity and sustainability.
Furthermore, its floorplan, new safety features and amenities are designed to provide a comfortable and efficient work environment for employees, whose numbers are expected to increase by double digits in the coming years.
“The updated facility will help us advance sustainability through plastic waste collection and recycling," Polymer Resources President and COO Scott Anderson said. "We are committed to helping our customers reach their production and sustainability goals, as well as meeting our own sustainability goals, and this new facility positions us to achieve those objectives.”
Greater Capacity for Compounding and Recycling
The project, which was completed in just over a year, expanded the footprint of the compounding facility from a total of 35,000 square feet, previously divided between two buildings, to 60,000 square feet in one building.
This change offers more space for compounding and grinding operations, storage, a laboratory and offices, and it improves process efficiency and streamlines workflow. Further, the Rochester site offers Polymer Resources an opportunity to add up to a total of 100,000 square feet on to the building.
To boost compounding capacity, the company has installed a new production line with a twin-screw extruder for faster throughput and advanced capabilities. This new equipment increases capacity by 40% and helps enable the efficient production of new and existing products.
A key feature of the facility is a separate, soundproofed, 3,250 square feet room for grinding and shredding post-industrial and post-consumer plastic waste for use in Polymer Resources’ sustainable resin grades.
Not only does this grinding operation use material from both the Rochester and Farmington sites, but it also accepts parts and waste material from customers and vendors for recycling. This initiative helps to divert plastic from landfills and oceans and extend its useful life.
Several end-use agreements between Polymer Resources and its customers are in place to ensure known, reliable sources of recycled content for the company’s sustainable materials portfolio.
Enhanced Work Environment
To maximize employee safety and comfort, Polymer Resources designed the facility with a powerful air filtration system, a dust collection system for the grinding operation and a modern break room. Greater space between machines also improves workers’ physical safety as they move around the production floor.
The Rochester plant compounds a wide range of engineering resins, from polyphenylene ether and polystyrene blends (PPX) to various grades of polycarbonate (PC), acrylonitrile-butadiene-styrene (ABS), polybutylene terephthalate (PBT), PC/ABS and PBT blends.
Many of these grades are available unfilled or with different loadings of mineral or glass-fiber reinforcement. The facility focuses on supplying large amounts of material, including full and partial truckloads (LTL volumes) to customers developing important applications for a variety of industries including the electrical, industrial, non-invasive medical, consumer goods, transportation and building and construction sectors.