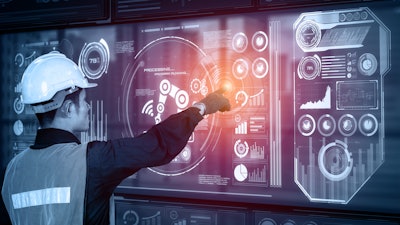
Engineers and procurement professionals want quality products quickly, but lately, companies that follow the just-in-time (JIT) manufacturing model have been struggling. This model relies on manufacturing partners to make only as many parts as are needed with little margin for error. While JIT enables companies to reduce inventory costs, it isn’t always compatible with today’s unpredictable world. This has left many searching for a new solution — and they’re finding it in the cloud.
To gain a deeper understanding of the challenges companies experience with JIT manufacturing and how cloud manufacturing can improve companies’ operations and bottom lines, Fast Radius surveyed 250 engineers, industrial and product designers, and procurement professionals. Here’s what we found.
Challenges with JIT Manufacturing
Our survey found that 32 percent of respondents are using JIT today, while 48 percent tried JIT and have moved away from it. Three core issues, all exacerbated by JIT practices, came to the front:
- Long lead times: Forty-two percent of respondents named long lead times as a top supply chain pain point, and pandemic-related shipping delays, material shortages, and factory shutdowns have only made these issues worse.
- Higher costs: Companies are currently dealing with higher material prices and costly delays, and 40 percent of our respondents cited high costs as a top pain point.
- Not enough flexibility: Thirty-five percent of respondents cited a lack of flexibility as a major pain point. The fact that many still follow a JIT strategy may contribute, as working with a limited supplier pool can make it challenging to adapt to sudden shortages or delays quickly.
What Comes Next — Cloud Manufacturing
As JIT manufacturing principles aren’t cutting it for many companies, cloud manufacturing has emerged as a solution that fixes not only issues of visibility and communication but also fulfills the need for high-quality parts at a reasonable cost, delivered on time. Cloud manufacturing offers the benefits of JIT manufacturing and more, with increased flexibility. Adopting a cloud manufacturing model can potentially enable:
- On-demand manufacturing: While JIT typically requires companies to make precise quantity projections, cloud manufacturing allows you to order parts as needed, without facing long lead times or high order minimums. Cloud manufacturing reduces the need for physical warehousing by storing designs in the cloud to produce on demand.
- Increased reliability: Since all of a part’s crucial design and manufacturing information is stored digitally, products can be made to spec repeatedly, whenever you need them.
- More flexible supply chains: Cloud manufacturing can also help the 35 percent of respondents who cited a lack of flexibility as a main pain point, as it allows manufacturers to shift production locations easily without sacrificing quality.
How do you know when it’s time to switch? And is cloud manufacturing the right choice for your business? The answers for these questions are different for every company.
In our survey, we found that those who have stuck with a JIT strategy are more likely to have found a manufacturer they trust. If JIT is working for your business — you’re avoiding the supply chain bottlenecks, rising costs, and quality problems others face — you may want to stick with your current strategy. However, if your supply chain isn’t delivering, now is the time to make a move.
When evaluating cloud manufacturers, consider the following:
- Their supplier network: Seek out a partner with a distributed network of suppliers across the globe. Having a variety of options allows you to pivot in response to regional issues.
- The tools they offer: One of the benefits of cloud manufacturing is centralized data and communication. Look for a cloud manufacturer that provides the visibility you want into your parts’ production, as well as tools to improve your parts based on manufacturing data.
- Their quality processes: A great cloud manufacturing partner should be working to ensure you receive quality parts at every step. When you first upload your design, they should provide feedback to improve manufacturability; when you manufacture that part, they should offer rigorous inspection options; and when you’re ready to re-order, they should have a record of everything needed to make your part perfectly.
The past few years have been challenging for manufacturing. Companies continue to deal with supply chain disruptions, longer lead times, and higher costs, making it difficult to keep pace. For those manufacturers who found that a JIT model led to higher budget overages, more lost revenue, and unhappy customers, it’s time to explore a different approach.
Cloud manufacturing platforms offer an appealing alternative, enabling companies to produce products and create flexible, resilient supply chains. It’s impossible to know what the future holds, but a cloud manufacturing strategy could give you the flexibility to handle any challenge.
Bobby Bott is the EVP of manufacturing at Fast Radius.