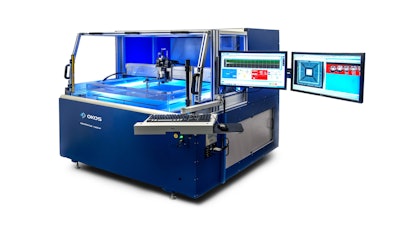
Industries with demanding metal bonding applications are increasingly relying on diffusion bonding, an essential joining method for achieving a high-purity interface between two similar or even dissimilar metals. The process involves applying high temperature and pressure to metals mated together in a hot press, which causes the atoms on solid metallic surfaces to intersperse and bond.
For similar materials bond strength approaches base material. For dissimilar materials it is a function of the intermetallic compounds formed, the thickness of the intermetallic zone and microscopic anomalies, such as voids, at the interface. To ensure the quality of the interface, materials engineers must analyze samples to validate the quality of the bond. Metrology systems are used to characterize the interface and provide a more quantitative analysis.
If either side of a welded or brazed joined assembly can be pressurized, a cursory helium leak check may be used. However, this method is more of an art and a science because it is highly dependent on user configuration and often produces inconsistent results. Also, the helium lead check cannot pinpoint the exact location of a leak: It only provides pass/fail results. Better technology and methods exist today.
Due to the imprecision of helium leak testing, experts in diffusion bonding are choosing to analyze samples through a much more advanced, data-driven inspection technique: Scanning Acoustic Microscopy (SAM).
SAM is a non-invasive, non-destructive ultrasonic testing method. The testing is already the industry standard for 100% inspection of semiconductor components to identify defects such as voids, cracks, and the delamination of different layers within microelectronic devices. Now, the same rigor of quality testing and failure analysis is being applied to validate the integrity of diffusion bonded metals.
“Unlike helium leak testing, SAM will not only indicate when there is a defect in bonding, but also indicate the location and size. It is essentially the equivalent of an x-ray inside the part, so is a much more comprehensive test method to ensure quality,” said Hari Polu, President of OKOS, a Virginia-based manufacturer of SAM and industrial ultrasonic non-destructive (NDT) systems. OKOS is a wholly owned subsidiary of PVA TePla AG, Germany and offers both manual and automated inspection systems for flat panels, thin plates, circular discs, sputtering targets and special alloys.
The Many Benefits of Diffusion Bonding and SAM
Today, diffusion bonding offers substantial benefits to various industries, such as the ability to bond dissimilar metals and high value alloys. The technology also enables advantageous applications for conformal cooling, which is used in injection molding and die casting.
The importance of designing a dissimilar metal joint often lies in a desire to expose the correct metal surface to specific environmental conditions where a single alloy may not perform as well. Another reason is to introduce material systems that are lighter in weight or provide a level of corrosion resistance that can only be achieved by “packaging” dissimilar metals.
Commercial processes of interest are titanium to iron-nickel alloys, titanium alloys to stainless steel, copper to steel and even some aluminum to metal applications. The process also enables coupling between different alloys in the same material group, such as mild steel, tool steel and Al MMC. As a result, this technology has attracted the interest of design engineers in the semiconductor, aerospace and energy industries.
Diffusion bonding also has tremendous potential applications for conformal cooling applications. The concept is to bond layers in which cooling channel geometry is optimized to dissipate heat. Various geometries and various materials benefit from such an approach. Depending on the size of the commercial press, layers can be bonded up to a stack height of 600mm.
Another application related to conformal cooling is for plastic injection molds. Conformal cooling channels are an engineered solution to facilitate the requirement for rapid cooling. Dies are typically made in 2-layer designs of tool steel and material such as stainless steel (STAVAX).
For validating the integrity of diffusion bonds, advanced, phased array Scanning Acoustic Microscopy works by directing focused sound from a transducer at a small point on a target object. The sound hitting the object is either scattered, absorbed, reflected or transmitted. By detecting the direction of scattered pulses as well as the “time of flight,” the presence of a boundary or object can be determined as well as its distance.
To produce an image, samples are scanned point by point and line by line. Scanning modes range from single layer views to tray scans and cross-sections. Multi-layer scans can include up to 50 independent layers. Depth-specific information can be extracted and applied to create two- and three-dimensional images without the need for time-consuming tomographic scan procedures and more costly x-rays. The images are then analyzed to detect and characterize flaws such as the size and location of any disbonding at the interface layer of diffusion bonded metal parts.
“OKOS has leveraged the lessons and the tight specifications from the semiconductor world and adapted our SAM scanning systems for various form factors to provide unique solutions for metals and alloys in the industrial markets," said Polu. “With this type of testing, we can inspect materials at a level one to two orders of magnitude better than helium leak detection to discover disbonding flaws and defects [at the interface] as small as 50-microns that were previously undetected.”
Companies like OKOS offer a range of SAM products from compact, tabletop units to fully automated production line systems.
When high throughput is required for 100% inspection, ultra-fast single or dual gantry scanning systems are utilized along with 128 sensors for phased array scanning. Multiple transducers can also be used to simultaneously scan for higher throughput.
“In tests with a Fortune 500 multinational company on a sample of aluminum and steel, the equipment was able to scan the material in three minutes. Before, it took them 40 minutes to do one part,” said Polu.
As important as the physical and mechanical aspects of conducting a scan, the software is critical to improving the resolution and analyzing the information to produce detailed scans. Multi-axis scan options enable A, B and C-scans, contour following, off-line analysis and virtual rescanning for metals and alloys, which result in highly accurate internal and external inspection for disbonding defects via the inspection software.
Various software modes can be simple and user friendly, advanced for detailed analysis or automated for production scanning. An off-line analysis mode is also available for virtual scanning.
“OKOS decided early on to deliver a software-driven, ecosystem-based solution,” said Polu. The company’s ODIS Acoustic Microscopy software supports a wide range of transducer frequencies from 2.25 to 230 MHz.
Polu estimates that the software-driven model enables them to drive down the costs of SAM testing while delivering the same quality of inspection results. As a result, this type of equipment is well within reach of even modest testing labs, R&D centers and material research groups.
“Every company will eventually move towards this level of diffusion bonding metal part inspection and quality control because the level of detection is far superior to helium leak detection. The increased accuracy, reliability and comprehensiveness as well as decreased cost and time involved are driving the change,” concluded Polu.
When industrial manufacturers take advantage of the higher level of failure detection and analysis, the production yield and overall reliability of products improve significantly. Projects are expedited and potential points of failure are eliminated in the field.