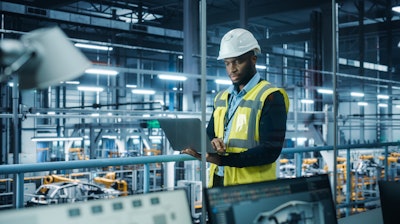
The fast-paced and dynamic manufacturing landscape has compelled brands to innovate and create a difference. The manufacturing industry will reach $944.6 billion by 2030, pacing at a CAGR of 3.3% from 2022 to 2030.
Such an ever-evolving industry demands manufacturing businesses to maintain efficiency, productivity and profitability while delivering high-quality products. However, they often encounter challenges that impede their progress and success.
From supply chain disruptions to workforce management and technological adoption, these obstacles can be daunting for any organization. Often, these challenges require intelligent solutions in terms of technology, which can be hardware and software.
In this piece, we’ll check out three common manufacturing challenges brands face and tech-enabled fixes to overcome those.
1. Inventory control
Inventory control issues in manufacturing businesses arise from inefficient raw materials management, work-in-progress and finished goods. This can lead to stockouts, overstocking and increased carrying costs, impacting production efficiency and profitability.
Monitoring inventory can be labor-intensive and often leaves scope for errors because relying on manual stock verification methods is inefficient and susceptible to mistakes. This results in discrepancies, insufficient stock, excess inventory and unaccounted damages.
Solution
Quote-to-Cash (Q2C): Technology integration in inventory control has revolutionized how manufacturers handle their inventory, improving efficiency and reducing costs. Manufacturing organizations can efficiently monitor their sales outcomes and promptly gather pending invoices by optimizing the quote-to-cash procedure. Also, maintaining comprehensive financial documentation for every transaction enables enterprises to effectively handle their stock and predict upcoming sales.
Barcode scanners: Periodic inventory assessments (including physical and cycle counts) can take the form of barcode scanning.
Barcode scanners streamline inventory management in manufacturing businesses by enabling quick and accurate data entry, reducing human error. Barcode scanners can expedite the monitoring process.
Inventory management software: Inventory supervisors must ensure an adequate supply of raw materials for production and that completed products are prepared for distribution to the final consumers.This can be efficiently achieved through inventory management software. Such software enables inventory supervisors to constantly monitor inventory levels, receive notifications when inventory nears the predetermined minimum quantity and reorder the appropriate items at the optimal moment.
Blending barcode mechanism with inventory management software: Inventory management applications can be seamlessly combined with barcode scanning devices to expedite the monitoring of stock levels and can be linked with additional platforms like procurement and financial systems. Owners of small-scale manufacturing enterprises can rest assured that cost-effective cloud-based options are available for their investment in such software.
2. Stalled Industry 4.0 efforts
The need for more skilled labor and other technological factors make it difficult to shift toward Industry 4.0. Manufacturing businesses look forward to accomplishing more with fewer resources, which may result in the early-stage transformation initiatives of Industry 4.0 being stuck in pilot purgatory.
The effort toward complete transformation may see manufacturing businesses needing more support in implementing cutting-edge technology. For instance, a Deloitte survey had 72% of executives expressing the continuous scarcity of essential resources and the sustained interruptions in supply chains as a great unpredictability factor.
Another obstacle in embracing Industry 4.0 advancements is the need for more awareness. As the scope of the technology increases, the associated risks may also shoot up. Moreover, not all organizations have leadership prepared to support and endorse innovation when outcomes may be unclear or intangible.
Tech-enabled Solutions
Bringing in the innovation: Begin integrating innovative solutions into your business, pivoting to tech collaboration in manufacturing. For instance, roping in consultants and leveraging their expertise help determine the most advanced technologies and whether your company should adopt them. They can offer essential training on the recommended technologies, ensuring you maximize your investment returns.
Involve IIoT: When leveraged effectively, the industrial internet of things (IIoT) can drive innovations and enhance return on investments (ROI).
The crucial component is the information and related services produced by IIoT. This valuable data not only highlights areas where manufacturing companies can develop new services but also aid in providing prompt repairs or upgrades as needed.
Moving to the cloud: If your manufacturing business is yet to move to the cloud, now is the right time. In the past 10 years, the number of businesses using the cloud has grown rapidly. An IDG study found that 92% of companies depend on the cloud and 87% are in manufacturing. The study indicates that these firms have gained substantial advantages from migrating to the cloud, where 70% assert that adopting the cloud has strengthened their capacity to fulfill customer expectations.
Enabling AR & VR: AR enables streamlining assembly processes by providing real-time visual guidance and overlaying 3D models on physical parts. Additionally, it enhances remote maintenance, enabling technicians to visualize equipment issues and receive expert assistance, reducing downtime and costs.
On the other hand, VR allows virtual prototyping to visualize and refine product designs before production. Moreover, it offers immersive training simulations, enabling employees to gain hands-on experience and improve efficiency in a risk-free environment.
Leveraging automation & robotics: Rance of occupations in large-scale manufacturing processes has been replaced by automation owing to rising labor expenses, heightened quality expectations and the need for expedited production. Moreover, consumers have developed more diverse preferences, prompting manufacturers to accommodate the growing demand for personalized and diverse products.
Consequently, manufacturers have integrated solutions such as advanced robotics to enhance workplace safety, streamline operations and facilitate tailored product offerings. Such widespread adoption of robotic systems for manufacturers can reduce costs, increase precision and improve safety features.
For example, automobile manufacturers use robotic arms for tasks like welding and painting, ensuring consistent quality and reducing human exposure to hazardous materials. Automated pick-and-place machines can rapidly assemble circuit boards with high precision in electronics manufacturing, accelerating production rates and reducing defects. Additionally, warehouses and distribution centers leverage automated guided vehicles (AGVs) to move materials, streamlining logistics and reducing manual labor requirements.
3. Supply chain
Supply chain administration involves orchestrating and regulating the movement of materials and data among suppliers, producers, distributors and consumers. This requires everyone in the manufacturing department to perform tasks like stock control, order completion and transportation.
Manufacturers not adopting technology face supply chain issues such as limited visibility, inefficient processes and difficulty adapting to disruptions. These businesses need solutions to monitor and optimize the flow of goods and information to lower costs, longer lead times and customer satisfaction.
Tech-enabled solutions
Using artificial intelligence (AI) and machine learning (ML): With the supply chain generating an immense quantity of data each year, companies are turning to AI-driven cloud solutions that can transform them into valuable insights. AI enables manufacturers to overcome supply chain issues by optimizing logistics, predicting demand and enhancing production efficiency.
Machine learning (ML) algorithms analyze historical data to forecast demand patterns, enabling better inventory management. Moreover, AI can identify bottlenecks, recommend alternative suppliers and streamline operations, leading to a more resilient and cost-effective supply chain.
Blockchain technology: Using blockchain for the supply chain can help create a secure, transparent and tamper-proof record of transactions and information exchange within the organization. This improves stakeholder trust, reduces fraud and simplifies processes, such as tracking and tracing, invoicing and customs clearance.
Wrapping up
The manufacturing industry is no stranger to challenges and brands must consistently adapt and innovate to stay ahead. In this piece, we have explored three key areas where companies face obstacles in terms of inventory control, Industry 4.0 adoption and supply chain management.
The tech-enabled solutions discussed above pave the way for opportunities in intelligent automation in 2023. The solutions for real-time inventory tracking, IoT integration and adopting data-driven supply chain optimization can transform a manufacturing unit.
As Industry 4.0 continues to revolutionize the manufacturing world, brands need to harness the power of these advanced technologies. In the long run, it can streamline operations, boost efficiency and ultimately create sustainable growth in the face of ever-changing market demands.
---
Hazel Raoult is a freelance marketing writer and works with PRmention. She has 6-plus years of experience in writing about business automation, entrepreneurship, marketing and all things SaaS.