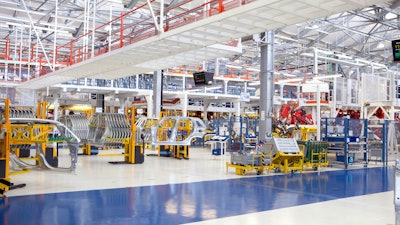
ENGIE Impact’s 2023 Net Zero Report revealed that 44% of manufacturing industry organizations have made public carbon-reduction commitments that include emissions spanning the entire value chain (i.e., Scope 3 emissions). Manufacturing, however, is one of the most carbon-intensive, hardest-to-abate industries and faces many potential barriers to achieve those goals.
In 2022, the World Business Council for Sustainable Development (WBCSD) and ENGIE Impact launched the Net Zero Manufacturing Masterclass series to bring together manufacturing leaders from around the world to discuss challenges, identify best practices, and collectively advance the effort to achieve Net Zero in manufacturing. Key insights developed during the series were consolidated into the Manufacturing Decarbonization Guidebook, which provides actionable solutions for companies to accelerate their decarbonization efforts.
Reducing overall energy use is often the most effective and efficient way companies can reduce greenhouse gas emissions and other pollutants. Seen as primarily a cost-reduction measure, reducing energy use is also one of the best decarbonization levers — enabling emissions and cost reductions simultaneously, usually with a good return on investment.
The main energy efficiency levers can be split into two complementary streams:
- Reducing final energy demand (using less energy), both through technical solutions and employee awareness to drive behavioral change.
- Optimizing utilities production (using energy more efficiently) by identifying minor system adjustments that will yield significant efficiency gains.
Avoiding Common Manufacturing Decarbonization Pitfalls
- Energy efficiency is not a one-off exercise. Decarbonization is a continuous process requiring company-wide buy-in. Identify champions at each site who will continually monitor efficiency, drive energy saving measures, and keep the team energized about meeting decarbonization targets.
- Access to CAPEX and/or financing solutions may be limited. Energy efficiency investments compete for corporate funds and may include difficult recommendations like replacing functional assets with highly efficient alternatives. It is imperative to change investment mindsets from return on investment (ROI) to total cost of ownership (TCO), which will typically show cost savings or no added cost, while also locking in future efficiency benefits.
- Energy efficiency projects must be implemented. A company can develop an energy efficiency action plan and fund it, but if those funds are put toward production instead of a well-considered efficiency model those benefits won’t materialize. Proper governance and incentives must be in place to see that corporate targets are cascaded down to individual sites.
- Site success should be scaled. While energy efficiency projects may be implemented on a site-by-site basis, tools and culture must promote the sharing of best practices with partners, creating synergies and transversality, and accelerating decarbonization at pace and scale.
Various innovative business models can support the implementation of energy efficiency programs, speed up the process and ease pressure on CAPEX.
Energy savings as a Service (ESaaS contract) targets a reduction of final energy consumption. Initial investment for upgrading a lighting system with an LED retrofit, for example, may cause delay. When done as ESaaS, a partner covers the upfront cost of the project, while the company pays a monthly fee for energy-efficient lighting. Energy savings are achieved over time without CAPEX investment required.
Utilities as a Service (UaaS contract) target the optimization of utilities production and distribution. Let’s say a company will be replacing boilers, compressors and chillers. Rather than investing in them directly, the company can purchase steam, hot water or compressed air per MWh. The energy savings are realized without up-front CAPEX and the expense may not show up on the balance sheet, while significant efficiency improvements are realized that help reduce emissions and save costs on operations and maintenance.
With both ESaaS and UaaS, the improved efficiency and cost savings can be significant if rolled out across multiple sites and multiple levers, such as HVAC, compressed air, chillers and boilers, as well as the energy demand management services that optimize them.
Ensuring Energy Savings Are Realized Through Continuous Improvement
Jason Bell, Director Sustainability Solutions-Americas, ENGIE Impact
Granular monitoring tools — referred to as energy management and information systems (EMIS) — can track energy usage and are significantly aided by artificial intelligence (AI)-enhanced software with automatic alerting and intelligent reporting, monitoring production efficiency by kWh/lb., kWh/kg or kWh/part.
It is harder to track something not consumed than something that is consumed, so it is useful to have a standard, such as the International Protocol for Measurement and Verification of Performance (IPMVP). And, of course, an established team to monitor activity and manage corrective or preventive action is vital for ongoing program improvement.