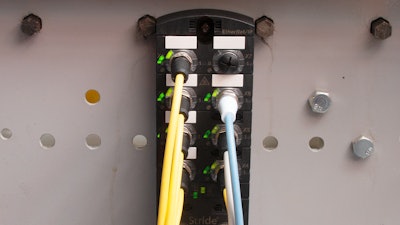
Machine and equipment builders are very familiar with using surface-mount, plug-and-cord wiring technologies. These methods provide overall cost savings and improved convenience through streamlined installations and simplified serviceability. However, traditional wired signals can only provide a single unidirectional value—discrete or analog—per wiring pair. OEMs and end users alike would find great benefit in using a digital communications technique, which would provide a way to access many values in a bidirectional manner, effectively networking field devices to a controller.
Process applications have many types of digital fieldbuses available for this purpose. However, the expense and implementation complexity of these, coupled with the fact that most types of basic machine sensor and actuator devices simply aren’t available with support for these protocols, has excluded them from consideration.
In response to these and other issues, the IO-Link protocol has been developed to provide digital communications and connectivity between input/output (I/O) modules and typical instruments, sensors, and field devices used on equipment. In turn, these intelligent I/O modules can connect with localized controllers and higher-level systems.
From Information Dirt Road to Highway
The most traditional equipment wiring methods used expensive conduit and wiring to make connections. Plug-and-cord connectivity and on-machine I/O modules greatly simplified connectivity for many types of applicable installations, but each signal of interest still typically required more wiring. Some machine-related devices, like variable frequency drives (VFDs), were available in Ethernet-capable versions, but most other basic field sensing and actuating devices have not been digitally-enabled, until recently.
A basic equipment I/O signal can be discrete (on/off) or analog (variable), and either an input to a controller (like a sensor) or an output from a controller (like a solenoid). But even the most straightforward field device might have other on-board configuration, monitoring, and diagnostic data available above and beyond the primary signal. A digital connection is needed to access this data so users can maximize the information, performance, and maintainability of their systems.
IO-Link, specified in IEC 61131-9, has been developed as a smart yet cost-effective standard to provide point-to-point bi-directional communications for typical machine and equipment use cases. It supplies 24V DC power and communications over useful distances up to 20 meters, using standard unshielded three-wire cables, and can even re-use existing wiring. Many field devices, such as photoeyes, already require this type of power to operate, provide local indication, and carry out more advanced functionality.
While IO-Link may not be quite as capable as some type of process fieldbuses or industrial communication protocols, it is a fit-for-purpose, reliable, and rapid way to transmit up to 32 bytes of device data, such as:
- Process values: provides one or more signals, input or output, discrete or analog.
- Configuration: lets users view, adjust, and upload/download device settings.
- Diagnostics: supplies extended information useful for troubleshooting devices.
Critical process values are delivered cyclically on a defined schedule. Other data, such as configuration and diagnostics, are available asynchronously as needed. Most importantly, support for IO-Link can be economically built into all types of field devices, so suppliers are providing a wide range of suitable sensors and actuators using this technology.
IO-Link Architecture and Integration
An IO-Link architecture incorporates “master modules” and sometimes “hubs” (Figure 1). Master modules support traditional and IO-Link I/O signals, and communicate to higher-level systems, while hubs aggregate traditional I/O signals into an I/O-Link format. These master and hub components are designed for open on-machine installation, with IP67-rated potted housings and key-coded M12 connectors.
Typical master modules can communicate to a controller using a standard industrial protocol like EtherNet/IP, but more advanced versions support protocols like OPC UA and MQTT so they can interact directly with the cloud, which is useful for industrial internet of things (IIoT) monitoring applications.
Some industrial-grade field devices may use dedicated IO-Link capability, but it is also quite common for a device to be capable of operating in traditional standard I/O (SIO) mode or IO-Link mode—although not both at the same time. A field device will auto-detect and work in the proper mode when connected, and the configuration will be downloaded to a new sensor. In this way, IO-Link provides simplified connectivity, much like USB devices are easily connected to a PC.
Making Smarter I/O Connections
Even though IO-Link is an established standard, users should ensure that associated products are provided with thorough electronic data sheet (EDS) files, and that the controller platform has good provisions for working with IO-Link systems. The best controller development environments will make it easy to connect with and access the wide variety of field device data (Figure 3).
---
Chris Kregoski is a product engineer at AutomationDirect in Cumming, GA., working on the Productivity PLC development and support team. He spent nearly a decade as the owner of Woodwest Controls, a small system integrator, servicing start-ups in malting, brewing, distilling, and water treatment industries.