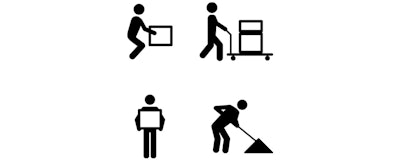
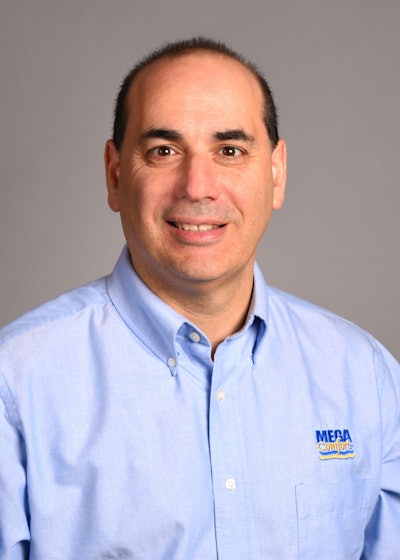
The new year is the perfect time to evaluate the ergonomic standpoint of your workplace. Implementing ergonomic practices into the workforce can make employees’ jobs and lives easier, while creating a safer workplace. Many jobs, such as ones in the industrial and manufacturing sectors, have workspaces filled with safety hazards, making a strong need for ergonomic solutions. For the year 2016, Injury Facts calculated that there were 4,398 preventable work deaths—270 of those deaths being from manufacturing jobs. Since workers at manufacturing plants often deal with heavy machinery and long hours of standing, they are extremely susceptible to injuries.
Maintaining a safe work environment by incorporating ergonomics practices, is not only vital for an employee’s well-being and productivity, but also for the employer to have smooth business operations. Here are three steps to ensure your workplace is taking proper safety measures:
Implement an Ergonomic Program
Ergonomic programs can encompass a wide range of offerings. Since operating machinery and standing are among the most dangerous threats to a manufacturing plant worker’s safety, training and personal protection equipment (PPE) should be an employer’s primary focus.
Properly training employees to use the machines correctly is the first step in keeping them from harming themselves with equipment. However, after working on the same equipment day after day, workers often get comfortable and stop putting forth the safety precautions they should be. To prevent this, employers should set up monthly training sessions to refresh workers on the importance of safety when operating machinery. There should also be a regularly scheduled machine inspection to ensure everything is running smoothly and effectively. Faulty machines are just as dangerous as careless employees.
PPE is also crucial when working in hazardous environments. Aside from the standard hard hats and safety goggles, it is important not to overlook PPE such as footwear. Prolonged and frequent standing causes blood to pool in the legs and feet, which can result in inflammation and severe pain. According to Occupational Safety and Health Administration (OSHA), most general industry incidents involve slips, trips and falls, which are often a result of inflammation and pain.
These types of injuries cause 15 percent of all accidental deaths, which falls closely behind the number one cause, car accidents. Many manufacturing plants try to aid this foot and ankle pain by installing floor matting. However, the flooring can also be a source of the problem if it is laid down incorrectly, placed in various sectors across the floor, and is unable to cover 100 percent of the surface area of the workplace. To reduce matting tripping hazards, try replacing floor matting with insoles instead. Anti-fatigue insoles provide personalized comfort that is not limited to spots with matting, but can be enjoyed wherever employees needs to go. Not only do they provide full workplace coverage, but they do not require costly maintenance and replacement. Implementing these solutions into an ergonomics program helps prevent incidents while also providing comfort and shock absorption.
Embrace the Safety Culture
Safety starts at the top—this means all plant managers and leaders should be wearing the proper PPE and behaving in a safe manner when on the floor. If upper management does not show full support of the safety culture, employees will tend to follow that example. To best express safety as part of the workplace culture, it is important to embrace it daily.
Examples of enforcing safety measures include hanging bulletin boards or posters throughout break rooms and restrooms and reminding workers that taking unsafe shortcuts is never the answer. Upper management must always be on the lookout for any changes happening within the plant floor in order to be at the forefront if anything ever goes wrong. Taking extra measures by proactively checking machinery and software systems in between regulated scheduled inspections, is a great way to stay on top of potential malfunctions and injuries. Lastly, the most vital way to embrace safety is to talk to employees. Training often comes in the form of videos, but having open and honest discussions about those videos will resonate best with workers. Be verbal so everyone has a chance to comment or express questions or concerns.
Continue to Grow the Safety Culture
Many manufacturing plants and warehouses count the number of days they’ve gone without serious injuries. To keep work-related injuries low, it is important to not only keep up with standard safety regulations, but to enhance existing safety programs. While many companies already have safety programs in place, few incorporate ergonomic solutions.
The new year is the perfect time to reevaluate your workplace safety standards and see where you can go above and beyond. If you don’t have an ergonomic program in place, start offering your employees solutions like insoles to help support their feet during long floor shifts. And if you do have an ergonomics program, figure out how you can revamp it and continue to enhance it, because ergonomic solutions prove to benefit employers as much as they do employees.
Dr. Kevan Orvitz is Founder & President of MEGAComfort.