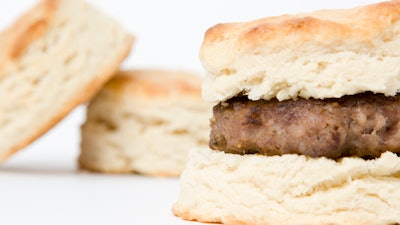
BIRMINGHAM, Ala. — The U.S. Department of Labor has found that an Alabama sausage manufacturer again exposed workers to deadly hazards at an Attalla worksite.
A follow-up inspection by the department’s Occupational Safety and Health Administration of Dean Sausage Co. Inc. found similar workplace safety hazards as identified in a Dec. 8, 2022, inspection, allowing workers to be exposed to hazards related to lockout/tagout, machine guarding, hazard communication and blocked exits.
The current inspection led OSHA to cite the employer with seven repeat violations for exposing employees to struck-by and caught-in hazards by failing to develop and use machine-specific lockout/tagout procedures and by not maintaining machine guarding. In addition, Dean Sausage failed to maintain clear exits, and to implement a written hazard communication program, including worker training, for those working with hazardous chemicals. The employer also did not maintain required safety data sheets for the materials.
OSHA also cited the company with two serious violations for lacking lockout/tagout procedures to protect employees before they cleared a machine’s bread cutter.
OSHA has proposed $116,153 in penalties.
In the initial 2022 inspection, OSHA cited Dean Sausage Co. for a total of 14 violations and assessed the company with more than $37,000 in proposed penalties. Established in 1955, Dean Sausage Co. Inc. employs 85 workers at its Attalla facility. The employer produces meat products, including sausage and frozen biscuit sandwiches distributed to retailers throughout the southern U.S.
OSHA’s investigation is part of its National Emphasis Program to focus enforcement efforts on amputation hazards in manufacturing industries. A NEP is a temporary program that focuses agency resources on particular hazards and high-hazard industries. The NEP on amputations targets industrial and manufacturing workplaces where OSHA has determined that unguarded or improperly guarded machinery and equipment played a role in employee injuries. OSHA also seeks to raise awareness of amputation hazards in the state’s manufacturing industry through a concerted education and prevention effort.
“The bottom line for any company is they must keep their workers safe,” said OSHA Area Office Director Joel Batiz in Birmingham. “Employers have a legal obligation to put worker safety before profit and to do all they must to make sure every employee ends their shift safely. The fact that Dean Sausage Co. has allowed employees to be exposed to hazards for which we cited them in the past raises real concerns. Their latest failure is unacceptable and OSHA will hold the company accountable.